
The mobile small dust extractor for flexible use in the cleanroom.

The mobile small dust extractor
As a small mobile dust extractor, the HETcompact is characterized in particular by its flexibility and efficiency. Designed for use in sensitive environments such as the pharmaceutical and chemical industries, it meets all the necessary standards to deliver optimum results even under stringent conditions.
In addition to its suitability for toxic and respirable dusts, which pose a high risk to health, the HETcompact offers outstanding functionality: the filtered clean gas is not only returned to the room air efficiently, but also safely, which is crucial for cleanroom environments. The innovative safe-change system enables filters to be changed without direct contact with dust, which significantly increases the safety of operating personnel and minimizes the risk of contamination.
Furthermore, the HETcompact is not limited to the pharmaceutical and chemical industries. Its mobile and compact design makes it a versatile device that can also be used effectively in other industries such as food processing, metalworking or workshops where clean air and dust control are crucial. Its adaptability to different working environments and its dust removal performance make the HETcompact an ideal solution for a wide range of applications where a powerful small dust extractor is required.
HETcompact
Advantages
- Up to three HEPA filter stages in one system
- Safe containment up to OEB 4
- GMP-compliant design
- Mobile, easily movable small dust extractor
- Explosion-proof housing with safe grounding
- Cleaning system for backwashing the primary filter by means of cleaning cylinder
- Plant in welded version
- Conductive equipment for almost all ATEX categories
- DEHS measuring points for qualification of the safety filter stage
Features
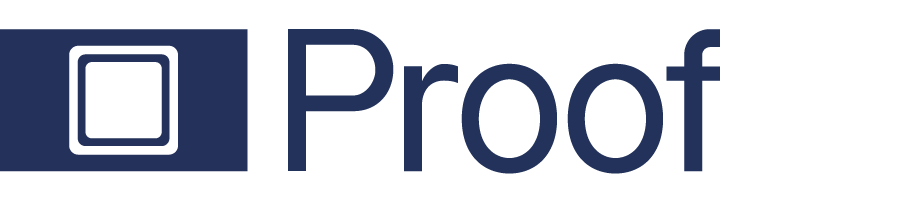
Tightness tested
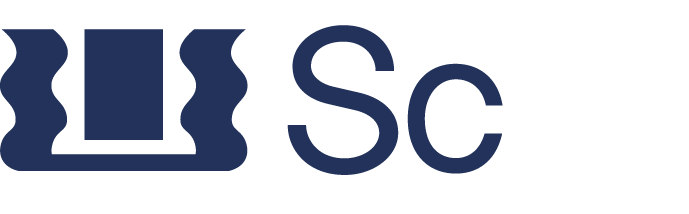
Highest containment level due to safe filter replacement
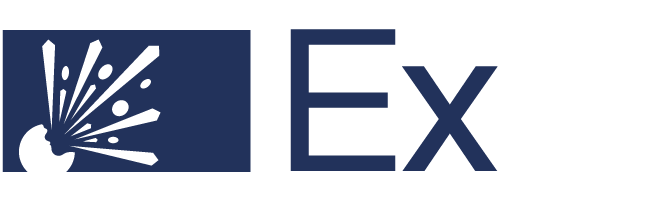
Highest explosion protection
We are happy to advise you
Get in touch with us
Jonas Röder
TECHNISCHE INFORMATION
Options
Technologies
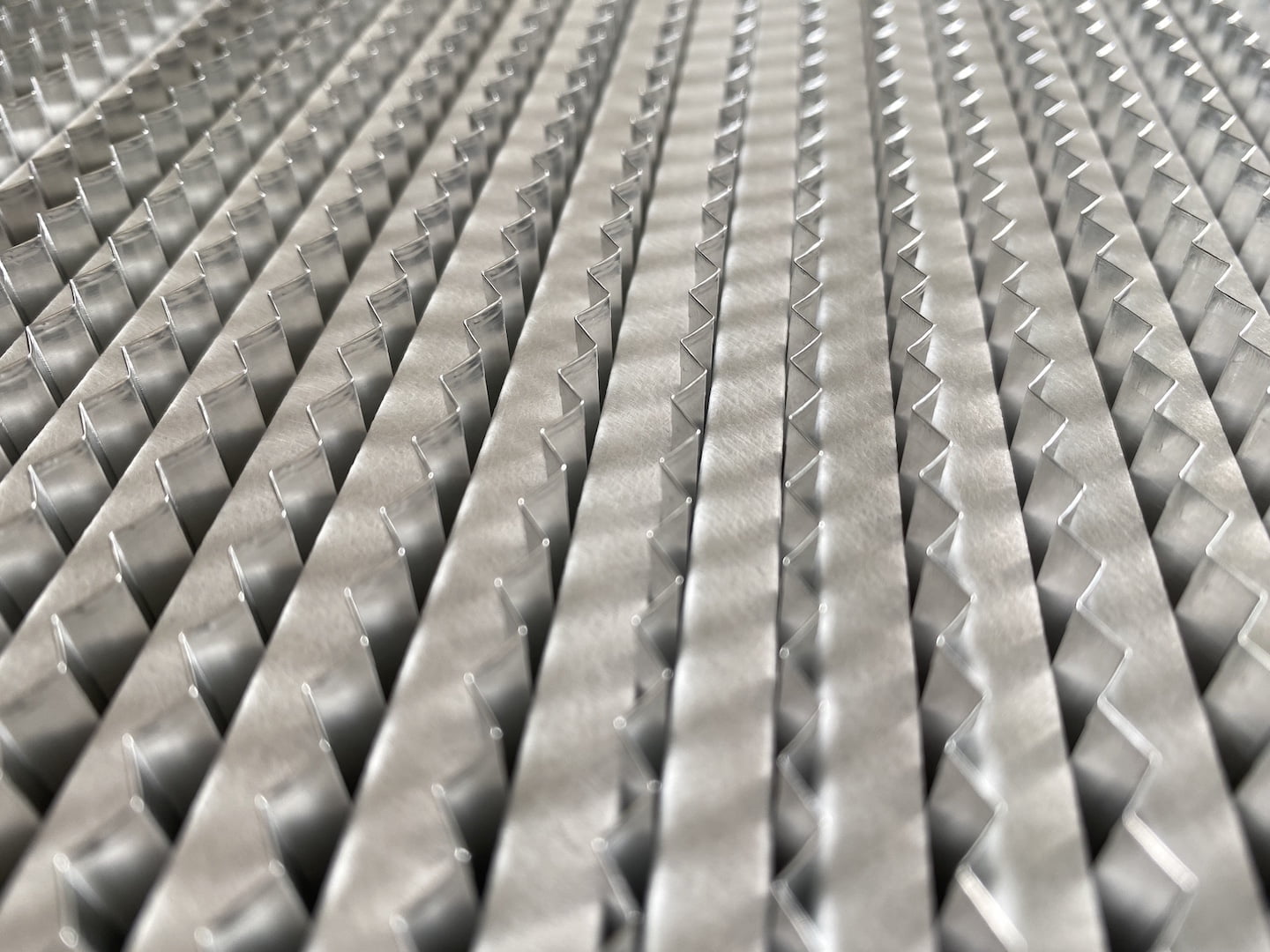
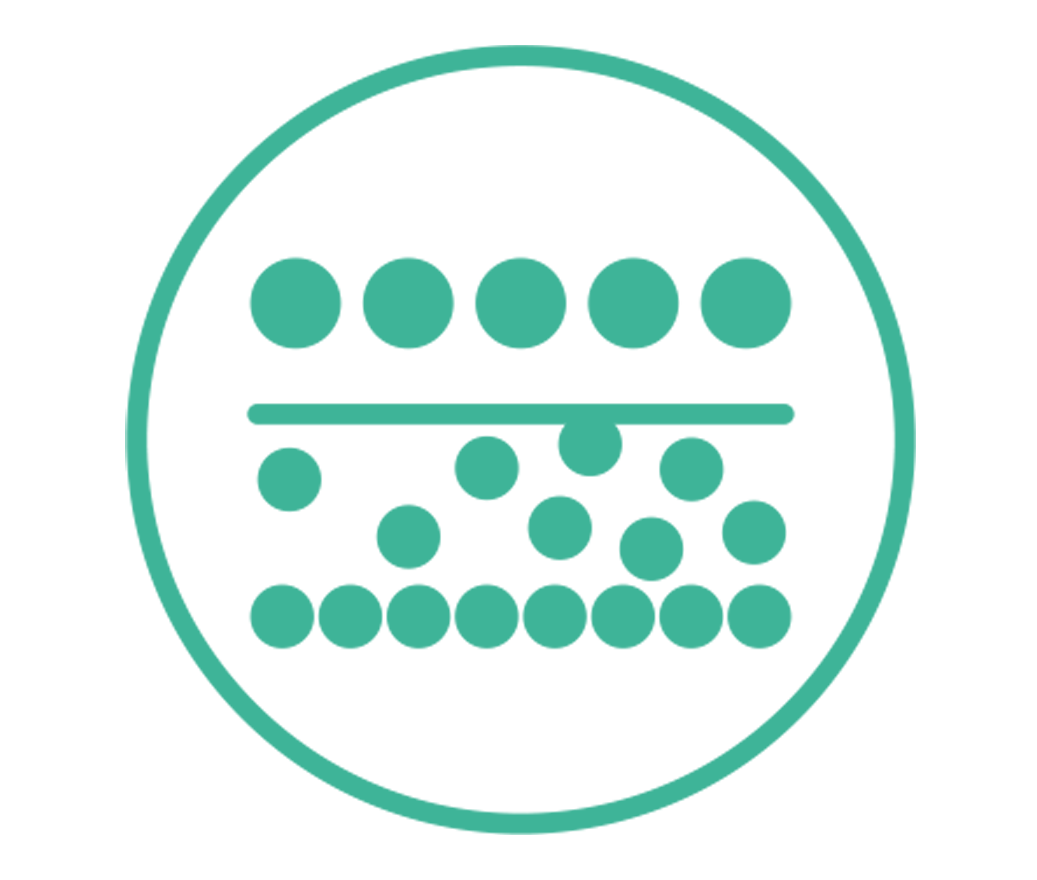
Filtration
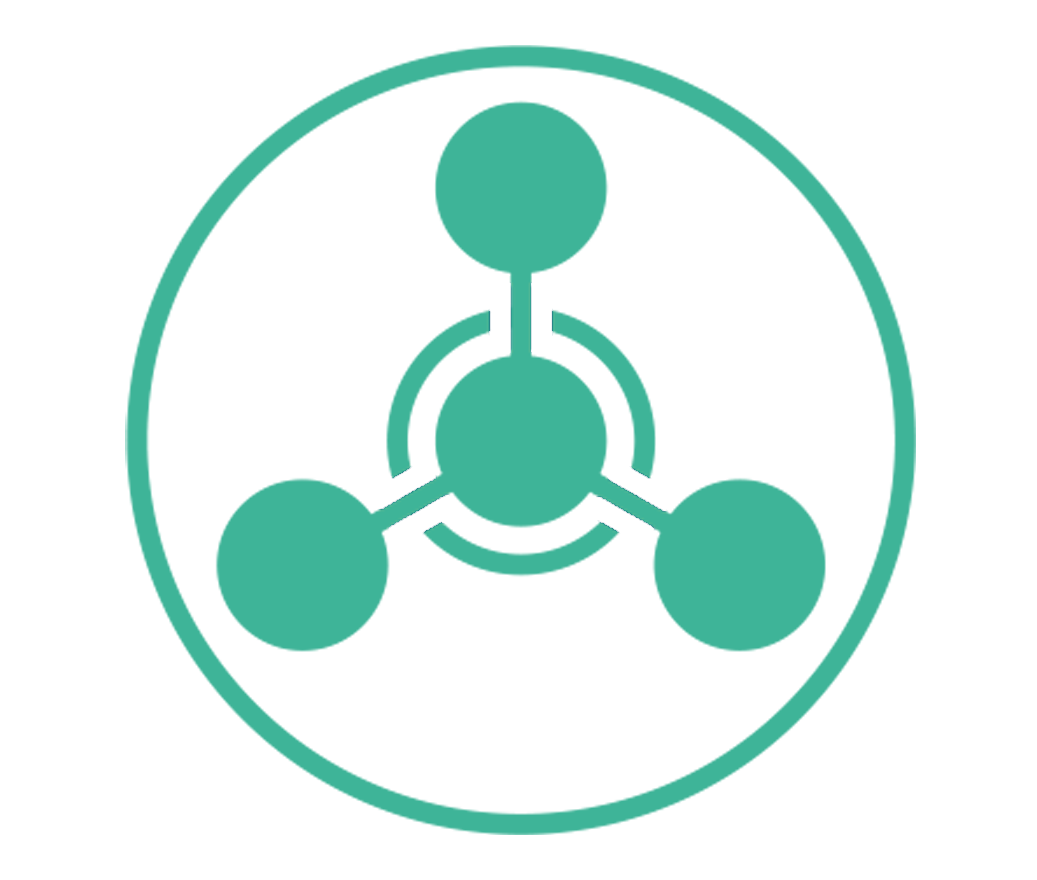
Containment
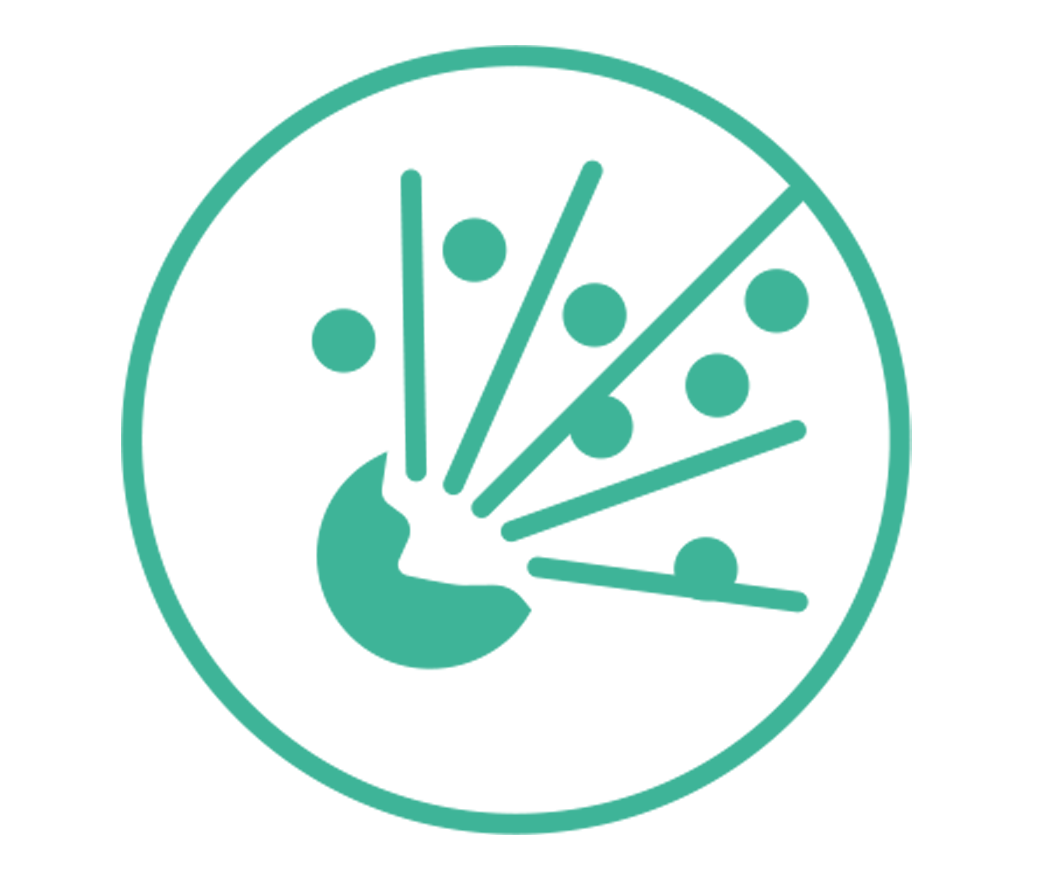
Explosion protection
other filter systems
Filter system for low dust loads
HEPA filter for highest demands
The cleanable filter system
Filter system for low dust loads
HEPA filter for highest demands
The cleanable filter system