
The static filter unit for low dust loading up to 5 mg/m³.

The static filter system
HETstatic is an innovative filter system that has been specially designed for the requirements of cleanrooms. It can be used both as a supply air and exhaust air filter system to ensure optimum air quality. Thanks to its modular design, the HETstatic system can be designed with any number of filter stages, enabling multi-stage purification of the air and thus ensuring the highest possible elimination of contaminants.
The integration of advanced technologies such as SafeChange and Wash-in-Place (WIP) sets the HETstatic filter system apart from others. SafeChange enables the filter cells to be changed safely and without contamination, which is particularly important in environments with high air purity requirements. The WIP technology also supports simple and effective cleaning of the filter cells, which simplifies maintenance and extends the service life of the system.
Thanks to its robust design, the HETstatic system is suitable for use in almost all industrial and scientific areas. Whether in the pharmaceutical industry, biotechnology, hospitals or semiconductor manufacturing – the HETstatic filter system meets the highest standards and ensures continuously clean air, which is essential to meet the strict requirements for clean rooms. The ability to configure the system up to protection level OEB 5 underlines its suitability for applications where air quality cannot be compromised.
HETstatic
Advantages
- HEPA HEPA filtration for the highest purity in the air
- Safe containment up to OEB 5
- Suitable for low dust concentrations < 5 mg/m³
- Plant in dust-tight or gas-tight design
- Conductive equipment
- Safe-change system for filter change
- Small size
- Use as a duct filter
- Especially Robust due to high sheet thickness
Features

Robust construction
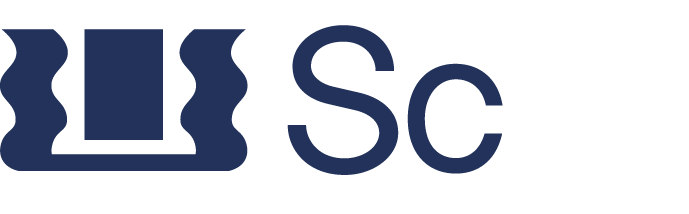
Highest containment level due to safe filter replacement
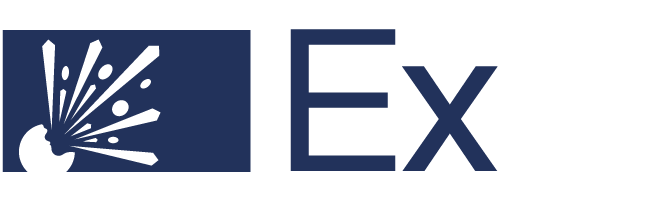
Highest explosion protection
Technical information | |
---|---|
Filter class | H13/H14 nach DIN EN 1822 |
VolumenstromVolume flow | from 250 m³/h |
Operating mode | continuous |
RohgasstaubbeladungRaw gas dust loading | < 5 mg/m³ |
Clean gas dust content | < 0,0001 mg/m³ |
Dust types | all types of dust |
Containment | bis OEB 5 |
Options
Technologies
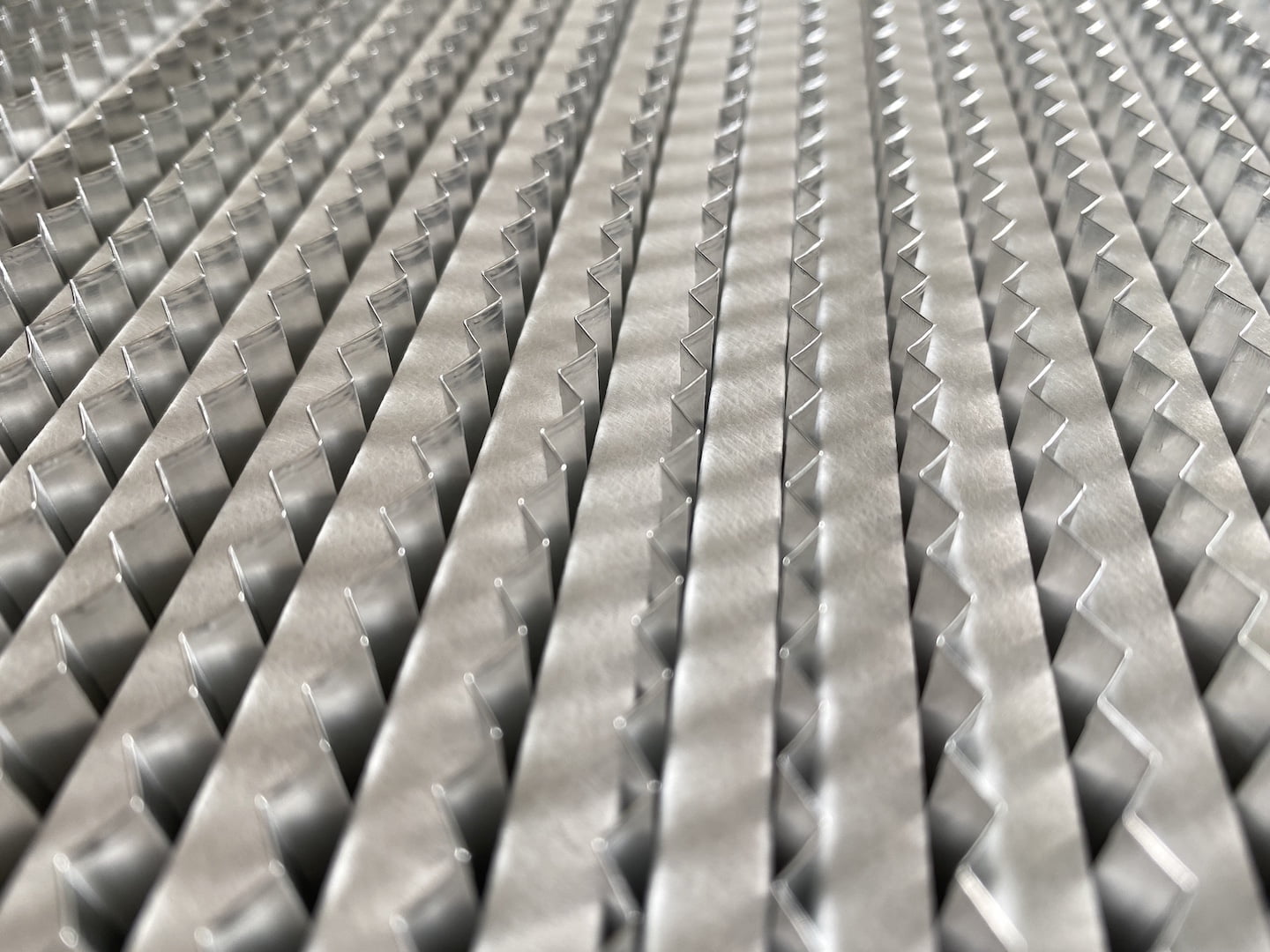
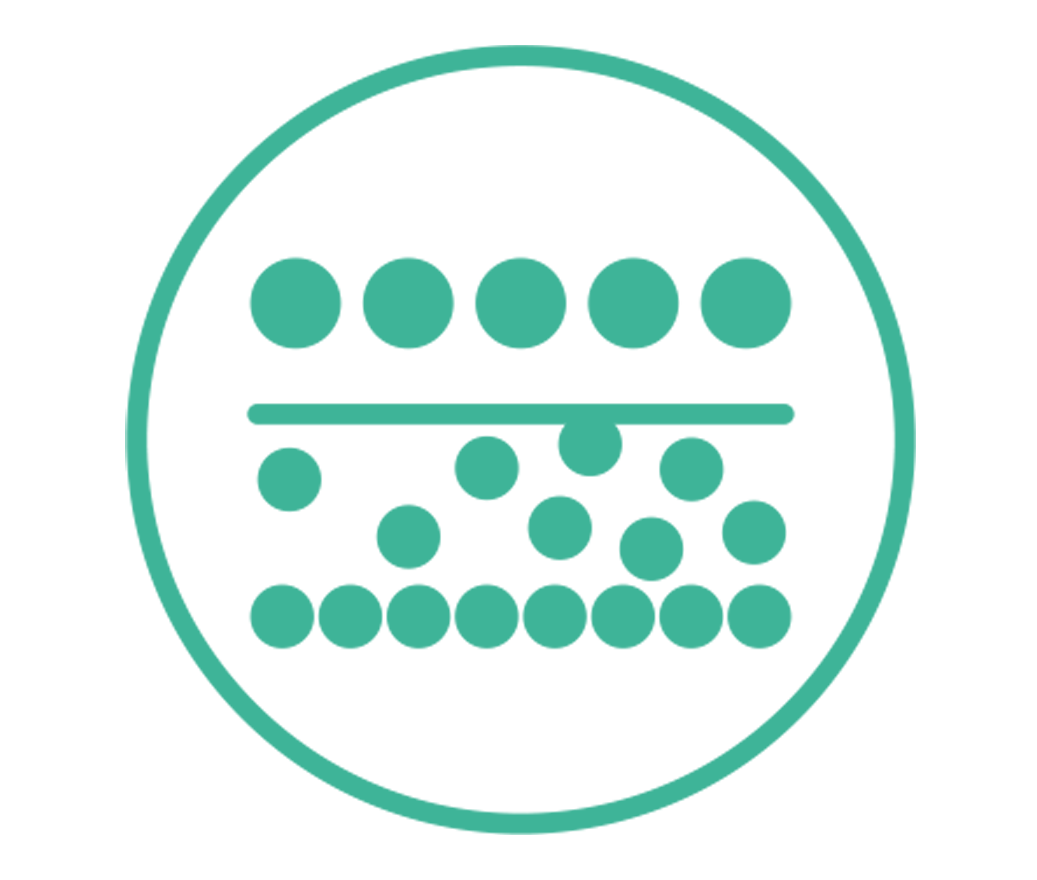
Filtration
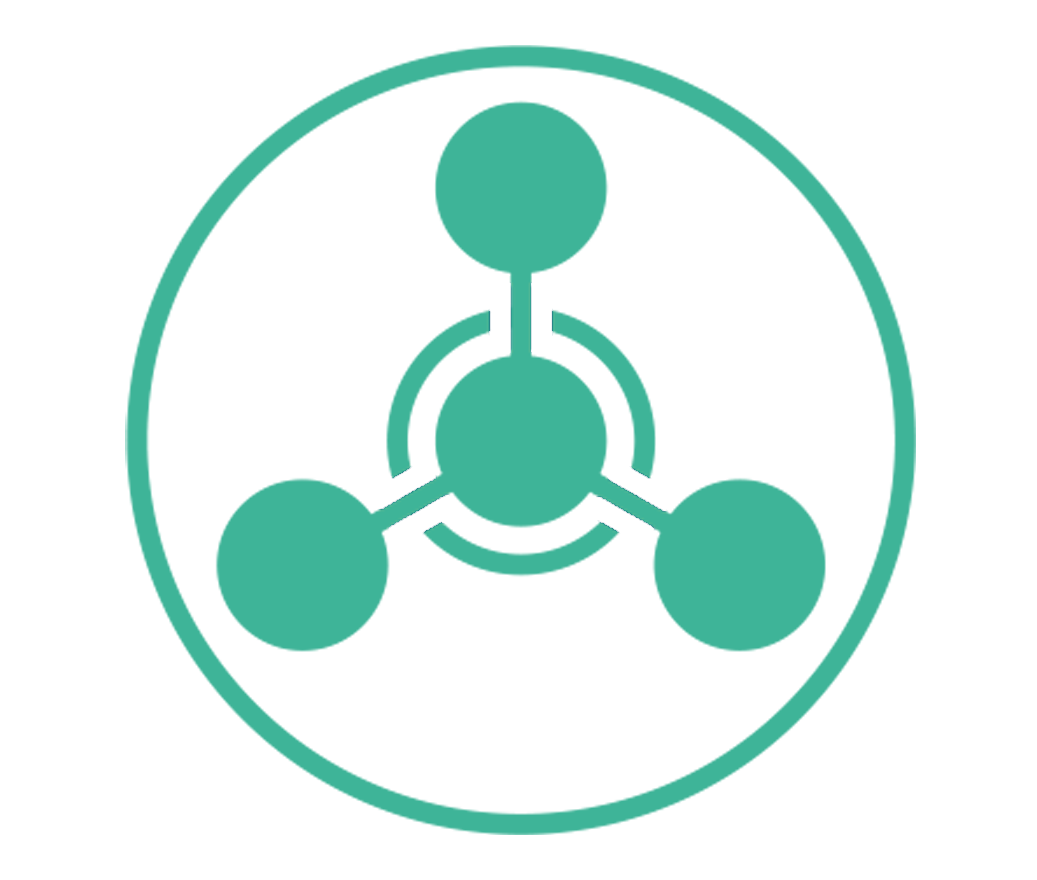
Containment
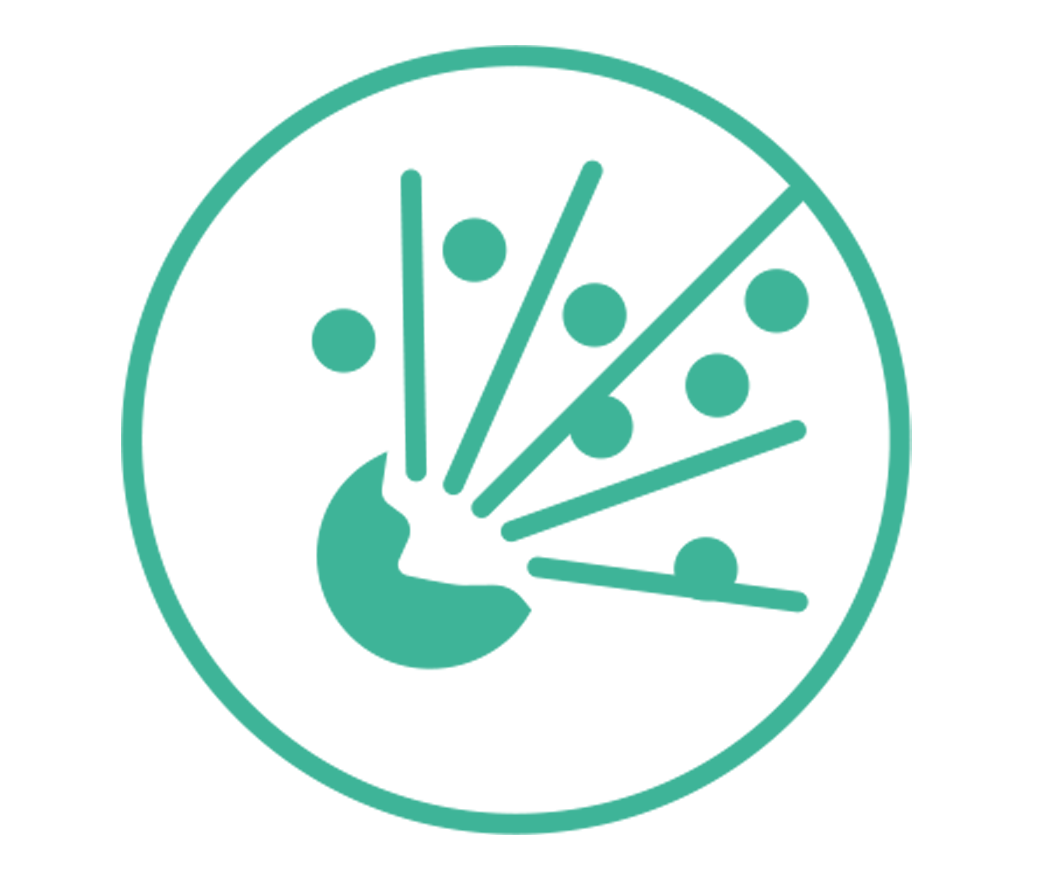
Explosion protection
other filter systems
the cleanable filter system
HEPA filter for highest demands

The mobile small dust collector

The cleanable filter system
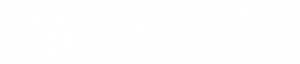
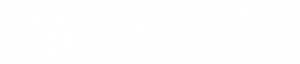
HEPA filter for highest demands

Mobile small dust extractor for flexible use