Hazardous dusts are inevitably encountered in the pharmaceutical industry. Containment measures are implemented to reduce the risk of contamination and thus also provide greater employee protection. The aim of these is to form a protective area for employees and the environment. Among other things, dedusting systems are used that extract, filter and safely separate the dust as it is generated. However, since the extracted dust was not transported away, but only from the point of capture into the plant, dust collection systems should also be equipped with containment measures.
In this article, you will learn which technical measures you can implement in the pharmaceutical industry to reduce the risk of contamination and thus ensure greater employee protection.
Technical measures
Operators of production facilities have a duty to protect employees from hazards during their daily work. This obligation can be met by considering technical containment solutions when planning a plant.
According to Directive 98/24/EC, the so-called “STOP” principle must be taken into account when selecting the containment measures in question:
- Substitution ofthe risky substance – Checking whether there are substances that are less toxicological
- Technicalmeasures – upgrading plants with appropriate safety solutions
- Organizationalmeasures – planning so that employees are not exposed to hazardous substances for too long
- PersonalProtective Equipment – Use when all other measures are not applicable.
The measures used in the pharmaceutical industry are divided into two groups:
Primary containment measures and secondary containment measures.
While the primary containment measures directly ensure that no hazardous dusts can escape from the production facilities, the secondary measures serve to trap particles that nevertheless occur from the production facilities or to prevent them from spreading. However, each case must be examined individually to determine which containment measures are appropriate. The decisive factor is always the exposure or hazard posed by the resulting dusts, as well as the (legal) requirements that must be observed (e.g. GMP, HSE).
In order to determine the risk and thus the scope of the measures, a risk assessment is mandatory. In this, the degree of exposure to the corresponding substance is related to the exposure (duration of exposure).
The goal is to prioritize technical measures that provide optimal protection for employees. Meaningful solutions adapted to each phase of the product life cycle should be sought. It is therefore not only necessary to design the production of the product safely, but also to protect the employees during the assembly and disassembly or disposal of the production plant.
Primary containment – preventing particles from escaping
The generation of hazardous dusts during the production of medicines is unavoidable. It is safest for people and the environment if dusts and loose particles of hazardous substances do not escape from where they are generated: the production plant itself.
To achieve this, there are various technical possibilities, some of which are listed below. By combining different options with each other, employee protection can be increased in the best possible way and user-friendliness can be improved.
Glove Box, RABS and Isolator
To prevent the spread of particles, it is possible to encapsulate and enclose the area of exposure. Depending on the hazard potential, this can be realized with the following measures:
- Glove Box -Box with plexiglass pane and gloves embedded in it.
- RABS (Restricted Access Barrier System) enclosure – enclosure with integrated airflow measures
- Isolator – device in which a defined negative pressure and extremely high tightness is possible.
Extraction and filtration systems
By means of extraction systems, the air with the substances in it is extracted directly at the point of occurrence and removed from the employee’s work area. The extracted air is then filtered and thus purified of the hazardous substances. The so-called dust collectors have filter inserts that bind the particles to themselves and thus remove them from the air. The result is pure, uncontaminated air. The occurring substances as well as the amount of air to be filtered determine the number of filter elements and their filter class (which amounts of particles of a certain size are separated from the air).
Differentiation according to particle sizeSecondary containment – preventing the spread of particles
During maintenance and installation work or in the event of malfunctions in the production process, the containment may be broken and the hazardous substances may escape. For these cases, production rooms themselves are designed to minimize the risk of further spread and contamination of employees and adjacent production rooms.
The selection of options results from the analysis of the workplaces (e.g. material flow, routes of personnel, etc.) and the risk considerations of the substances that occur.
For example, the following solutions are available for secondary containment:
Work areas with air locks
The workplaces can only be reached via airlocks for decontamination. Depending on the design, separate entrances and exits can be used, or the material flow can be separated from the personnel routes. In the airlocks, people and material are cleaned of contaminants that are brought in from outside and thus pose a risk to the production process or the product. On the other hand, the use of airlocks also prevents substances from entering from the inside and contaminating the adjacent areas.
Working areas with pressure cascades
Different air pressures prevail in the individual areas, which control the movement of particles suspended in the air.
- Positive pressure – used when no substances are allowed to enter the room.
- Negative pressure – used when no substances are allowed to get out of the room
Cleanroom solutions
The cleanroom concept takes care to limit the amount of particles in the air. Various regulations come into play, all aimed at reducing contamination or facilitating cleaning. Regulations apply, for example, to:
- the nature of the surfaces – as large as possible to minimize the number of joints and facilitate cleaning
- the choice of materials – smooth surfaces
- the construction of the room ceilings – tight, with recessed lighting and ventilation.
- the flow of material – no contaminated material is allowed to leave the room unless appropriate decontamination or safe packaging takes place.
- cleaning the room air – filtration in this case is carried out by supply and exhaust air filters equipped with appropriate filter cells. Similar measures apply as for the technical measures under primary containment:
- The filter change must be carried out under certain protective measures.
- Indoor air handling (AHU) units shall be inspected and maintained regularly for performance. This applies, for example, to the performance of the filter when installed.
- By means of so-called DEHS tests, the filters are checked for their separation efficiency prior to commissioning.
Containment measures on filter systems
When designing the process and production equipment, different protection options are used for the dust collection systems:
Safe Change
According to this principle, employees can replace the contaminated filter cells of a filter system without coming into contact with the contaminated filter material itself or any dust that may have been stirred up.
1. removal of the material/used filter cell
In this case, the filter unit is equipped with a frame around the filter opening, to which a protective bag (plastic bag) is attached. When changing, a second protective plastic bag is slipped over the frame and secured airtight by means of a rubber ring.
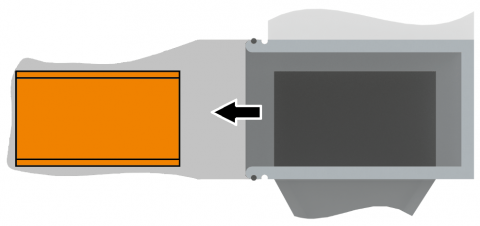
2. closing the protective bag
The filter element is pulled into the new plastic bag together with the existing protective bag (Fig. 1). This is then securely sealed between the frame and the filter cell at two points and separated between the sealing points (Fig. 2). The separated part of the protective bag with the filter cell inside can now be disposed of properly.
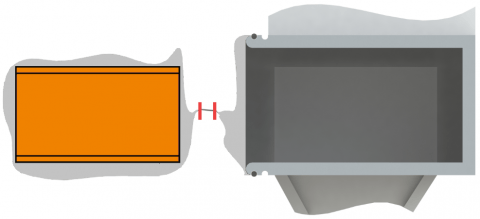
3. introduction of the new material/the new filter cell
A new filter element is then placed in a new protective bag This is then reattached to the frame of the filter opening. The remainder of the old protective bag is removed from the frame by the new protective bag and positioned behind the new cell so that it can be pushed into the filter unit (Fig. 3). The new protective bag is rolled up and stowed behind the cover of the filter opening.
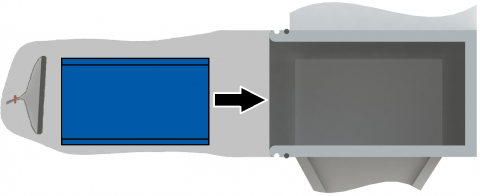
The use of the protective bags ensures that the plant remains sealed throughout the entire process and that no substances can escape. To ensure greater safety, the loaded filter cell can be wetted with water immediately before removal to achieve dust binding and adhesion to the filter cells. This again very significantly reduces possible exposure during the filter change.
Endless liner systems
A safe method of changing the dust discharge on a dust collector is an endless liner. This consists of a foil tube cartridge. The length of the film hose is such that the discharge can be emptied several times without also having to change the film hose each time.
The foil tube is closed at the bottom so that the material can fall in. After a certain filling level is reached, the film tube is securely closed above the material and cut off. It is important that the sealing takes place at two points and that the film tube is separated between the sealing points.
Closure systems
The choice of closure systems is determined by the substances encountered. There are simple systems, such as cable ties, which are sufficient for use with less hazardous substances. Since residues of the substances may still be present in the closure points, the use of special closure systems is recommended for more hazardous substances. These consist of clamps that tightly close the protective bag and special tools to separate the clamps so that no dust can escape.
Cleaning the filter system from the inside
In addition to the measures already mentioned, which are used during operation, there are also various options that are used during maintenance and repair of the equipment. For example, the interiors of plants can be washed out with water before opening to bind the dust:
Wash-In-Place (WIP):
Before opening the plant, the surfaces are wetted with water to bind the dust. For a full cleaning effect, subsequent manual cleaning is required.
Here, the inside of the plant is completely cleaned before any maintenance or repair work is carried out. In any case, cleaning must be qualified and validated for processes that come into contact with the product.
Conclusion
In the pharmaceutical industry, there are various ways to protect employees and processes from hazardous substances. These can be determined by the STOP principle. For the selection of technical measures at the dedusting plants, a prior consideration of the processes themselves as well as the occurring substances is indispensable. The resulting hazard determines the degree of containment that must be used.
In the pharmaceutical industry, applications can be divided into two groups: Primary containment measures, which ensure that no hazardous dusts escape, and secondary containment measures, which are designed to trap particles that do occur and prevent them from spreading. By combining several technical measures on the dust collectors, the user-friendliness for the employees as well as the occupational safety is increased in the best possible way and contamination is prevented.
Modern dust collectors play a dual role in this case: on the one hand, they serve as an independent, technical containment measure; on the other hand, containment measures must be taken for them to protect employees and the environment during use.