A containment strategy is essential when planning pharmaceutical manufacturing processes. This strategy deals in detail with the processed substances and processes in order to minimize exposure in the environment and contact with people. Such a strategy is crucial to meet the requirements of Good Manufacturing Practice (GMP) and avoid cross-contamination. The STOP principle involves dividing protective measures into different groups, which should then be applied in a fixed order. The S stands for substitution, the T, O and P for technical, organizational and personal measures.
The importance of the STOP principle
The STOP principle is a basic concept that divides protective measures into substitution, technical, organizational and personal measures. It sets out a clear sequence in which these measures should be applied to ensure the safety of employees. The idea is simple: first try to eliminate or replace the source of danger, then take technical and organizational measures, and only then consider personal protective equipment. This order of priority is also enshrined in the Occupational Health and Safety Act (§ 4 ArbSchG). It states: “Hazards must be combated at their source” and “individual protective measures are secondary to other measures”.
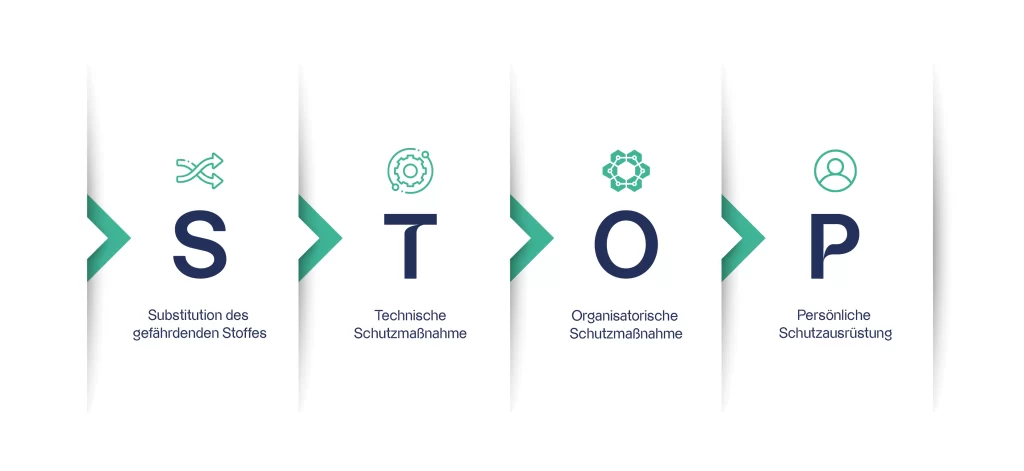
Filter systems in pharmaceutical production
Filter systems, which are used for the dedusting of tablet presses or capsule fillers, absorb the processed substances and collect them in waste containers. These must be safely and securely separated from the appliance and disposed of. As these filter systems are generally not specifically connected to a single production machine, but are used as so-called collective dedusters, it is necessary to deal with a large number of different substances consisting of auxiliary and active substances. Therefore, as part of a risk assessment of the existing exhaust air devices and processes, it must be determined which substances arrive in the filter system.
Accordingly, a protection concept should be designed that is specified for the most critical substance. This protection concept covers the operation of the filter system itself, but also maintenance activities such as filter and discharge changes. Large quantities of dust are to be expected during such activities in particular, which requires appropriate protective measures to avoid coming into contact with the substance mixtures. It is not advisable to assume concentrations of active substances in the mixture and their dilution as in the manufacturing processes, as mixing of the substances in the extraction processes is generally not homogeneous and is not controlled in this context.
Challenges and solutions
With the increasing development of active substances that are effective even in the smallest quantities, the Occupational Exposure Limit (OEL) values are falling continuously. This requires continuous adaptation and improvement of protective measures. New technologies and protection systems generally meet these increasing requirements. However, existing plants and manufacturing processes often face challenges when it comes to meeting the increased requirements of containment levels.
Pharmaceutical plant operators are therefore faced with the choice of upgrading or retrofitting existing systems or implementing new solutions that correspond to the current state of the art. This challenge extends not only to the direct production areas, but also to peripheral processes such as ventilation concepts, dust extraction, material transportation and cleaning.
Conclusion: Containment in the pharmaceutical industry
The development and implementation of an effective containment strategy is essential for pharmaceutical manufacturing processes. The STOP principle provides clear guidance for prioritizing protective measures. Pharmaceutical plant operators must continually evaluate new technologies and solutions to meet ever-changing requirements and ensure the safety of their employees.