Digitalization has long since arrived in production-related areas of the pharmaceutical industry – with a clear goal: greater efficiency, safety and traceability while complying with regulatory standards. While topics such as automation, networking and data analysis are already established in production, quality assurance and logistics, one area is often neglected: filtration technology.
Filtration is a key component for safe and GMP-compliant production processes – especially where potentially hazardous or highly active substances are processed. Intelligent filter systems with digital control and monitoring offer enormous potential here. They make it possible to record filter statuses in real time, optimize maintenance processes and minimize failure risks.
In this article, we show how digital filtration technology works today, what advantages it offers and how companies in the pharmaceutical industry can benefit from its introduction.
Filtration technology in the pharmaceutical industry – status quo
Filter systems in pharmaceutical production environments perform a variety of tasks. They protect employees from harmful dusts, prevent cross-contamination and ensure product quality. In cleanrooms, highly efficient particle filters (HEPA) are standard – as are dedusting systems that extract process dusts directly at the source.
However, traditional filter systems are often “self-contained”. Many of them have no or only limited digital connection. The need for maintenance often has to be determined manually – for example by measuring pressure loss or visual inspection. Filters are changed at fixed intervals, not on the basis of their actual condition. The result: unnecessary downtime, limited efficiency and limited transparency.
In addition, conventional systems are rarely integrated into the higher-level production control system (MES/SCADA). Information about operating statuses, alarms or energy consumption is only available to a limited extent – or not at all.
Digital filtration technology as a game changer
Digital filtration technology is fundamentally changing this situation. It stands for the consistent integration of modern control technology, intelligent sensor technology and networked data analysis in extraction systems and filter modules. This makes filtration an active part of the digital value chain.
Real-time monitoring with IoT technology
Equipped with sensors – for example for differential pressure, volume flow, temperature or humidity – filter systems can be continuously monitored. The data flows into a central control system or cloud-based platform and enables detailed analysis in real time.
Predictive maintenance
Instead of replacing filters at fixed intervals, digital filtration technology enables condition monitoring. The systems automatically detect when a filter is saturated and issue corresponding messages. Maintenance measures can be better planned – unplanned downtimes are avoided.
Integration into production control systems
Modern systems are fully capable of communication – for example via OPC UA, Modbus or Profinet. This allows them to be integrated directly into the existing infrastructure and enables holistic control and monitoring of production.
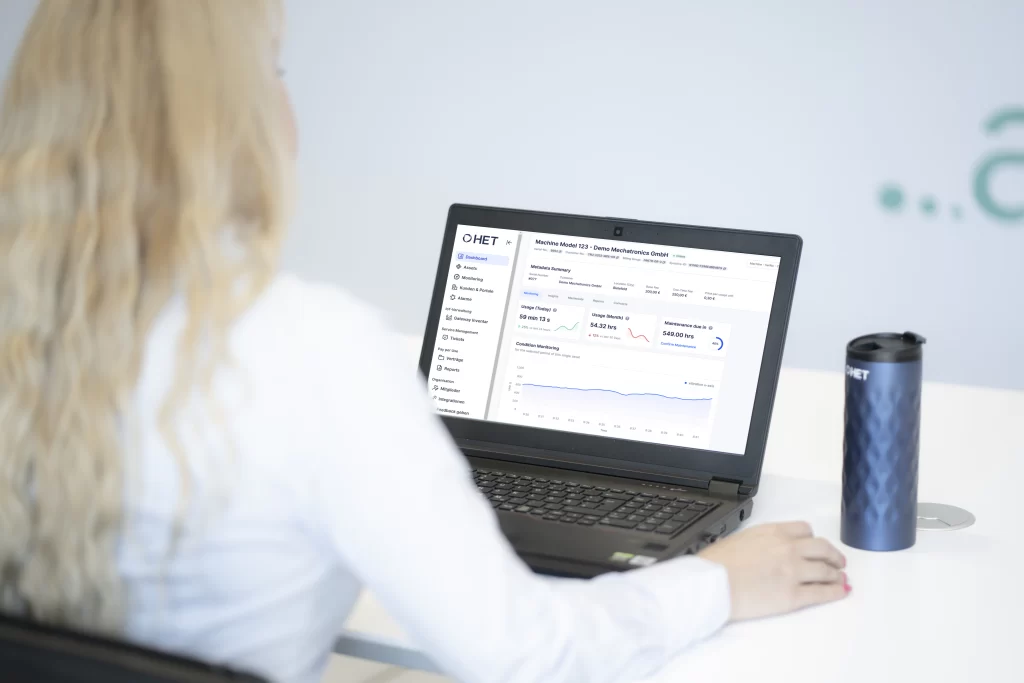
Advantages of digital filtration technology
The switch to digital filtration technology has a number of specific advantages:
More efficiency in maintenance
Automated status messages reduce maintenance costs and minimize unplanned downtime. Filters are only changed when they are actually needed, which reduces material costs and downtimes.
Greater process reliability
By permanently monitoring the operating parameters, deviations can be detected at an early stage and countermeasures initiated – before production-related problems occur.
Better traceability
All operating data is documented and can be used for quality assurance and audits. This traceability is a decisive factor, particularly in the GMP environment.
Optimized energy use
Monitoring and control of the volume flow ensure that the extraction power is used as required – which can significantly reduce energy consumption.
Application examples from practice
Digital filtration technology is used in numerous pharmaceutical processes:
- Active ingredient production: Extraction systems with digital control ensure dust collection during powder handling, weighing processes or when opening containers.
- Tableting: Monitoring the filter service life ensures consistent extraction performance – important for consistent tablet quality.
- Packaging: Integration into the packaging line enables direct adaptation to the line speed.
- Clean room zones: Digital filter modules can be adapted to changing production conditions and report faults at an early stage.
How to successfully switch to digital systems
The introduction of digital filtration technology requires a systematic approach:
- Inventory: Which systems are in place? Which processes should be digitized?
- System selection: What are the requirements with regard to ATEX, GMP, filter class, control interfaces?
- Integration: Planning the integration into existing control systems.
- Commissioning & training: Professional installation and instruction of personnel.
- Validation: Documentation and proof of GMP conformity.
HET Filter offers comprehensive support here – from planning and design to integration and qualification.
Future prospects: AI, sustainability and networking
The future of digital filtration technology lies in the connection with artificial intelligence (AI) and higher-level management systems. The aim is a fully networked production process in which filtration not only reacts, but also acts proactively.
Conceivable in the future:
- AI-based control algorithms that determine the optimum time for filter changes
- Energy management systems that optimize power consumption
- Life cycle analyses that provide information on sustainability and carbon footprint based on real operating data
Digital filtration technology is more than just a trend – it is a strategic lever for greater efficiency, safety and transparency in pharmaceutical production. Companies that rely on intelligent filter systems at an early stage not only gain a technological advantage, but also meet key requirements in terms of compliance, sustainability and cost-effectiveness.
Do you want to make your filter systems fit for the future? Our experts support you in the planning, implementation and validation of digital filtration technology – customized, GMP-compliant and future-proof.