Confinement par des systèmes de filtration – protection des employés dans l’industrie pharmaceutique : dans de nombreux secteurs industriels, la poussière est une sorte de substance dangereuse en raison de sa composition et constitue donc un problème majeur. Dans l’industrie pharmaceutique en particulier, la composition de la poussière et l’exposition quotidienne des employés à la poussière est un sujet important, car les particules générées lors de la production se trouvent dans l’air sur le lieu de travail. Sans autre mesure de protection, ils peuvent ainsi pénétrer dans les voies respiratoires des employés et, dans certaines circonstances, entraîner de graves conséquences pour leur santé. C’est pourquoi la protection des employés – par exemple dans l’environnement de la production de comprimés – est particulièrement importante, car d’une part, le mécanisme d’auto-nettoyage des voies respiratoires ne peut plus maîtriser ou évacuer seul une trop grande quantité de poussières et, d’autre part, les substances actives utilisées peuvent devenir un danger si les employés y sont exposés pendant une période prolongée.
Pour savoir comment protéger vos collaborateurs contre les poussières dangereuses, consultez notre article de blog.
Confinement par des systèmes de filtration – une protection efficace des employés dans l’industrie pharmaceutique
Lors de la fabrication de médicaments, il s’agit d’éliminer les particules soulevées dans l’air afin qu’elles n’entrent pas en contact avec les collaborateurs. Il existe différentes mesures pour protéger les travailleurs lors de la fabrication de produits pharmaceutiques. Dans l’environnement pharmaceutique, cette forme de protection des employés est appelée confinement.
Le processus de production joue un rôle important dans le choix d’une mesure de confinement appropriée :
- Il existe des solutions pour salles blanches dont l’objectif est de ne pas laisser la poussière s’échapper dans l’air ambiant.
- Des séparateurs et des sas installés à l’intérieur des lignes de production garantissent que la poussière produite reste là où elle est produite et ne se propage pas.
- Pour créer un environnement sûr, il est également possible de purifier l’air.
Les systèmes de filtration ou de dépoussiérage spéciaux constituent une solution efficace dans ce cas. Grâce à leur technique de filtration particulière, ils éliminent même les particules les plus fines de l’air et créent ainsi un air très pur.
Il existe un grand choix d’installations de filtrage des poussières. Pour les processus de production de comprimés présentés ici, les installations de dépoussiérage qui, grâce à un système de captage des poussières approprié, veillent à ce que les particules soient captées par effet d’aspiration peu après leur tourbillonnement et séparées dans l’installation de filtrage par un système de tuyauterie, conviennent parfaitement. Pour que l’air chargé de poussières lors de la fabrication de granulés de poudre, par exemple, ne soit pas rejeté dans l’environnement, on utilise des dépoussiéreurs d’air actifs. Ces installations de dépoussiérage sont souvent placées à la fin du processus, elles absorbent le gaz dit brut (= air chargé de poussière) et séparent les particules de poussière du flux d’air.
L’installation de dépoussiérage sert donc en premier lieu à évacuer en toute sécurité la poussière de la zone de production et donc de la zone de danger direct pour les collaborateurs ainsi que pour leur santé. Cela souligne l’importance de la protection des employés dans l’industrie, où la sécurité sur le lieu de travail est une priorité absolue. Il est donc impératif de définir précisément les cinq critères suivants pour la sélection de ce type d’équipement et de choisir les mesures de protection appropriées pour le processus défini et avec les substances décrites afin de garantir la protection des employés.
1. classification de l’exposition aux poussières sur le lieu de travail (OEL)
Toutes les poussières ne se valent pas
La poussière dans l’industrie pharmaceutique est composée des éléments qui composent les comprimés. Outre la substance active proprement dite, il s’agit d’autres composants qui ont un impact sur les propriétés des comprimés ou des médicaments. Le risque pour les employés peut varier en fonction du composant : Le type de substance et ses composants sont décisifs pour l’exposition des collaborateurs à la santé, mais aussi la dose ou la durée d’exposition à cette substance dans le cadre du travail quotidien. Pour cela, une valeur limite d’exposition professionnelle est définie pour chaque substance, appelée OEL (Occupational Exposure Limit) – c’est-à-dire la limite de risque au sein de l’entreprise. Celle-ci indique la quantité de substance qui peut être contenue dans un mètre cube d’air pour que l’employé ne soit pas exposé à un risque pour sa santé.
Le « NOEL = No-Observable Effect Level » (niveau sans effet observable) constitue la base de l’OEL. Il indique la dose journalière à laquelle un effet critique est tout juste évité. A cette dose journalière, d’autres facteurs sont pris en compte, comme par exemple
- l’adaptation des données animales aux données humaines,
- des sensibilités différentes selon les personnes,
- la durée des études,
- la gravité des effets ou
- lorsque des effets notables sont apparus malgré l’observance.
Il en résulte l' »ADE=Acceptable Daily (Worker) Exposure ». Il s’agit de la dose journalière tolérée qui – rapportée à l’air respiré pendant une journée – donne le LAO.
Dans l’industrie pharmaceutique, les études des fabricants de ces substances servent de source d’évaluation.
2. affectation des installations aux niveaux OEB (exigences de l’industrie pharmaceutique)
Si l’on ne dispose pas de suffisamment d’informations pour une substance afin de déterminer la valeur OEL et donc d’évaluer le danger, on utilise des systèmes de classification. Celles-ci permettent d’attribuer une catégorie de danger (également appelée classe ou bande) à la substance. Un système courant est celui des « Occupational Exposure Bands », en abrégé OEB. Le niveau le plus bas concerne les substances les moins actives, c’est-à-dire les substances qui ne sont pas si dangereuses, voire pas du tout dangereuses. Le niveau le plus élevé concerne les substances les plus actives, c’est-à-dire les substances pour lesquelles peu de matière suffit à constituer un danger important.
Cette catégorisation est mise en parallèle avec une classification des équipements de production à utiliser : Selon le modèle, différentes quantités de poussière peuvent s’échapper pendant le processus de production. En fonction de la classification de la substance, il faut ensuite choisir les caractéristiques des installations. Cela signifie que, par exemple, pour les substances moins actives de la catégorie OEB1, des installations avec peu ou pas de mesures de confinement peuvent être choisies pour protéger les employés, car la substance ne présente aucun danger.
En principe, il faut veiller à ce que la quantité de substance qui s’échappe de l’installation choisie soit toujours inférieure à la valeur limite de cette même substance, afin d’exclure tout risque pour les collaborateurs.
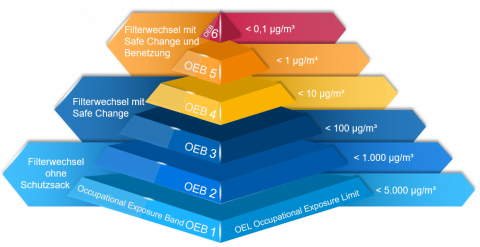
3. vérification des exigences spécifiques du système de filtration pour la production de comprimés
L’équipement du système de filtration est déterminé par la valeur OEL calculée pour les substances utilisées. Le processus complet, c’est-à-dire l’ensemble des flux de personnel et de matériel, doit être pris en considération : La section présentant les exigences les plus élevées définit le niveau de BPE pour tous les composants et donc également pour le système de filtration. Des mesures plus simples suffisent pour les substances qui sont moins critiques que pour celles qui nécessitent une classification plus élevée en raison de leur toxicité.
4. respect de l’équipement nécessaire et des mesures d’entretien des installations de filtrage
Afin de garantir la sécurité du processus pendant la production des comprimés, on utilise en grande partie des systèmes de filtres régénérables pour un dépoussiérage efficace. Dans le cas des systèmes de filtration régénérables, les éléments filtrants sont nettoyés à l’air comprimé après des périodes déterminées afin d’éviter un colmatage prématuré. Cela permet d’augmenter significativement la durée de vie du filtre. Dès que la durée de vie du filtre est atteinte, c’est-à-dire que la poussière ne peut pas se détacher du filtre malgré la régénération, celui-ci doit être remplacé. Le changement s’effectue sous des mesures de protection appropriées, qui doivent garantir que l’opérateur et l’environnement direct n’entrent pas en contact avec la substance. A cet effet, diverses mesures techniques de confinement sont disponibles pour une manipulation sûre de l’installation de dépoussiérage.
La poussière expulsée des cellules filtrantes pendant le décolmatage est collectée avec les particules de poussière plus grosses dans un collecteur de poussière. Ce récipient doit également être changé régulièrement. Comme pour le remplacement des cellules filtrantes, il est tout aussi important de respecter les mesures de confinement appropriées, en fonction de la composition de la poussière, afin de garantir la protection des employés.
5. prise en compte des conditions particulières pour les installations de dépoussiérage dans le secteur pharmaceutique
En plus des risques pour la santé liés aux composants, il y a aussi le danger lié à l’existence même de la poussière : dans les entreprises pharmaceutiques, on traite principalement des matières organiques. Ceux-ci sont généralement inflammables et font en sorte que, dans certaines conditions, il peut y avoir un risque d’explosion dans le processus. L’installation de filtrage doit donc être dotée des mesures appropriées, spécialement adaptées aux besoins de l’entreprise. Les systèmes de dépoussiérage dans une version antidéflagrante, qui répondent aux exigences de la directive ATEX 2014/34 applicable à ces installations, constituent ici une alternative.
Conclusion
Les installations de dépoussiérage modernes jouent un rôle important dans la protection de la santé de vos collaborateurs, la protection de l’environnement ainsi que la sécurité des processus lors de la fabrication de produits pharmaceutiques. Afin de faciliter le choix de l’installation de dépoussiérage adaptée à toutes les personnes concernées et de garantir ainsi à long terme la protection des collaborateurs, les critères suivants doivent être clarifiés au préalable :
- Niveau d’exposition maximal aux poussières sur le lieu de travail (OEL)
- Exigences de l’industrie pharmaceutique
- exigences spéciales pour le système de filtration pour la production de comprimés
- l’équipement nécessaire et les mesures d’entretien des installations de filtration
- conditions particulières pour les installations de dépoussiérage dans le secteur pharmaceutique
En tenant compte de ces cinq critères, vous devriez être en mesure de choisir l’installation de filtrage optimale pour les besoins spécifiques de votre entreprise, qui vous permettra de garantir un environnement pratiquement exempt de poussière et sûr pour vos collaborateurs et la production à long terme de vos produits.