Contención mediante sistemas de filtrado – protección de los trabajadores en la industria farmacéutica: En muchas ramas de la industria, el polvo es un tipo de sustancia peligrosa debido a su composición y, por tanto, constituye un problema importante. En la industria farmacéutica en particular, la composición del polvo y la exposición diaria al polvo de los empleados es una cuestión importante, ya que las partículas generadas durante la producción se encuentran en el aire del lugar de trabajo. Sin más medidas de protección, pueden introducirse en las vías respiratorias de los trabajadores, donde pueden tener graves consecuencias para la salud. Por tanto, la protección de los trabajadores es especialmente importante -por ejemplo, en el ámbito de la fabricación de comprimidos-, ya que, por un lado, el mecanismo de autolimpieza de las vías respiratorias ya no puede hacer frente o eliminar por sí solo una cantidad excesiva de polvo y, por otro, los principios activos utilizados pueden convertirse en un peligro si los trabajadores están expuestos a ellos durante un periodo de tiempo prolongado.
Descubre cómo puedes proteger a tus empleados de los polvos peligrosos en nuestro artículo del blog.
Contención mediante sistemas de filtrado: protección eficaz de los trabajadores en la industria farmacéutica
En la producción de medicamentos, es importante eliminar las partículas del aire para que no entren en contacto con los empleados. Existen diversas medidas para proteger a los trabajadores en la fabricación de productos farmacéuticos. En el entorno farmacéutico, esta forma de protección de los empleados se denomina contención.
El proceso de producción desempeña un papel importante en la selección de una medida de contención adecuada:
- Hay soluciones para salas limpias que pretenden evitar que el polvo se escape al aire ambiente.
- Los separadores y esclusas instalados dentro de las líneas de producción garantizan que el polvo producido permanezca donde se genera y no se propague más.
Para crear un entorno seguro, también se puede purificar el aire. Los sistemas de filtrado especiales o los sistemas de extracción de polvo son una solución eficaz en este caso, ya que su tecnología de filtrado especial elimina incluso las partículas más finas del aire y crea así el aire más puro.
Hay una gran selección de sistemas de filtrado de polvo. Para los procesos de fabricación de pastillas que aquí se presentan, son adecuados los sistemas de desempolvado que utilizan un sistema de captación de polvo adecuado para garantizar que las partículas se recojan poco después del remolinado mediante un efecto de succión y se separen en el sistema de filtrado a través de un sistema de tuberías. Los desempolvadores activos de aire de salida se utilizan para evitar que el aire cargado de polvo se libere al medio ambiente durante la producción de granulados en polvo, por ejemplo. Estos sistemas de desempolvado suelen instalarse al final del proceso, toman el llamado gas bruto (=aire cargado de polvo) y separan las partículas de polvo del flujo de aire.
Por tanto, el sistema de aspiración de polvo sirve principalmente para eliminar de forma segura el polvo de la zona de producción y, por tanto, de la zona de peligro directo para los trabajadores y su salud. Esto subraya la importancia de la protección de los trabajadores en la industria, donde la seguridad en el lugar de trabajo es una prioridad absoluta. Por tanto, es esencial definir con precisión los cinco criterios siguientes para la selección de dichos equipos y seleccionar las medidas de protección adecuadas para el proceso definido y con las sustancias descritas, a fin de garantizar la protección de los trabajadores.
1. clasificación de la exposición al polvo en el lugar de trabajo (OEL)
No todo el polvo es igual
El polvo de la industria farmacéutica está formado por los componentes de las pastillas. Además del principio activo propiamente dicho, incluyen otros componentes que afectan a las propiedades de los comprimidos o medicamentos. El riesgo para los trabajadores puede variar en función del componente: No sólo el tipo de sustancia y sus componentes, sino también la dosis o el tiempo que el trabajador está expuesto a esta sustancia en su trabajo diario son decisivos para el riesgo para la salud de los trabajadores. Para ello, se define un valor límite en el lugar de trabajo para cada sustancia, el denominado LEP (Límite de Exposición Profesional), es decir, el límite de exposición profesional. Especifica la cantidad de sustancia que puede contener un metro cúbico de aire para que el trabajador no esté expuesto a ningún riesgo para la salud.
La base del OEL es el «NOEL = No-Observable Effect Level» (nivel sin efecto observable). Indica la dosis diaria con la que se acaba de prevenir un efecto crítico. Además de esta dosis diaria, se tienen en cuenta otros factores, como
- la adaptación de los datos animales a los datos humanos,
- diferentes sensibilidades de las personas,
- la duración de los estudios,
- la gravedad de los efectos o
- si se producían efectos significativos a pesar del cumplimiento.
Esto da como resultado la «ADE = Exposición Diaria Admisible (del Trabajador)». Se trata de la dosis diaria tolerable, que -basada en el aire respirado en un día- da el LEP.
En la industria farmacéutica, los estudios de los fabricantes de estas sustancias sirven de fuente para la evaluación de las sustancias.
2. asignación de los sistemas a los niveles OEB (requisitos de la industria farmacéutica)
Si no se dispone de información suficiente sobre una sustancia para determinar el valor OEL y, por tanto, evaluar el peligro, se utilizan sistemas de clasificación. Se utilizan para asignar la sustancia a una categoría de peligro (también conocida como clase o banda). Un sistema habitual es el de las «Bandas de Exposición Profesional», abreviado OEB. El nivel más bajo se aplica a las sustancias menos activas, es decir, las sustancias que no son tan peligrosas a no peligrosas. El nivel más alto se aplica a las sustancias más activas, es decir, aquellas para las que incluso una pequeña cantidad de material es suficiente para suponer un peligro importante.
Esta clasificación se compara con una clasificación de los sistemas de producción que se van a utilizar: Según el diseño, pueden escaparse distintas cantidades de polvo durante el proceso de producción. A continuación, hay que seleccionar las propiedades de los sistemas en función de la clasificación de la sustancia. Esto significa, por ejemplo, que para las sustancias menos activas de la categoría OEB1, pueden seleccionarse sistemas con pocas o ninguna medida de contención para proteger a los trabajadores, ya que la sustancia no supone un peligro.
En principio, debe garantizarse que la cantidad de sustancia que se escapa del sistema seleccionado esté siempre por debajo del valor límite de la misma sustancia para descartar cualquier riesgo para los trabajadores.
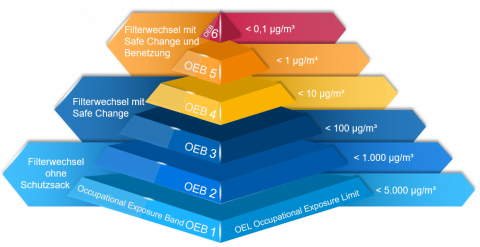
3. comprobación de los requisitos especiales de los sistemas de filtrado para la producción de comprimidos
El equipamiento del sistema de filtrado viene determinado por el valor OEL de las sustancias utilizadas. Debe tenerse en cuenta todo el proceso, es decir, todo el flujo de personal y material: La sección con los requisitos más elevados define el nivel de OEB para todos los componentes y, por tanto, también para el sistema de filtrado. Para las sustancias que son menos críticas, bastan medidas más sencillas que para las sustancias que requieren una categorización superior debido a su toxicidad.
4. observancia de las medidas necesarias de equipamiento y mantenimiento de los sistemas de filtración
Para garantizar la fiabilidad del proceso durante la producción de comprimidos, se utilizan en su mayor parte sistemas de filtros regenerables para un desempolvado eficaz. En los sistemas de filtros regenerables, los elementos filtrantes se limpian con aire comprimido después de unos tiempos determinados para evitar que se obstruyan antes de tiempo. Esto aumenta significativamente la vida útil del filtro. En cuanto el filtro haya llegado al final de su vida útil, es decir, cuando no se pueda eliminar el polvo del filtro a pesar de la regeneración, hay que cambiarlo. El cambio se realiza con las medidas de protección adecuadas para garantizar que el operario y el entorno inmediato no entren en contacto con la sustancia. Existen diversas medidas técnicas de contención para la manipulación segura del sistema de desempolvado.
El polvo que sale de las celdas del filtro durante la limpieza se recoge junto con las partículas de polvo más grandes en un recipiente de recogida de polvo. Este recipiente también debe cambiarse regularmente. Al igual que en el cambio de las celdas filtrantes, en este caso es igual de importante cumplir las medidas de contención adecuadas, en función de la composición del polvo, para garantizar la protección de los trabajadores.
5. consideración de las condiciones especiales de los sistemas de desempolvado en la industria farmacéutica
Además del riesgo para la salud que suponen los ingredientes, también existe el riesgo que supone la existencia del propio polvo: las empresas farmacéuticas procesan principalmente sustancias orgánicas. Generalmente son inflamables y, en determinadas condiciones, pueden provocar un riesgo de explosión en el proceso. Por tanto, el sistema de filtrado debe estar equipado con las medidas adecuadas específicamente para los requisitos de cada empresa. Una alternativa en este caso son los sistemas de aspiración de polvo con diseño antideflagrante que cumplen los requisitos de la Directiva ATEX 2014/34 aplicable a estos sistemas.
Conclusión
Los modernos sistemas de desempolvado desempeñan un papel fundamental en la protección de la salud de tus empleados, la protección del medio ambiente y la fiabilidad de los procesos de fabricación de productos farmacéuticos. Los siguientes criterios deben aclararse de antemano para facilitar a todos los implicados la selección del sistema de aspiración de polvo adecuado para garantizar la protección de los trabajadores a largo plazo:
- Exposición máxima al polvo en el lugar de trabajo (OEL)
- Requisitos de la industria farmacéutica
- Requisitos especiales de los sistemas de filtrado para la producción de comprimidos
- Equipamiento necesario y medidas de mantenimiento de los sistemas de filtrado
- Condiciones especiales de los sistemas de desempolvado en la industria farmacéutica
Si tienes en cuenta estos cinco criterios, podrás seleccionar el sistema de filtrado óptimo para las necesidades específicas de tu empresa, garantizando un entorno prácticamente libre de polvo y seguro para tus empleados y la producción a largo plazo de tus productos.