Dans l’industrie pharmaceutique, des poussières dangereuses sont inévitablement présentes. Des mesures de confinement sont mises en œuvre afin de réduire le risque de contamination et d’assurer ainsi une meilleure protection des employés. Elles ont pour but de constituer une zone de protection pour les collaborateurs et l’environnement. On utilise entre autres des installations de dépoussiérage qui aspirent, filtrent et séparent la poussière en toute sécurité dès sa formation. Cependant, comme la poussière aspirée n’a pas été évacuée, mais seulement transportée du lieu de capture vers l’installation, les installations de dépoussiérage devraient également être équipées de mesures de confinement.
Dans cet article, vous découvrirez les mesures techniques que vous pouvez mettre en œuvre dans le domaine de l’industrie pharmaceutique afin de réduire le risque de contamination et d’assurer ainsi une meilleure protection des employés.
Mesures techniques
Les exploitants d’installations de production ont l’obligation de protéger les employés contre les dangers au cours de leur travail quotidien. Il est possible de satisfaire à cette obligation en prévoyant des solutions de confinement technique lors de la planification d’une installation.
Lors de la sélection des mesures de confinement envisageables, il convient de tenir compte du principe dit « STOP », conformément à la directive 98/24/CE :
- Substitutionde la substance à risque – Vérifier s’il existe des substances moins toxicologiques
- Mesures techniques– mise à niveau des installations avec des solutions de sécurité appropriées
- Mesures organisationnelles– Planifier pour que les employés ne soient pas exposés trop longtemps aux substances dangereuses
- Équipement de protection individuelle– À utiliser lorsque toutes les autres mesures sont inapplicables
Les mesures appliquées dans l’industrie pharmaceutique sont divisées en deux groupes :
Mesures de confinement primaires et mesures de confinement secondaires.
Alors que les mesures de confinement primaires veillent directement à ce qu’aucune poussière dangereuse ne puisse s’échapper des installations de production, les mesures secondaires servent à capturer les particules des installations de production qui se produisent malgré tout ou à empêcher leur dispersion. Toutefois, il convient d’examiner au cas par cas quelles mesures de confinement sont appropriées. L’élément déterminant est toujours la charge ou le danger que représentent les poussières produites, ainsi que les directives (légales) à respecter (par ex. GMP, HSE).
Pour déterminer le risque et donc l’ampleur des mesures à prendre, il est obligatoire de procéder à une évaluation des risques. Celle-ci met en relation le degré de risque lié à la substance en question et l’exposition (durée de l’exposition).
L’objectif est d’identifier en priorité les mesures techniques qui permettent de protéger au mieux les collaborateurs. Il convient de rechercher des solutions judicieuses, adaptées à chaque phase du cycle de vie du produit. Il ne s’agit donc pas seulement d’assurer la sécurité de la production du produit, mais aussi de protéger les employés pendant le montage et le démontage ou l’élimination de l’installation de production.
Confinement primaire – empêcher les particules de s’échapper
La production de poussières dangereuses lors de la fabrication de médicaments est inévitable. La solution la plus sûre pour l’homme et l’environnement est d’éviter que les poussières et les particules détachées des substances dangereuses ne s’échappent de l’endroit où elles sont produites : l’installation de production elle-même.
Pour y parvenir, il existe diverses possibilités techniques, dont nous citons quelques-unes ci-dessous. En combinant différentes possibilités entre elles, il est possible d’augmenter au mieux la protection des employés et d’améliorer la convivialité.
Boîte à gants, RABS et isolateur
Pour éviter la propagation des particules, il est possible d’encapsuler et de confiner la zone d’exposition. Selon le potentiel de risque, cela peut être réalisé avec les mesures suivantes :
- Glove Box -Boîte avec vitre en plexiglas dans laquelle sont insérés des gants
- Boîtier RABS (Restricted Access Barrier System) – boîtier avec guidage d’air intégré Mesures
- isolateur – dispositif permettant une dépression définie et une étanchéité extrêmement élevée
Installations d’aspiration et de filtrage
Au moyen d’installations d’aspiration, l’air et les substances qu’il contient sont aspirés directement à l’endroit où ils se produisent et évacués de la zone de travail du collaborateur. L’air aspiré est ensuite filtré et donc purifié des substances dangereuses. Les dépoussiéreurs sont équipés de filtres qui retiennent les particules et les éliminent ainsi de l’air. Il en résulte un air pur et non pollué. Les substances présentes ainsi que la quantité d’air à filtrer déterminent le nombre d’éléments filtrants et leur classe de filtration (quelles quantités de particules d’une certaine taille sont séparées de l’air).
Distinction selon la taille des particulesConfinement secondaire – empêcher la dispersion des particules
Pendant les opérations de maintenance et d’installation ou en cas de perturbation du processus de production, il peut arriver que le confinement soit rompu et que les substances dangereuses s’échappent. Pour ces cas, les locaux de production eux-mêmes sont aménagés de manière à minimiser le risque de propagation et de contamination des employés et des locaux de production adjacents.
Le choix des possibilités résulte de l’analyse des postes de travail (p. ex. flux de matériaux, trajets du personnel, etc.) ainsi que des considérations relatives aux risques liés aux substances présentes.
Pour le confinement secondaire, il existe par exemple les solutions suivantes :
Zones de travail avec sas à air
Les postes de travail ne peuvent être atteints que par des sas de décontamination. Selon le modèle, il est possible d’utiliser des entrées et des sorties séparées ou de séparer le flux de matériel des trajets des personnes. Dans les sas, les personnes et le matériel sont d’une part nettoyés des contaminations qui sont apportées de l’extérieur et qui représentent donc un danger pour le processus de production ou le produit. D’autre part, l’utilisation de sas permet également d’éviter que des substances ne passent de l’intérieur vers l’extérieur et ne contaminent les zones adjacentes.
Zones de travail avec cascades de pression
Chaque zone est soumise à des pressions d’air différentes, qui permettent de contrôler le mouvement des particules en suspension dans l’air.
- Pression positive – utilisée lorsqu’aucune substance ne doit pénétrer dans la pièce
- Dépression – utilisée lorsqu’aucune substance ne doit sortir de la pièce
Solutions pour salles blanches
Le concept de salle blanche veille à limiter la quantité de particules présentes dans l’air. Différentes règles entrent en jeu, qui ont toutes pour objectif de réduire la pollution ou de faciliter le nettoyage. Des prescriptions s’appliquent par exemple à :
- la nature des surfaces – aussi grandes que possible, afin de réduire au maximum le nombre de connexions et de faciliter le nettoyage
- le choix des matériaux – les surfaces lisses
- la construction des plafonds des pièces – étanches, avec éclairage et ventilation encastrés
- le flux de matériel – aucun matériel contaminé ne doit quitter la pièce, à moins d’une décontamination appropriée ou d’un emballage sûr.
- l’épuration de l’air ambiant – dans ce cas, la filtration est assurée par des filtres d’entrée et de sortie d’air équipés de cellules filtrantes appropriées. Des mesures similaires aux mesures techniques sous le confinement primaire s’appliquent :
- Le remplacement du filtre doit être effectué en respectant certaines mesures de protection.
- Les appareils de ventilation et de climatisation (VMC) doivent être régulièrement contrôlés et entretenus en ce qui concerne leurs performances. C’est le cas, par exemple, de la performance du filtre lorsqu’il est installé.
- Le degré de séparation des filtres est contrôlé avant la mise en service au moyen de tests dits DEHS.
Mesures de confinement sur les installations de filtrage
Lors de la conception des installations de processus et de production, différentes possibilités de protection sont utilisées pour les installations de dépoussiérage :
Changement sûr
Selon ce principe, les collaborateurs peuvent remplacer les cellules filtrantes contaminées d’une installation de filtrage sans entrer en contact avec le matériau filtrant contaminé lui-même ou avec la poussière éventuellement soulevée.
1. retrait du matériau/de la cellule filtrante usagée
Dans ce cas, un cadre entoure l’ouverture du filtre et un sac de protection (sac en plastique) y est attaché. Lors d’un changement, un deuxième sac de protection en plastique est placé sur le cadre et fixé hermétiquement à l’aide d’un anneau en caoutchouc.
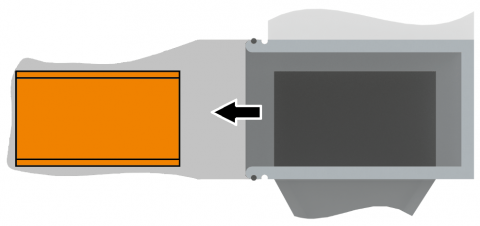
2. fermeture du sac de protection
L’élément filtrant est tiré dans le nouveau sac en plastique avec le sac de protection déjà présent (image 1). Celui-ci est ensuite fermé de manière sûre en deux endroits entre le cadre et la cellule filtrante et séparé entre les points de fermeture (figure 2). La partie détachée du sac de protection avec la cellule filtrante qu’il contient peut maintenant être éliminée correctement.
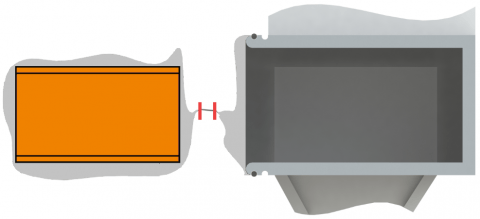
3. introduction du nouveau matériau/de la nouvelle cellule filtrante
Ensuite, un nouvel élément filtrant est placé dans un nouveau sac de protection. Celui-ci est ensuite à nouveau fixé au cadre de l’ouverture du filtre. Le reste de l’ancien sac de protection est retiré du cadre par le nouveau sac de protection et positionné derrière la nouvelle cellule, de sorte que celle-ci puisse être glissée dans le système de filtration (image 3). Le nouveau sac de protection est enroulé et rangé derrière le couvercle de l’ouverture du filtre.
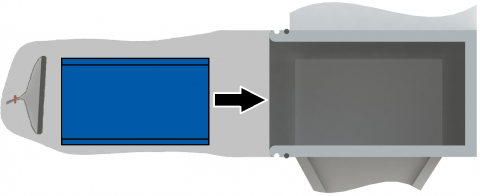
L’utilisation des sacs de protection garantit tout au long du processus que l’installation reste fermée et qu’aucune substance ne peut s’échapper. Pour garantir une plus grande sécurité, il est possible d’humidifier la cellule filtrante chargée avec de l’eau juste avant le démontage afin d’obtenir une fixation de la poussière et une adhérence aux cellules filtrantes. Cela réduit encore plus l’exposition potentielle lors du changement de filtre.
Systèmes de gaines sans fin
Une méthode sûre pour changer l’évacuation des poussières sur une installation de dépoussiérage est une gaine sans fin. Celui-ci se compose d’une cartouche de film tubulaire. La longueur du tuyau de film est calculée de manière à ce que la décharge puisse être vidée plusieurs fois sans devoir changer le tuyau de film à chaque fois.
Le film tubulaire est fermé à son extrémité inférieure, ce qui permet au matériau de tomber à l’intérieur. Une fois qu’un certain niveau de remplissage est atteint, le film tubulaire est fermé et séparé en toute sécurité au-dessus du matériau. Il est important que la fermeture s’effectue à deux endroits et que le film tubulaire soit séparé entre les points de fermeture.
Systèmes de fermeture
Le choix des systèmes de fermeture est déterminé par les substances qui apparaissent. Il existe des systèmes simples, comme les colliers de serrage, qui sont suffisants pour une utilisation avec des substances moins dangereuses. Comme des résidus de substances peuvent encore se trouver dans les points de fermeture, il est recommandé d’utiliser des systèmes de fermeture spéciaux pour les substances plus dangereuses. Ceux-ci se composent de pinces qui ferment solidement le sac de protection et d’outils spéciaux pour séparer les pinces de manière à ce que la poussière ne puisse pas s’échapper.
Nettoyage de l’intérieur du système de filtration
Outre les mesures déjà mentionnées qui sont utilisées pendant l’exploitation, il existe également diverses possibilités qui sont utilisées lors de l’entretien et de la réparation des installations. Par exemple, l’intérieur des installations peut être lavé à l’eau avant d’être ouvert afin de fixer la poussière :
Wash-In-Place (WIP) :
Avant d’ouvrir l’installation, les surfaces sont mouillées avec de l’eau afin de lier la poussière. Pour obtenir un effet de nettoyage complet, il est nécessaire de procéder ensuite à un nettoyage manuel.
Clean-In-Place (CIP) :
Ici, l’intérieur de l’installation est entièrement nettoyé avant d’effectuer des travaux de maintenance ou de réparation. Dans tous les cas, le nettoyage doit être qualifié et validé pour les processus en contact avec le produit.
Conclusion
Dans l’industrie pharmaceutique, il existe différentes possibilités de protéger les collaborateurs et les processus contre les substances dangereuses. Ceux-ci peuvent être déterminés par le principe STOP. Pour choisir les mesures techniques à prendre sur les installations de dépoussiérage, il est indispensable d’examiner au préalable les processus en eux-mêmes ainsi que les substances qui apparaissent. Le danger qui en résulte détermine le degré de confinement à mettre en place.
Dans l’industrie pharmaceutique, les applications peuvent être divisées en deux groupes : Les mesures de confinement primaires, qui veillent à ce qu’aucune poussière dangereuse ne s’échappe, et les mesures de confinement secondaires, qui visent à capturer les particules qui se présentent malgré tout et à empêcher leur propagation. La combinaison de plusieurs mesures techniques sur les installations de dépoussiérage permet d’augmenter au mieux la convivialité pour les collaborateurs ainsi que la sécurité au travail et d’éviter la contamination.
Les installations de dépoussiérage modernes jouent dans ce cas un double rôle : d’une part, elles servent de mesure de confinement technique autonome ; d’autre part, des mesures de confinement doivent être prises pour elles afin de protéger les employés et l’environnement pendant leur utilisation.