En la industria farmacéutica se producen inevitablemente polvos peligrosos. Se aplican medidas de contención para reducir el riesgo de contaminación y garantizar así una mayor protección de los trabajadores. Su objetivo es crear un espacio protegido para los trabajadores y el medio ambiente. Entre otras cosas, los sistemas de aspiración de polvo se utilizan para extraer, filtrar y separar de forma segura el polvo a medida que se genera. Sin embargo, como el polvo extraído no se transporta fuera, sino sólo del punto de recogida al sistema, los sistemas de extracción de polvo también deben estar equipados con medidas de contención.
En este artículo, aprenderás qué medidas técnicas puedes aplicar en la industria farmacéutica para reducir el riesgo de contaminación y garantizar así una mayor protección de los empleados.
Medidas técnicas
Los operadores de las instalaciones de producción tienen la obligación de proteger a los empleados de los peligros durante su trabajo diario. Esta obligación puede cumplirse considerando soluciones técnicas de contención al planificar un sistema.
De acuerdo con la Directiva 98/24/CE, debe tenerse en cuenta el denominado principio «STOP» a la hora de seleccionar las medidas de confinamiento en cuestión:
- Sustitución dela sustancia de riesgo – Comprueba si hay sustancias menos toxicológicas
- Medidas técnicas– actualización de los sistemas con soluciones de seguridad adecuadas
- Medidas organizativas: planificación para que los trabajadores no estén expuestos a sustancias peligrosas durante demasiado tiempo.
- Equipo de protección individual– Utilízalo cuando todas las demás medidas no sean aplicables
Las medidas utilizadas en la industria farmacéutica se clasifican en dos grupos:
Medidas de contención primaria y medidas de contención secundaria.
Mientras que las medidas primarias de contención garantizan directamente que no pueda escapar polvo peligroso de las instalaciones de producción, las medidas secundarias sirven para capturar cualquier partícula que se produzca en las instalaciones de producción y evitar que se propague. Sin embargo, cada caso debe examinarse individualmente para determinar qué medidas de contención son adecuadas. El factor decisivo aquí es siempre la exposición o el peligro que suponen los polvos producidos, así como los requisitos (legales) que deben cumplirse (por ejemplo, BPF, HSE).
Es obligatoria una evaluación del riesgo para determinar el riesgo y, por tanto, el alcance de las medidas. En ella, el grado de riesgo que plantea la sustancia en cuestión está vinculado a la exposición (duración de la exposición).
El objetivo es dar prioridad a las medidas técnicas que proporcionen una protección óptima a los trabajadores. El objetivo debe ser encontrar soluciones sensatas que se adapten a cada fase del ciclo de vida del producto. Por tanto, no sólo es importante que la fabricación del producto sea segura, sino también proteger a los trabajadores durante el montaje, el desmontaje y la eliminación de la planta de producción.
Contención primaria: evitar que escapen partículas
La producción de polvos peligrosos durante la fabricación de medicamentos es inevitable. Lo más seguro para las personas y el medio ambiente es que los polvos y partículas desprendidas de sustancias peligrosas no salgan de donde se crean en primer lugar: en la propia planta de producción.
Hay varias opciones técnicas para conseguirlo, algunas de las cuales se enumeran a continuación. Combinando distintas opciones, se puede aumentar al máximo la protección de los trabajadores y mejorar la facilidad de uso.
Guantera, RABS y aislante
Para evitar la propagación de partículas, es posible encapsular y encerrar la zona de exposición. Dependiendo del potencial de riesgo, esto puede realizarse con las siguientes medidas:
- Caja de guantes – caja con panel de plexiglás y guantes incrustados
- Recinto RABS (Sistema de Barrera de Acceso Restringido) – Recinto con conductos de aire integrados Medidas
- Aislador – dispositivo que permite una presión negativa definida y una estanqueidad extremadamente alta
Sistemas de extracción y filtrado
Los sistemas de extracción se utilizan para extraer el aire con las sustancias que contiene directamente en el punto en que se produce y eliminarlo de la zona de trabajo del trabajador. El aire extraído se filtra y así se limpia de sustancias peligrosas. Los llamados extractores de polvo tienen insertos filtrantes que unen las partículas a sí mismas y así las eliminan del aire. El resultado es un aire limpio y no contaminado. Las sustancias que se producen y la cantidad de aire que hay que filtrar determinan el número de elementos filtrantes y su clase de filtro (qué cantidades de partículas de un determinado tamaño se separan del aire).
Diferenciación por tamaño de partículaContención secundaria: evitar la dispersión de partículas
Durante los trabajos de mantenimiento y reparación o en caso de fallos en el proceso de producción, la contención puede romperse y las sustancias peligrosas pueden escapar. Para estos casos, las propias salas de producción se diseñan de forma que se minimice el riesgo de propagación y contaminación ulterior de los empleados y de las salas de producción adyacentes.
La selección de opciones se basa en un análisis de los lugares de trabajo (por ejemplo, flujo de materiales, rutas del personal, etc.) y en evaluaciones del riesgo de las sustancias implicadas.
Para la contención secundaria, por ejemplo, existen las siguientes soluciones:
Zonas de trabajo con esclusas
Sólo se puede acceder a los lugares de trabajo a través de esclusas para la descontaminación. Según el diseño, se pueden utilizar entradas y salidas separadas o separar el flujo de materiales de las rutas peatonales. En las esclusas, las personas y los materiales se limpian de los contaminantes que llegan del exterior y que, por tanto, suponen un riesgo para el proceso de producción o el producto. Por otra parte, el uso de esclusas también impide que entren sustancias desde el interior y contaminen las zonas vecinas.
Zonas de trabajo con cascadas presurizadas
En cada zona prevalecen presiones de aire diferentes, que controlan el movimiento de las partículas suspendidas en el aire.
- Presión positiva – se utiliza cuando no se permite la entrada de sustancias en el local
- Presión negativa: se utiliza cuando no se permite que ninguna sustancia salga de la sala.
Soluciones para salas blancas
El concepto de sala blanca garantiza que la cantidad de partículas contenidas en el aire siga siendo limitada. Aquí entran en juego varias normativas, todas ellas encaminadas a reducir la contaminación o facilitar la limpieza. Los reglamentos se aplican, por ejemplo, a:
- la naturaleza de las superficies: tan grandes como sea posible para minimizar el número de juntas y simplificar la limpieza
- la elección de los materiales – superficies lisas
- la construcción de los techos: herméticos, con iluminación empotrada y ventilación
- el flujo de material: ningún material contaminado puede salir de la sala a menos que se lleve a cabo una descontaminación adecuada o un envasado seguro.
- limpieza del aire ambiente – en este caso, la filtración se realiza mediante filtros de aire de impulsión y extracción equipados con celdas filtrantes adecuadas. Se aplican medidas similares a las medidas técnicas de contención primaria:
- El cambio de filtro debe realizarse bajo ciertas medidas de protección.
- Las unidades de tratamiento de aire (UTA) deben ser revisadas y mantenidas periódicamente en cuanto a su rendimiento. Esto se aplica, por ejemplo, al rendimiento del filtro cuando está instalado.
- La eficacia de filtración de los filtros se comprueba mediante las llamadas pruebas DEHS antes de la puesta en servicio.
Medidas de contención en los sistemas de filtrado
Al diseñar los sistemas de proceso y producción, se utilizan distintas opciones de protección para los sistemas de desempolvado:
Cambio seguro
Según este principio, los empleados pueden sustituir las celdas filtrantes contaminadas de un sistema de filtrado sin entrar en contacto con el propio material filtrante contaminado ni con el polvo que pueda levantarse.
1. retirada del material/célula filtrante usada
En este caso, el sistema de filtrado está equipado con un marco alrededor de la abertura del filtro con una bolsa protectora (bolsa de plástico) adherida. Al cambiarla, se coloca una segunda bolsa de plástico protectora sobre el armazón y se sujeta herméticamente con un anillo de goma.
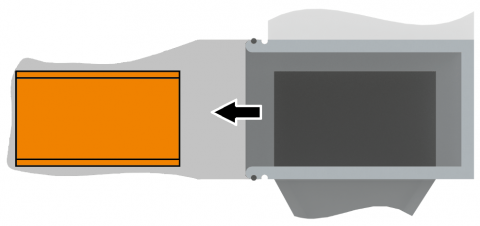
2. cerrar la bolsa protectora
El elemento filtrante se introduce en la nueva bolsa de plástico junto con la bolsa protectora existente (Fig. 1). A continuación, se sella firmemente entre el bastidor y la célula filtrante en dos puntos y se separa entre los puntos de sellado (fig. 2). La parte separada de la bolsa protectora con la célula filtrante en su interior puede eliminarse ahora adecuadamente.
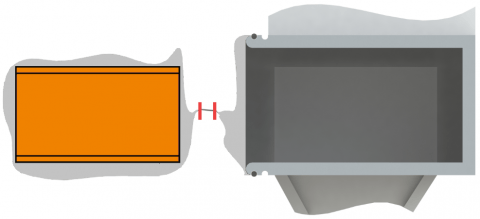
3. introducción del nuevo material/nueva célula filtrante
A continuación, se coloca un nuevo elemento filtrante en una nueva bolsa protectora, que se vuelve a fijar al marco de la abertura del filtro. El resto de la bolsa protectora vieja se retira del bastidor junto a la bolsa protectora nueva y se coloca detrás de la celda nueva para que pueda introducirse en el sistema de filtrado (Fig. 3). La nueva bolsa protectora se enrolla y se guarda detrás de la tapa de la abertura del filtro.
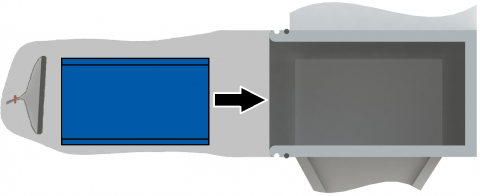
El uso de bolsas protectoras garantiza que el sistema permanezca sellado durante todo el proceso y que no puedan escapar sustancias. Para mayor seguridad, la célula filtrante cargada puede humedecerse con agua inmediatamente antes de retirarla, a fin de aglutinar el polvo y garantizar su adherencia a las células filtrantes. Esto reduce significativamente la posible exposición durante el cambio de filtro.
Sistemas de liners sin fin
Una camisa sin fin es un método seguro para cambiar la descarga de polvo en un sistema de desempolvado. Consiste en un cartucho de tubo de aluminio. La longitud de la manguera de la película está dimensionada de modo que la descarga pueda vaciarse varias veces sin tener que cambiar cada vez la manguera de la película.
El tubo de película está sellado en el extremo inferior para que el material pueda caer en él. Una vez alcanzado un determinado nivel de llenado, el tubo de película se sella firmemente por encima del material y se corta. Es importante que el sellado se realice en dos puntos y que el tubo de película esté separado entre los puntos de sellado.
Sistemas de cierre
La elección de los sistemas de cierre viene determinada por las sustancias que se producen. Hay sistemas sencillos, como las bridas para cables, que bastan para utilizar sustancias menos peligrosas. Dado que pueden quedar residuos de las sustancias en los puntos de sellado, se recomienda utilizar sistemas de sellado especiales para sustancias peligrosas. Consisten en abrazaderas que cierran herméticamente la bolsa protectora y herramientas especiales para separar las abrazaderas de modo que no pueda escapar el polvo.
Limpieza del sistema de filtrado desde el interior
Además de las medidas ya mencionadas, que se utilizan durante el funcionamiento, también hay varias opciones que se utilizan durante el mantenimiento y la reparación de los sistemas. Por ejemplo, los interiores de los sistemas pueden lavarse con agua antes de abrirlos para aglutinar el polvo:
Lavado en el lugar (WIP):
Antes de abrir el sistema, se humedecen las superficies con agua para aglutinar el polvo. Se requiere una limpieza manual posterior para obtener un efecto de limpieza completo.
Limpieza in situ (CIP):
Aquí, el interior del sistema se limpia por completo antes de realizar el mantenimiento o la reparación. La limpieza debe estar siempre cualificada y validada para los procesos que entran en contacto con el producto.
Conclusión
En la industria farmacéutica, hay varias formas de proteger a los empleados y los procesos de las sustancias peligrosas. Se pueden determinar utilizando el principio STOP. A la hora de seleccionar las medidas técnicas para los sistemas de desempolvado, es esencial tener en cuenta previamente los propios procesos y las sustancias que se producen. El peligro resultante determina el grado de contención que debe utilizarse.
En la industria farmacéutica, las aplicaciones pueden dividirse en dos grupos: Las medidas de contención primaria, que garantizan que no se escape ningún polvo peligroso, y las medidas de contención secundaria, que capturan cualquier partícula que se produzca y evitan que se propague. Combinando varias medidas técnicas en los sistemas de desempolvado, se aumenta al máximo la facilidad de uso para los empleados y la seguridad laboral, y se evita la contaminación.
En este caso, los sistemas de desempolvado modernos desempeñan un doble papel: por un lado, sirven como medida de contención independiente y técnica; por otro, hay que tomar medidas de contención para ellos con el fin de proteger a los trabajadores y al medio ambiente durante su uso.