Wherever dust is generated in the course of the production process, measures must be taken to protect people and the environment by minimizing – if not eliminating – exposure to dust.
In accordance with the STOP principle for reducing dust pollution or the procedure for dealing with the occurrence of substances hazardous to health, technical solutions are an important approach when it comes to protecting everyone involved – after the substitution of the relevant substances. One technical solution is the use of filtering equipment, also called dust collectors or dust collectors.
In this article, we will show you the requirements for filter systems and what is important when selecting them so that the best possible protection can be achieved.
Areas of application and mode of operation of dust collectors
Filter systems are used where the dusts and substances produced can be extracted due to their properties. Depending on the process and the overall concept of the production plant, this can be at different points.
They can be used directly at the process step where the dust is generated (e.g. tablet press) or a central extraction system with appropriate filtration is installed, which is connected to several so-called extraction points via a pipe system.
When designing a filtration system, the system should be selected accordingly, whose individual mode of operation fits the required conditions.
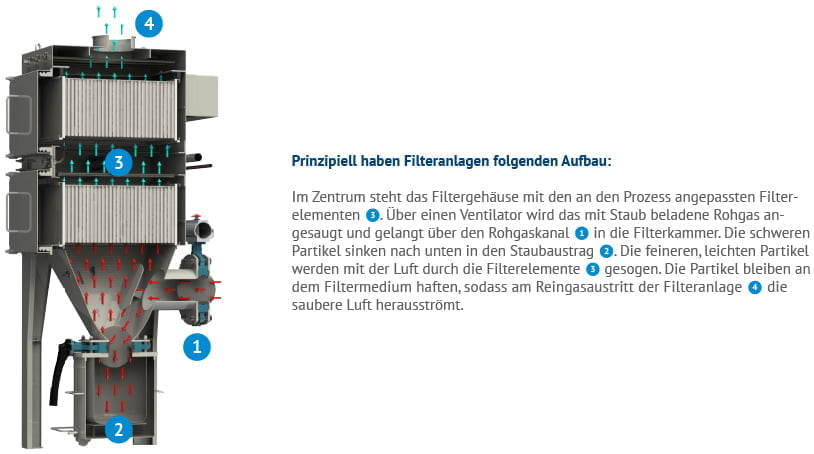
Dust collector requirements
In general, there are other aspects to consider in addition to the overall concept when selecting and designing filter systems. In principle, the more detailed the information is that the engineer in charge of the design receives, the better the protection that the filter system finally provides.
Below we give you an overview of the most important requirements. Please note, however, that this list cannot replace a conversation with the contracted company and a detailed consultation!
Requirements due to the material properties of the dust
Many places in industry produce dusts that differ in property and hazard. For this reason, the type of dust and its hazard potential must be taken into account when selecting the right dust collection system.
Influence of dust on operating personnel and production
The first step is to check what the exposure limits are and what needs to be considered with regard to cross-contamination. The so-called Occupational Exposure Limit (OEL) is used for exposure classification. This classification then results in the assignment of the filter system to the OEB stages and thus the selection of the necessary containment measures.
Depending on the effectiveness of the substances, the filter system itself initially serves as a containment measure. For protection during operation and maintenance, however, additional containment concepts are also used for the filter system itself.
These include:
- WIP (Wash-In-Place) for cleaning the filter system from the inside
- Safe-Change for contamination-free replacement of filter elements (in
combination with the corresponding closure systems) - Selection of dust discharge: Is a simple container sufficient or are other containment measures, such as Safe-Change or RABS for safe change of dust discharge with additional barrier (Restricted Access Barrier System) necessary?
The physical and chemical properties of the dust
The consideration of the material properties of the dust is important for the design of the filter system, the selection of the filter elements as well as the selection of the materials to be used and their resistance.
Requirements from the process
Depending on the industry, different requirements arise from the processes: If a filter system is used in the pharmaceutical industry, a great deal of attention is paid to containment. When used in the chemical industry, high volume flows are the decisive factor.
We have briefly summarized and explained the basic requirements for you below:
Dust content of the raw gas or required purity value of the clean gas
The amount of dust contained in the air to be cleaned affects the choice of filter. For example, cartridge filters are used for larger loads, or HEPA filters are used for lower loads or higher air purity requirements. Combinations are also often used: A pre-filter is then used as the first filter stage, while a second filter stage takes over the task of filtering the fine, often health-endangering substances from the air.
Volume flow
The volume flow determines the type of filter element as well as the number of filter chambers. Since the efficiency of the filter element depends on the flow rate passing through it, it is limited depending on the filter medium. In the case of a higher volume flow, it is then necessary to divide the filter into several filter elements and thus into several filter chambers.
The volume flow is also an important variable for the design of the blower or fan and the connecting piping.
Temperature of the raw gas
The expected temperature of the air flowing through has an influence on the materials to be used: At higher temperatures, the components of the filter element and all other installed assemblies must be designed in such a way that no undesirable effects occur. It may also be necessary to insulate the filter chamber to protect the operating personnel from burns, as heating of the housing may occur.
Sound pressure level
There are specifications regarding the sound pressure level that every operator must comply with. In the case of filtration systems, the source of the noise is the fan. Depending on the fan design and the required sound pressure level, a sound-insulated housing, vibration dampers or even a silencer must be provided for the fan.
Explosion protection
Potentially explosive atmospheres can occur in some processes. The division into the corresponding zones is specified by the operator. Appropriately tested and approved concepts are available for filter systems, which ensure that the overall system will not suffer any further damage if an explosion should occur within the filter systems.
Requirements by the operator
In addition to the process-related requirements, however, there are also conditions that result from the overall concept of the production plant. Among others, the following points can be mentioned:
Control system
The filter system can be controlled independently or via integration into a higher-level control system for the entire system. Which control system is used depends on the required planned signal exchange. The scope here is often customer request.
Housing material
The housing material is selected based on how the filter system is to be integrated into the overall concept. Often the decision also results from the applied process. However, aspects such as existing solvents or GMP (Good Manufacturing Practice in the pharmaceutical industry) requirements also play a role in making the right choice.
Fan
With the fan, the question arises as to whether there is a central extraction system or whether the filter system is operated directly at the extraction point. This determines, on the one hand, the size of the fan and, on the other hand, whether the filter unit is supplied with or without a fan. Care must always be taken to ensure that the power of the fan is in proportion to the volume flow. The correct design of the piping system must also not be neglected.
Performance measurement and monitoring options
To check whether the filter system is working properly and delivering the performance for which it is intended, the performance – i.e. separation capacity, tightness, etc. – can be determined. If such tests are envisaged, the filter system can be equipped with the appropriate measuring equipment, such as DEHS lances, at the time of delivery. In general, there are several ways to monitor. In order to use the most appropriate and optimal equipment for one’s own process, this should be discussed with the engineer in advance.
Conclusion
In addition to the area of application, which determines the type of filter system used, there are many other requirements for dust collectors that can be grouped into the following categories:
- Requirements due to the material properties of the dust
- Requirements from the process
- Requirements by the operator
In each of these categories, there are a variety of requirements that must be considered for optimal use of the dust collector. Depending on the application, different decisions are made about components such as the fan, control system, temperature resistance or housing material.
Our tip: A discussion with the manufacturer will show which options are suitable for your processes and requirements in order to achieve a perfect result:
Clean air and protection from hazardous substances for people and the environment!