Dust collectors and filter systems are used in the pharmaceutical and chemical industries to bind the dust generated during production. In the filter cells installed in it, the particles are separated from the air, so that in the end clean air is created and the danger from the dust is eliminated.
The type of dust or the composition of the air mixture as well as the requirements from the process result in the selection criteria for the filter cells.
Filter cells are available in various types, designs and materials. The following article is intended to give a brief overview of the construction methods and classifications of filters.
In order to be able to compare the individual filter cells in their various designs with each other or to compare them with the requirements from the process, there is a classification system that is defined on the basis of standards.
The correct selection and maintenance of filtration systems and their components is crucial to ensure air quality, guarantee the safety and efficiency of the production process and ensure compliance with environmental and health regulations. The following article provides a detailed overview of the different designs, filter groups and classifications of filters to assist industry professionals in selecting the best filtration solution for their specific needs.
Classification of the filter cells
In order to be able to correctly assign the various filter classes or filter groups, an overview of the air filters considered should first follow in order to show when which classification applies.
Air filter overview
Air filters are classified according to their ability to separate particles of different sizes.
There are “dust filters” that are used for high dust loads and coarser particles in the air. These are further subdivided into “coarse dust filters” and “fine dust filters” – depending on the particle size. For these filters, classification is based on the EN ISO 16890 standard.
If finer or finest particles are to be filtered, “HEPA filters” are used. Here, a further subdivision is made into “standard HEPA filters” and “high-efficiency HEPA filters”. Here, too, the classification is based on the actual particle size. Classification is based on the EN 1822-1 standard.
Classification according to EN ISO 16890
The basis of the classification is the filtration efficiency of the filter cell. This indicates how many particles are retained by the filter medium and how many particles can still be found in the exhaust air after passing through the filter. The value that is of importance here is the separation efficiency of particles with sizes from 0.3 µm to 10 µm.
Based on this value, the corresponding filter group can be assigned in accordance with the EN ISO 16890 standard.
The standard provides for 3 levels according to which the filter cells are classified:
- PM1: Separation efficiency for particles up to 1 µm (0.3-1 µm)
- PM2.5: Separation efficiency for particles up to 2.5 µm (0.3-2.5 µm)
- PM10: Separation efficiency for particles up to 10 µm (0.3-10 µm)
If at least 50% of the specified particles are separated, the filter cell has reached the corresponding group. In this case, one speaks of the “minimum efficiency”, which is determined on a new filter cell. In parallel, the “average efficiency” is also measured over the entire filter cell.
Thus, in the procedure for determining the filter group, the minimum efficiencies for the 3 particle sizes are first determined together with the average efficiencies. At the step where at least 50% of the deposition is achieved, the average efficiencies are taken and rounded down to the nearest 5 step. These values can then be used to specify the classification
.
Example: ISO ePM2.5 80%
If it happens that a filter cell fulfills the conditions for several stages, it is up to the manufacturer of the filter cells to decide which indication he makes on the product.
Classification according to EN 1822-1
The DIN EN 1822-1 standard refers to the classification of high-performance particulate and high-performance HEPA filters used in cleanroom technology or the pharmaceutical industry. In addition to the classification of the filter cells, the production and testing are also specified in the standard. It should be noted here that Part 1 of the DIN EN 1822 standard is valid for the classification of filters – the specifications for production and testing, however, can be found in Parts 2-5 of ISO 29463.
The DIN EN 1822-1 standard distinguishes between filter groups and filter classes:
Filtergruppe | Filterklasse | Integralwert Abscheidegrad im MPPS | Integralwert Durchlassgrad im MPPS | Lokalwert Abscheidegrad im MPPS | Lokalwert Durchlassgrad im MPPS |
---|---|---|---|---|---|
EPA = Hochleistungs- Partikelfilter | E10 E11 E12 | ≥ 85 % ≥ 95 % ≥ 99,5 % | ≤ 15 % ≤5% ≤ 0,5 % | - - - | - - - |
HEPA = Schwebstofffilter | H13 H14 | ≥ 99,95 % ≥ 99,995 % | ≤ 0,05 % ≤ 0,005 % | ≥ 99,75 % ≥ 99,975 % | ≤ 0,25 % ≤ 0,025 % |
ULPA = Hochleistungs- Schwebstofffilter | U15 U16 U17 | ≥ 99,999 5 % ≥ 99,999 95 % ≥ 99,999 995 % | ≤ 0,000 5 % ≤ 0,000 05 % ≤ 0,000 005 % | ≥ 99,997 5 % ≥ 99,999 75 % ≥ 99,9999 9 % | ≤ 0,002 5 % ≤ 0,000 25 % ≤ 0,000 1 % |
The basis of the classification here is the minimum filtration efficiency of the filter cell for particles of size 0.1 – 0.3 µm, the “MPPS”, as explained in the paper Filter Influence Factor Principle.
Classification proceeds in three steps: first, the particle size at the separation minimum is determined on the unfolded filter medium (MPPS). In the second step, the absence of leaks (= local separation efficiency) is tested. Finally, the integral filtration efficiency of the filter element is determined using a test aerosol for the particle size in the separation minimum.
Based on the values obtained, the filter element can be assigned to the appropriate filter class with the help of the overview in the standard.
The following figure shows in which areas the different filter classes or filter groups can be used.
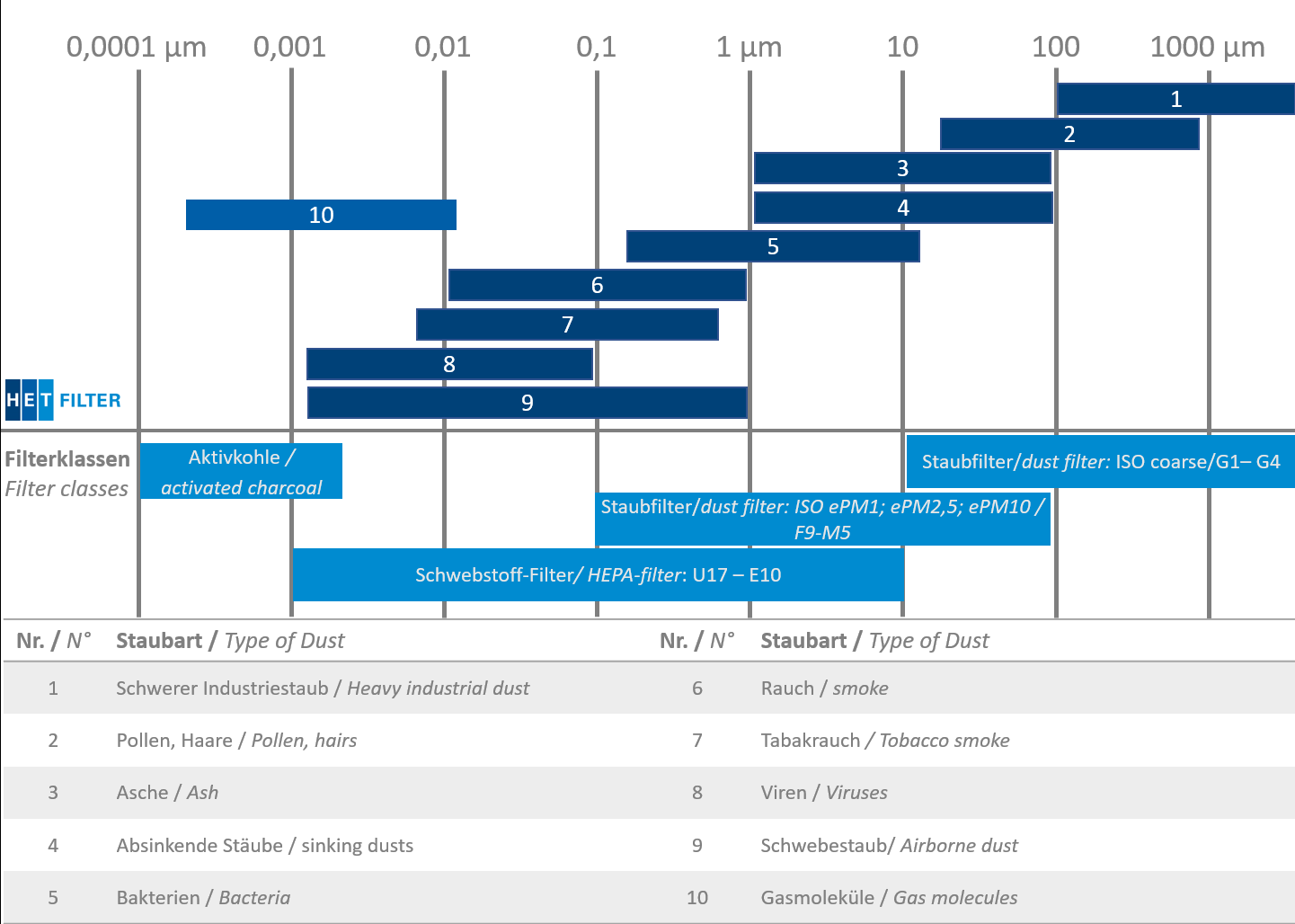
Filter cell construction methods
Various designs are available for filter elements, depending on the manufacturer, application and requirements.
Various factors play a role in the selection: from process requirements to the installation situation, resulting from the design of the filter system, to the question of cost, there is a lot to consider.
In this article, we will take a look at the “cartridge filter”, “lamella filter” and “cassette filter” designs – i.e. the filters that are used in the plants of HET Filter GmbH.
The three filter designs have different characteristics, which are described below:
Cartridge filter
Structure:
In the cartridge filter, the pleated filter medium (filter fleece) is located inside a cylindrical carrier basket. This design allows for cost-effective production.
Use:
for air with high dust loads
Classification:
Coarse and fine filter according to EN ISO 16890
Special features:
Due to its design, the filter cannot be changed under safe-change conditions, i.e. only low containment requirements can be met with this filter. These are described in the blog articles on the subject of “Containment”.
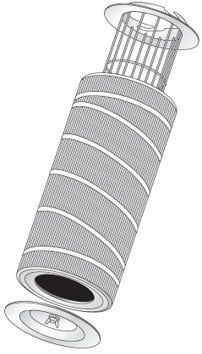
Lamellar filter
Structure:
Lamella filters consist of a
pleated fleece that can be installed either horizontally
or vertically.
The
respective filter stage of a dust extractor consists
of several of these lamella filters
.
Due to the design, the
individual lamella filters can be cleaned using pulsed
compressed air.
The compressed air
causes the elements to vibrate, so
that the particles are loosened and fall into the
dust discharge.
Due to the simple
design, this type of filter is comparatively
inexpensive.
Use:
for air with high dust loads,
for difficult dusts
Classification:
Coarse and fine filter according to EN ISO 16890
Special features:
Due to its design, the filter cannot be changed under safe-change conditions, i.e. only low containment requirements can be met with this filter. These are described in the blog articles on the subject of “Containment”.
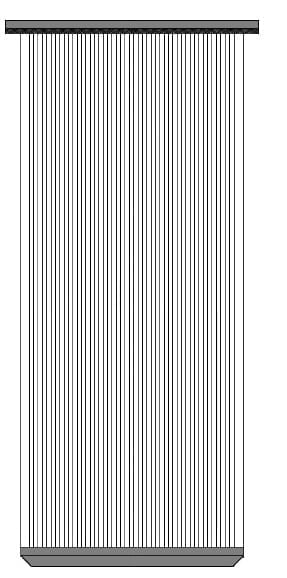
Cassette filter
Structure:
In the cassette filter, the
medium is contained in a robust, conductive
housing made of galvanized steel or
stainless steel.
For use in non-
potentially explosive areas, the
frame can also be made of wood (MDF).
The filter fleece is folded in layers or in a V-shape
and sealed to the
housing using a casting compound.
There are spacers between the individual
layers, which
ensure that the layers remain open during the
intake of air and that the
air can flow unhindered through the filter
.
They are also conductive to prevent
electrostatic charges.
Application:
for the finest dusts in the pharmaceutical industry,
Dust loads up to 2,000 mg/m3
Volume flows up to 2,000 m3/h
Can be used in
various systems thanks to the standardized dimensions.
Classification:
HEPA filter according to EN 1822;
dust filter according to EN ISO 16890
Special features:
The filter can be changed under safe
change conditions, i.e.
this filter can be used to meet containment
requirements up to OEB6, among others
.
The filter cells can be cleaned, which
increases the service life.
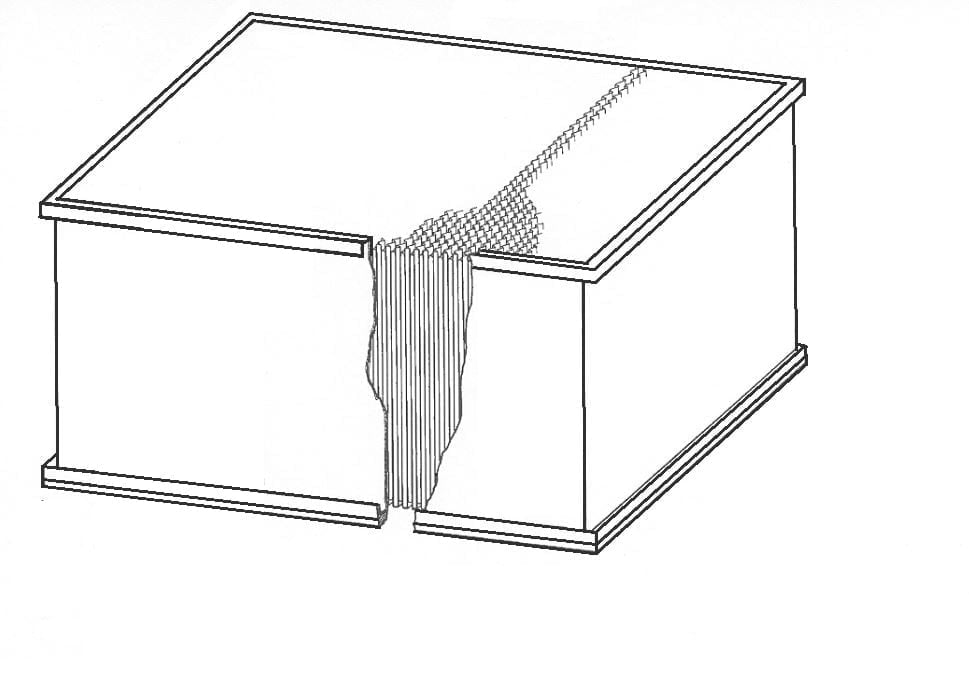
Conclusion
Filter cells are available in a wide range of features and design options. The selection depends on the properties of the dust as well as the requirements of the process. It is therefore essential for the design of the filter systems to know the dust precisely and to transmit the data to the manufacturers of the filter groups. Only in this way can the right filter elements be selected, so that in the end their task is fulfilled – providing clean air, without danger to people and the environment.