In the production of the pharmaceutical and chemical industry dusts occur again and again. Since this is undesirable, measures must be taken to prevent the occurrence of these dusts. One possibility is the use of filter systems, so-called dust collectors. In these plants the dust is separated from the air and collected.
For this purpose, the filter units are equipped with filter elements, in whose filter media or filter mats the dust is caught and prevented from being transported further with the air. There are different designs of filters as well as different materials that filters can be made of.
The following explains how the principle of filtration works in order to understand what is important in the selection of materials.
Criteria that influence the selection of the filter
The selection of the number, type and materials of the filter elements – also called filter cells – depends on the nature of the substance to be filtered as well as the conditions under which filtration takes place. The following conditions must be observed:
- Volume flow [m3/h]:
The volume flow describes the amount of air that is to be filtered per hour. Since the filter element is limited here by its design, the number of filter elements must be increased as the volume flow increases.
- Composition of the medium:
The applications often involve air that is loaded with particles. However, other gases and dusts may also be contained in the medium. The composition of the medium flowing through the filter determines the selection of the filter’s materials, as the substances must be compatible with each other and must not react in order to exclude further hazards.
- Air temperature [°C]:
The temperature of the air flowing through the filter cells – as well as its composition – determines the filter materials. At higher temperatures, correspondingly heat-resistant material must be used to prevent premature wear or even destruction of the filter cell.
- Dust load of the air [mg/m3]:
The dust load indicates how much dust or how many particles are in the air to be filtered. This quantity determines the type of filter. A filter element only has a certain service life, i.e. absorption capacity of the dust until it is clogged. The more particles there are in the air, the faster the filter becomes clogged and its operating limit is reached. Depending on the type of filter, the filter can either be cleaned and is thus ready for use again or – if this is not possible – it must be replaced.
- Requirements from the process:
The following questions arise from the process:
– What should be done with the separated material?
– Should it simply be separated or should it be reused?
– How should the filter system be operated? Are downtimes possible due to service activities in the
process or must the filter system be operated continuously?
– Are there any regulations that must be observed due to the applications, e.g. ATEX?
– Are there any requirements regarding containment?
The answers are important for the selection of filter elements, because they determine the ability to clean and the number of filters or the type of design.
- If substances are to be recycled, the filter cell must be cleanable. If it is not, the substance remains in the filter medium and is disposed of together with the filter cell.
- If the filtration system is to be used continuously, additional filters must be planned so that the volume flow can be distributed accordingly during cleaning (during cleaning, filtration is not possible at the filter, which is why the volume flow is distributed to the other filters).
- If an explosive atmosphere is present and there is a risk of explosions, the filter cell and its components must be grounded to prevent electrostatic effects.
- If there are requirements regarding air purity, the filter groups must be observed according to the filter classes
Design and mode of operation of a filter cell
To better understand the influence of these criteria, the operating principle of the filter elements must be known.
The dust, or the various particles it contains, have different properties that are crucial for the efficiency of the filtration.
In addition to these properties of the dust itself – sticky dust, for example, causes the filter medium to clog more quickly, while free-flowing dust is very easy to filter – the properties of the individual particle and the filter cell must also be considered.
Structure of the filter cell
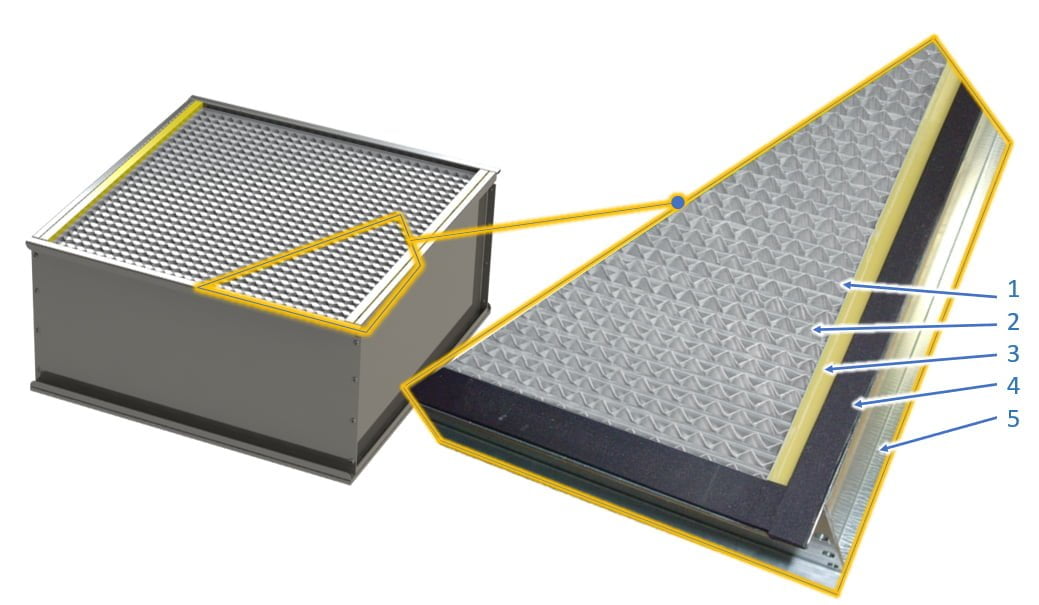
- Filter medium
- Spacer
- Potting compound
- Seal
- Metal frame
Effects of filtration
In order to explain the principle of filtration – i.e. the mechanical separation of substances from gases – it is necessary to look from the filter cell as a whole to the filter fiber in particular: here, physical effects are at work on a small scale that are important for the result on a large scale.
The particles that flow through the filter cell follow the air flow. The size and nature of these particles determine what happens inside the filter cell – on the filter fibers.
Inertia effect:
A particle with a large mass is relatively inert. If the air flows past the filter fiber, this particle cannot follow, hits the fiber and sticks.
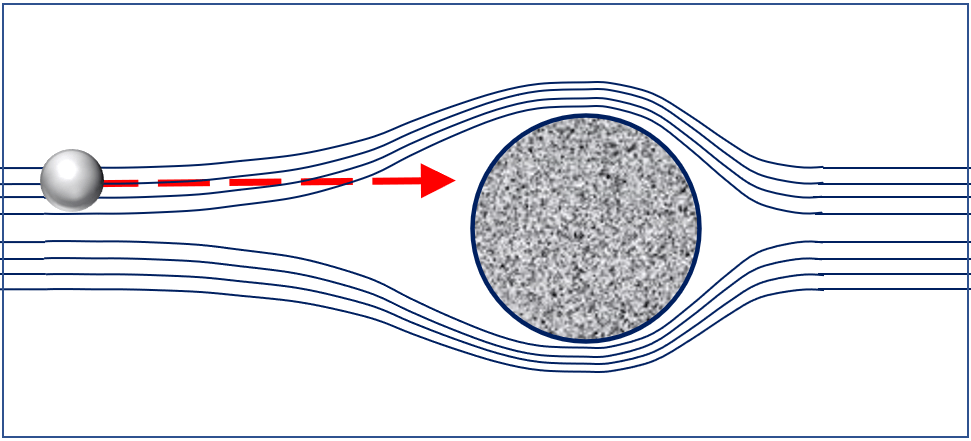
Diffusion
A particle of very small size flows with the air stream, but does not follow the streamlines, but deviates from them. During these movements, it can hit a fiber or other particles and stick there. The cause of this diffuse behavior lies in Brownian molecular motions.
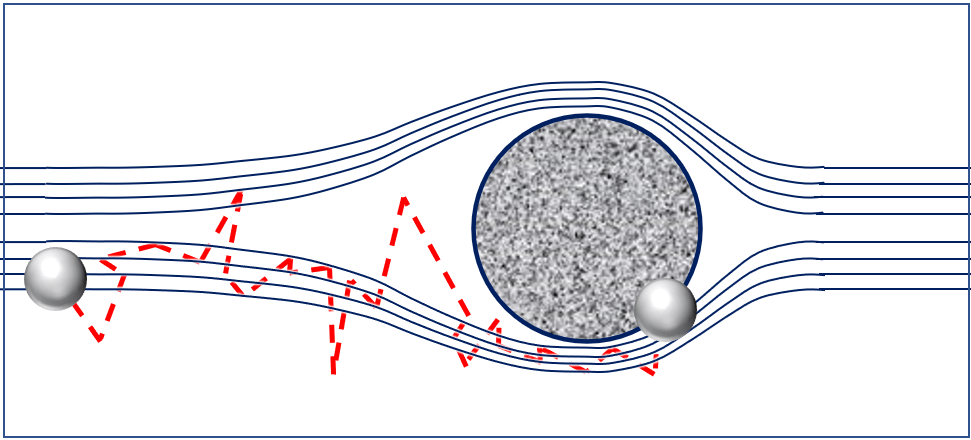
Blocking effect:
Although a largeparticle follows the air flow on the streamlines, it is too large to avoid the filter fibers. When flowing around it, it hits the filter fiber due to its dimensions and sticks there.
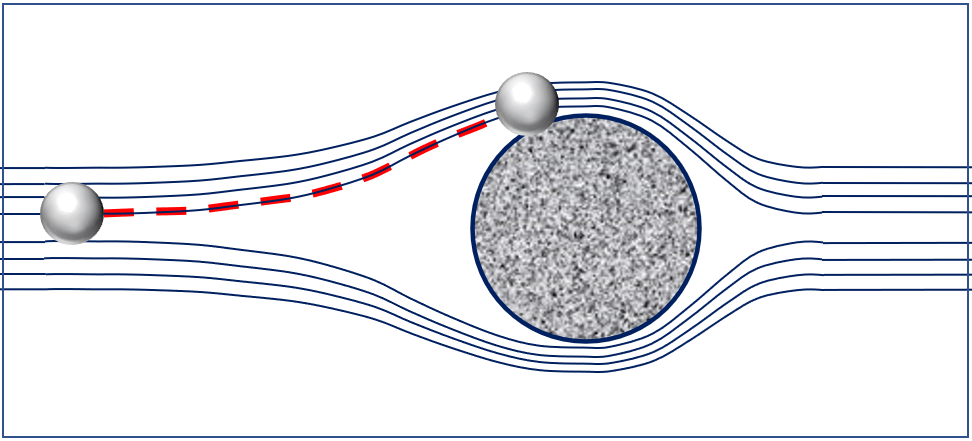
Electrostatic attraction
(Van der Waals forces):
The movement and associated friction of the particles can cause them and the filter fiber to become electrostatically charged. If the charge is opposite in each case, the particle is attracted to the filter fiber and remains stuck there.

These effects ensure that the particles from the air are retained in the medium of the filter cell. How well this works is indicated by the efficiency, also called separation efficiency. This indicates how many particles remain in the filter cell or how many particles are still in the exhaust air after flowing through the filter cell. The separation efficiency is given as a percentage (number of separated particles in relation to the incoming particles).
The influence of the various effects on the degree of separation is shown in the following diagram:
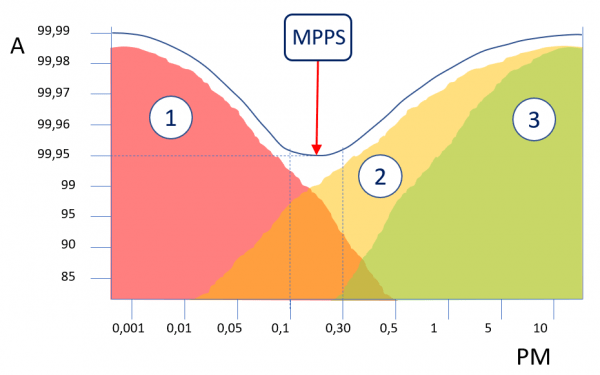
- Diffusion A Separation efficiency [%]
- Barrier effect PM Particle size [µm]
- Inertia effect MPPS particles 0.1-0.3 µm -> minimum of filtration
Since particles of various sizes and properties are present in the air, the effects mentioned act in correspondingly different ways. Smallest particles are separated due to diffusion. Larger particles remain in the filter medium due to the inertia effect or the barrier effect. In between, there is overlapping of the effects that influence the filtration efficiency of the filter cell.
In the exemplary diagram it is clear that at a certain particle size there is a minimum of filtration. This low point is called “MPPS = Most Penetration Particle Size”. This range exists for particle sizes between 0.1 µm to 0.3 µm and includes the filtration performance of the particles that experience has shown to be the most difficult to filter. Based on the degree of separation at this point, the filter cell is classified. With the help of the classification into different levels or classes based on different standards, the filter cell can be described accordingly so that it can be contrasted with the containment requirements for the process.
Conclusion
Knowledge of the prevailing conditions as well as the properties of the occurring dust play a very important role in the planning and design of the filter systems and especially of the filter elements. This results in the requirements that a filter cell inside the filter system must meet in order to produce exhaust air of the desired quality. With this knowledge, the filter cell that best fits the process can be determined from the abundance of available filter cells. A discussion with the manufacturer’s engineers is of fundamental importance, as they have the know-how to design and select the right components.