HET Features
For best protection of personnel and product
HET Features
Our experience makes the difference
The safety and reliability of our filter systems are uncompromisingly our top priority at HET Filter. Particularly in the pharmaceutical and chemical industries, where potentially hazardous substances are handled, the protection of operating and maintenance personnel is of paramount importance. We understand that the cleaning and maintenance of these systems can be associated with risks – especially the unintentional release of hazardous substances. We therefore place great importance on developing safe and user-friendly solutions that ensure the highest level of protection.
In order to meet the high demands of our customers, we rely on innovative technologies such as Restricted Access Barrier Systems (RABS) and Wash In Place (WIP). These modern solutions minimize the risk of contamination and effectively protect operating personnel from health hazards.
Our solutions are designed not only to maximize safety, but also to make the workflow efficient. In this way, we support our customers in maintaining the highest standards in terms of safety, efficiency and regulatory requirements.
TOP FEATURES
Optimally equipped for your containment requirements
Our filtration systems feature state-of-the-art technologies that ensure maximum protection and safety for operators during cleaning and maintenance.
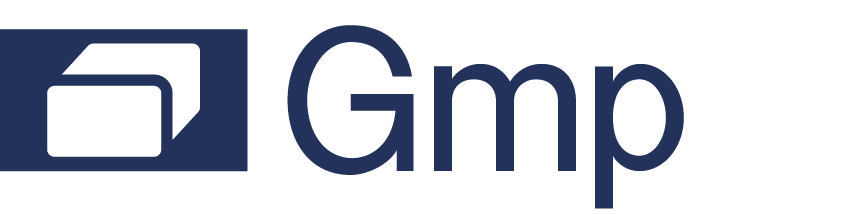
GMP compliant construction

Filter housing
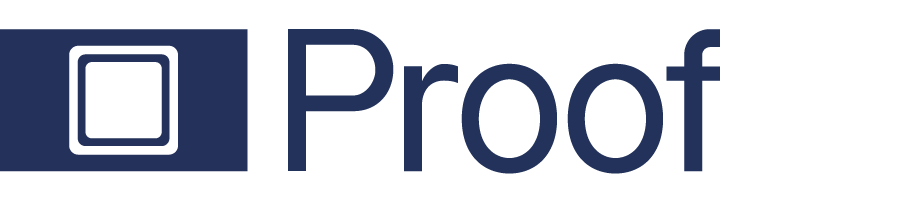
Leak test
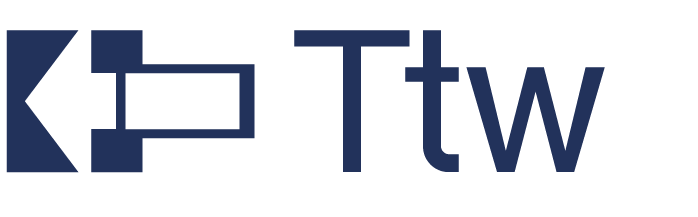
Through the wall
OTHER FEATURES
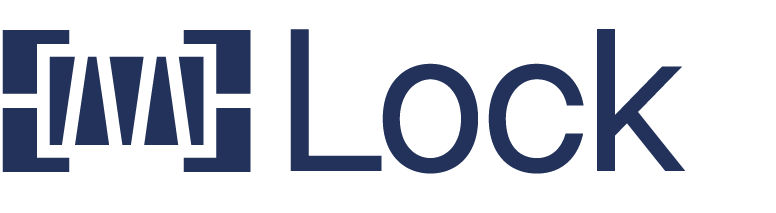
Clamping device

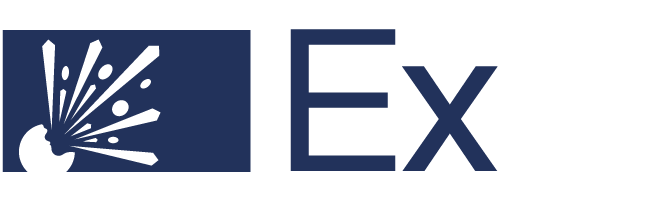
Explosion protection
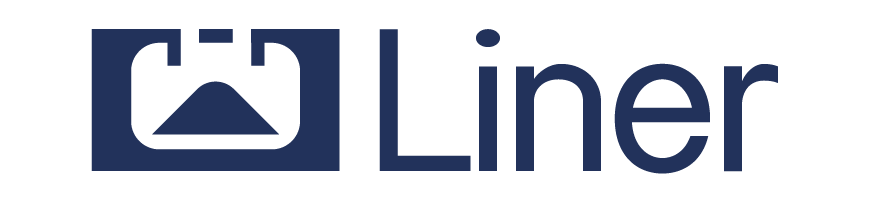
Dust discharge
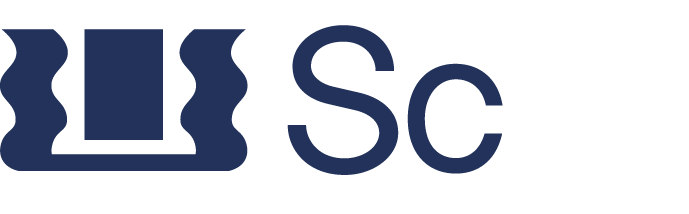
Safe Change
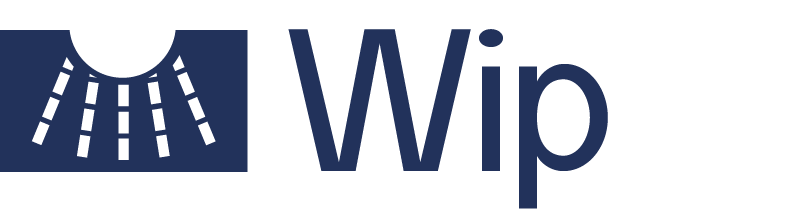
Cleaning without removal
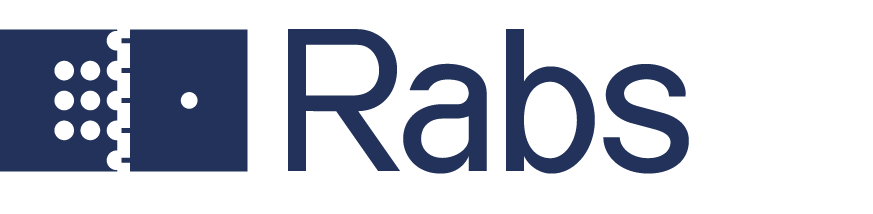
Restricted Access Barrier System
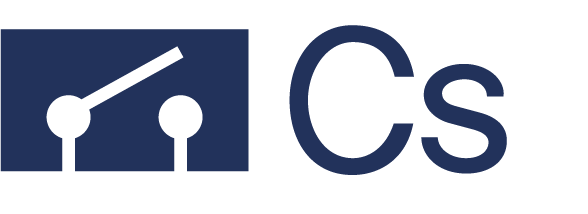
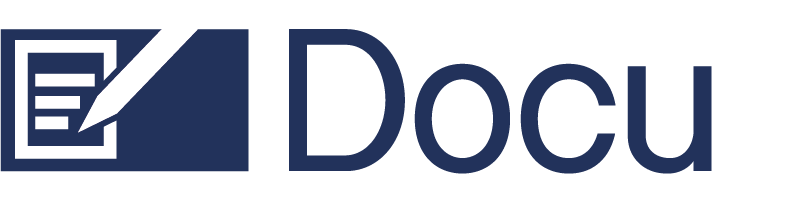
Extended documentation
Accessories and services
For safe and easy handling of your filter system
Our extensive range of accessories includes high-quality filter media, performance monitoring sensors, automated control systems and ergonomically designed control panels that optimize the efficiency and user-friendliness of our filtration systems.
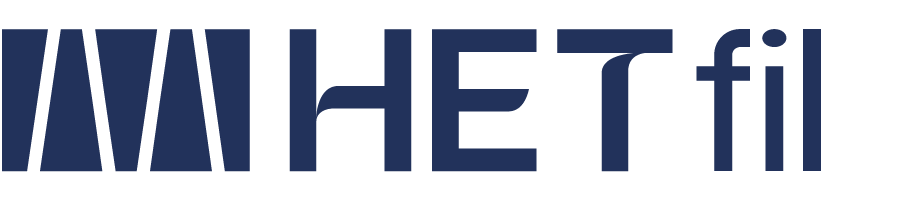
Filter systems

Filter change

Qualified DEHS measurement

For your staff
HETservices
Our service offers you comprehensive advice on the subject of filter systems
HET Filter systems
Our product variety
Tailored to your area of application, we can supply you with filter systems and filter cells from a single source. The modular design of our filter systems gives you a wide variety of options.