Various processes and production steps are used in the pharmaceutical industry and other branches of industry, all of which have one thing in common: They generate emissions that are subsequently present in the environment and the air we breathe.
Depending on their composition, these emissions can either be merely annoying because they are deposited on surfaces (which then have to be cleaned) or even dangerous for employees, as they can be inhaled while suspended in the air we breathe and cause illness.
In this article, you will learn how emissions are created. In this context, dusts are considered in concrete terms: What properties do they have? What effect do they have? What can be done to limit the spread of dusts?
Emergence of emissions
The generation of emissions is as diverse as the various production processes themselves. The following distinction exists:
- Spatial emissions (arise, for example, from spraying
- areal emissions (arise e.g. from immersion baths)
- Point emissions (generated e.g. during grinding)
In the pharmaceutical industry, for example, tablet pressing is a process that results in the release of dusts. But emissions are also generated during mixing, coating and other processes.
The dispersion depends on the following properties of the substances:
- Particle size
- Particle weight
- Momentum of the particles
- Particle velocity
- State of aggregation (solid, liquid, gaseous)
If the substance is present as a gas, dispersion occurs uniformly because the gas molecules float (disperse) in the air. In the case of liquid or solid aggregate states – e.g. dusts – the dispersion, i.e. the distribution of the particles in the air, depends on the droplet or particle size: the smaller the size, the more easily the particles float in the air and can be carried further.
Dust properties
The emissions that are in solid form are called dust. This term includes all fine, solid particles that occur in various sizes in gases and especially air. The particles can be of various origins. The dwell time can also vary – depending on the size.
So dust is not just dust!
Depending on how and where the dust originates, it results in certain properties with corresponding effects on humans and the environment. If these properties are harmful, solutions must be found to eliminate dust.
When processing dusts – or the occurrence of dust in general – it must be noted that, depending on the composition and occurrence, a hazard may arise for employees. With regard to occupational health and safety, limit values are defined depending on particle size and particle shape, and compliance with these values is checked by measuring the concentration in the air.
Differentiation according to particle size and shape:
- E-dust
This dust can be inhaled through the mouth and nose. The particles with a size of up to 100 µm stick to the nasal hairs or mucous membranes.
Example: pollen or cement dust - A-dust
A-dust is fine dust that can penetrate into the alveoli (respirable), as the particles are only max. 5 µm in size. 5 µm in size.
Example: welding fumes - U-dust
U-dust stands for “ultrafine dust”. These are nanoparticles with a size of <100 nm.
Example: Product of combustion processes, in paints and coatings - Fibers/fiber dusts
Fibers are elongated particles of inorganic or organic substances. All fibers that are >5 µm long, have a diameter of <3 µm and exceed a length:diameter ratio of 3:1 represent a hazard as they can penetrate into the deeper respiratory tract.
Example: asbestos, glass wool, cotton dust
Differentiation according to physical properties
If dusts are not only generated in production, but are also used to manufacture a product, the following properties must be considered:
- Sticky dusts
With sticky dusts, the particles stick to each other and to surfaces. This can lead to bridging in the production systems.
Example: Coating tablets - abrasive dusts
The particles of abrasive dusts can damage production systems in the long term due to their strength and surface properties. Therefore, the flow velocities as well as the wall thicknesses must be taken into account when designing the pipelines. - hygroscopic dusts
These particles draw moisture out of the air and stick together or liquefy. They are then no longer dry and free-flowing, which can affect further production steps. - hydrophobic dusts
Hydrophobic dusts do not bind with moisture in the air. - agglomerating dusts
By spraying fine particles, small grains are created by sticking together, which improves the transport properties and processing of the materials. Agglomeration makes the grains more free-flowing than the fine particles, making them easier to transport. However, the flow velocities must be taken into account when designing the pipelines and production plants, as plugging can occur in the production plants. - free-flowing dusts
The finer the particles, the less free-flowing the dust and the easier the material can be whirled up. The flowability must be taken into account in the design of the production equipment. - bridging dusts
Bridging must be avoided in production plants, as it can lead to disruptions in the process. When designing production facilities, bridge-forming dusts must be taken into account and the design adapted accordingly.
Dust effect
The effect of dust depends on various factors. For example, dust can be a nuisance simply because of the amount present. The human body, especially the respiratory tract, is equipped with various protective systems to counteract the dust, as long as the amount is kept within limits. However, the effect also depends on the properties mentioned so far – e.g. how far the particles can penetrate the organism.
To determine the hazard potential, the composition is important in addition to the particle size. Depending on the ingredients, even larger particles that only reach the upper respiratory tract can pose a danger. Therefore, the toxicological properties must be considered:
- Sensitizing dusts
These dusts can trigger allergies and therefore pose a risk to humans.
Example: organic dusts from plants and animals - Fibrogenic dusts
Fibrogenic dusts can lead to scarring of the lung tissue and permanently impair lung function.
Example: quartz dust - Corrosive dusts
The particles of corrosive dusts can destroy human tissue by forming acids or bases.
Example: Bird droppings - Toxic dusts
Inhaling toxic dusts can damage internal organs such as the lungs.
Example: toxic dusts of lead, cadmium - Carcinogenic dusts
These dusts can cause cancer.
Example: oak wood dust, asbestos - Radioactive dusts
Radioactive dusts can attack the genome, trigger tumors and settle in mucous membranes or bronchial tubes.
Example: Tritium
Dust containment
To reduce the spread of dust or the risk from dust, the STOP principle comes into play, which we have already looked at in our blog article on employee protection:
- Substitution ofthe risky substance – check if there are substances that are less toxicological.
- Technicalmeasures – upgrading facilities with appropriate security solutions.
- OrganizationalMeasures – Plan to ensure that employees are not exposed to hazardous materials for too long.
- PersonalProtective Equipment – Use when all other measures are not applicable.
So the first thing to do is to try to prevent the occurrence of dust. This can be done by selecting the material properties – for example, less dust occurs when agglomerating substances are used than when fine substances are used.
If dust nevertheless occurs, the danger can be reduced if less toxic substances are used.
Technical measures are solutions that absorb dust created. These include encapsulation of the dusting process steps, water spraying systems or fans.
An efficient way to protect people and the environment is to extract the dust. In this process, the air laden with dust is sucked up directly and cleaned in dust collectors with filter elements adapted for the application. The dust remains in the filter system and can be disposed of accordingly.
Depending on the particle size and properties, there are various options to choose from, which is exemplified in the following overview. Therefore, when designing a filtration system, it is important to communicate the characteristics of the dust to the equipment manufacturer so that the correct filter can be selected.
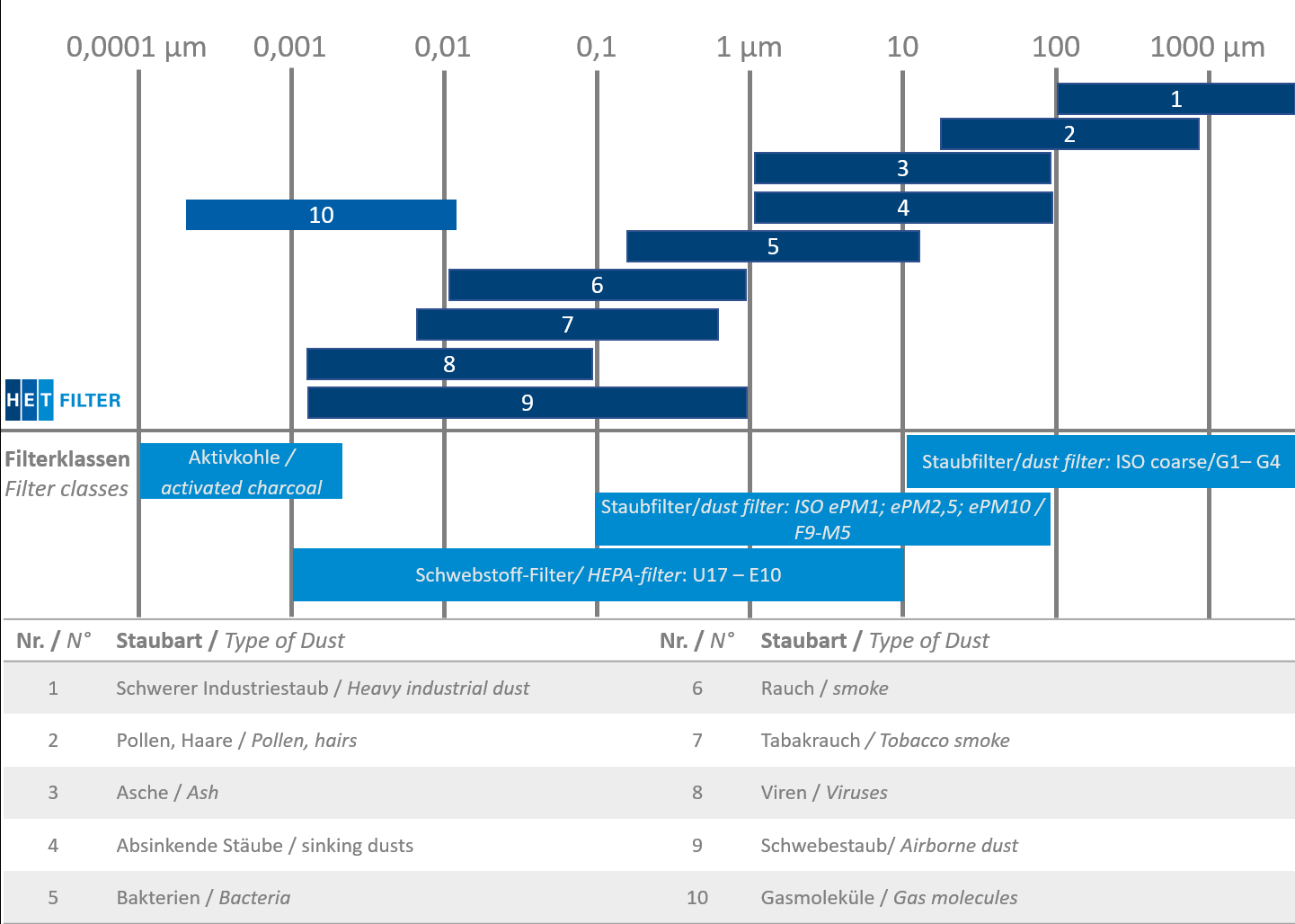
In addition to planning the deployment of employees, organizational measures also include regular cleaning and ventilation of the affected production areas in order to keep exposure at the workplace itself to a minimum.
If the occurrence of dust cannot be prevented despite all efforts and the risk to employees remains high, the use of personal protective equipment still remains. Here, too, the selection depends on the properties of the dust that occurs.
Summary
Dust is an everyday companion that cannot be completely avoided. But whether it is just a nuisance or a health hazard depends on a number of factors:
- Quantity
- Particle size and shape
- material properties
- toxicological properties
In addition to regular cleaning, there are various technical options such as filter systems to protect people and the environment and reduce the negative impact of dust on the production of sensitive parts.