Um den Staub, der während der Produktion entsteht, zu binden, kommen in der Pharma- und Chemie-Industrie Entstauber bzw. Filteranlagen zum Einsatz. In den darin verbauten Filterzellen werden die Partikel aus der Luft abgeschieden, so dass am Ende saubere Luft entsteht und die Gefahr durch den Staub eliminiert ist.
Die Art des Staubes bzw. die Zusammensetzung des Luftgemisches sowie die Anforderungen aus dem Prozess heraus ergeben die Auswahlkriterien für die Filterzellen.
Filterzellen sind in verschiedenen Arten, Ausführungen und Materialien verfügbar. Der folgende Artikel soll einen kurzen Überblick über die Bauweisen und Einteilungen der Filter geben.
Um die einzelnen Filterzellen in ihren verschiedenen Ausführungen miteinander vergleichen zukönnen bzw. sie den Anforderungen aus dem Prozess entgegen zu stellen, gibt es ein Klassifizierung-System, das anhand von Normen festgelegt ist.
Die korrekte Auswahl und Wartung von Filteranlagen und deren Komponenten ist entscheidend, um die Luftqualität zu sichern, die Sicherheit und Effizienz des Produktionsprozesses zu gewährleisten und die Einhaltung von Umwelt- und Gesundheitsvorschriften zu garantieren. Der folgende Artikel bietet einen detaillierten Überblick über die verschiedenen Bauweisen, Filtergruppen und Einteilungen von Filtern, um Fachleuten in der Industrie bei der Auswahl der besten Filtrationslösung für ihre spezifischen Bedürfnisse zu unterstützen.
Klassifizierung der Filterzellen
Um die verschiedenen Filterklassen bzw. Filtergruppen richtig zuordnen zu können, soll zunächst einmal eine Übersicht über die betrachteten Luftfilter folgen, um zu zeigen, wann welche Einteilung greift.
Übersicht über Luftfilter
Luftfilter werden nach ihrer Fähigkeit eingeteilt, wie gut sie Partikel unterschiedlicher Größen abscheiden können.
Es gibt „Staubfilter“, die für hohe Staubbeladungen und gröbere Partikel in der Luft eingesetzt werden. Diese unterteilen sich noch einmal im „Grobstaubfilter“ und „Feinstaubfilter“ – in Abhängikeit der Partikelgröße. Für diese Filter erfolgt die Klassifizierung anhand der Norm EN ISO 16890.
Sollen feinere bzw. feinste Partikel gefiltert werden, kommen „Schwebstofffilter“ zum Einsatz. Hier erfolgt eine weitere Unterteilung in „Standard-Schwebstofffilter“ und „Hochleistungs- Schwebstofffilter“. Auch hier erfolgt die Klassifizierung nach der tatsächlichen Partikelgröße. Die Klassifizierung erfolgt anhand der Norm EN 1822-1.
Einteilung gemäß EN ISO 16890
Die Grundlage der Klassifizierung bildet der Abscheidegrad der Filterzelle. Dieser sagt aus, wie viele Partikel von dem Filtermedium zurückgehalten werden bzw. wie viele Partikel nach Durchströmen des Filters weiterhin in der Abluft zu finden sind. Der Wert, der hier von Bedeutung ist, ist die Abscheideleistung von Partikeln mit Größen von 0,3 µm bis 10 µm.
Anhand dieses Wertes kann gemäß der Norm EN ISO 16890 die entsprechende Filtergruppe zugeordnet werden.
Die Norm sieht dabei 3 Stufen vor, nach denen die Filterzellen klassifiziert werden:
- PM1: Abscheideleistung für Partikel bis 1 µm (0,3-1 µm)
- PM2,5: Abscheideleistung für Partikel bis 2,5 µm (0,3-2,5 µm)
- PM10: Abscheideleistung für Partikel bis 10 µm (0,3-10 µm)
Werden mindestens 50% der angegebenen Partikel abgeschieden, hat die Filterzelle die entsprechende Gruppe erreicht. In dem Fall spricht man von der „Minimal-Effinzienz“, die an einer neuen Filterzelle ermittelt wird. Parallel dazu wird auch die „mittlere Effizienz“ über die gesamte Filterzelle gemessen.
Bei dem Verfahren zur Ermittlung der Filtergruppe werden also zunächst zusammen mit der mittleren Effinzienz die Minimal-Effizienz für die 3 Partikelgrößen ermittelt. Bei der Stufe, in der mindestens 50% der Abscheidung erreicht wird, wird die mittlere Effinzienz genommen und auf den nächsten 5-er Schritt abgerundet. Mit diesem Werten kann dann die Klassifzierung angegeben
werden.
Beispiel: ISO ePM2,5 80%
Kommt es vor, dass eine Filterzelle die Bedingungen für mehrere Stufen erfüllt, obliegt es dem Hersteller der Filterzellen, welche Angabe er auf dem Produkt macht.
Einteilung gemäß EN 1822-1
Die Norm DIN EN 1822-1 bezieht sich auf die Einteilung von Hochleistungs-Partikel- und Hochleistungs-Schwebstofffilter, wie sin der Reinraumtechnik oder der Pharma-Industrie Anwendung finden. Neben der Einteilung der Filterzellen wird auch die Produktion und Prüfung in der Norm festgelegt. Hier ist zu beachten, dass für die Klassifizierung der Filter der Teil 1 der Norm DIN EN 1822 gültig ist – die Vorgaben für die Produktion und Prüfung sind allerdings in den Teilen 2-5 der ISO 29463 zu finden.
Die Norm DIN EN 1822-1 unterscheidet in Filtergruppen und Filterklassen:
Filtergruppe | Filterklasse | Integralwert Abscheidegrad in MPPS | Integralwert Durchlassgrad in MPPS | Lokalwert Abscheidegrad in MPPS | Lokalwert Durchlassgrad in MPPS |
EPA = Hochleistungs- Partikelfilter | E10 E11 E12 | ≥ 85 % ≥ 95 % ≥ 99,5 % | ≤ 15 % ≤5% ≤ 0,5 % | – – – | – – – |
HEPA = Schwebstofffilter | H13 H14 | ≥ 99,95 % ≥ 99,995 % | ≤ 0,05 % ≤ 0,005 % | ≥ 99,75 % ≥ 99,975 % | ≤ 0,25 % ≤ 0,025 % |
ULPA = Hochleistungs- Schwebstofffilter | U15 U16 U17 | ≥ 99,999 5 % ≥ 99,999 95 % ≥ 99,999 995 % | ≤ 0,000 5 % ≤ 0,000 05 % ≤ 0,000 005 % | ≥ 99,997 5 % ≥ 99,999 75 % ≥ 99,9999 9 % | ≤ 0,002 5 % ≤ 0,000 25 % ≤ 0,000 1 % |
Die Grundlage der Einteilung ist hier der minimale Abscheidegrad der Filterzelle bei Partikeln der Größe 0,1 – 0,3 µm, dem „MPPS“, wie er im Beitrag Filter-Einflussfaktoren-Prinzip erläutert ist.
Die Klassifizierung läuft in drei Schritten ab: zunächst wird am ungefalteten Filtermedium die Partikelgröße am Abscheideminimum ermittelt (MPPS). Im zweiten Schritt wird die Leckfreiheit (= lokaler Abscheidegrad) geprüft. Als letztes wird unter Verwendung eines Prüfaerosols für die Partikelgröße im Abscheideminimum der integrale Abscheidegrad des Filterelementes ermittelt.
Anhand der gewonnen Werte kann mit Hilfe der Übersicht in der Norm das Filterelement der entsprechenden Filterklasse zugeordnet werden.
Die folgende Abbildung zeigt, in welchen Bereichen die verschiedenen Filterklassen bzw. Filtergruppen zum Einsatz kommen können.
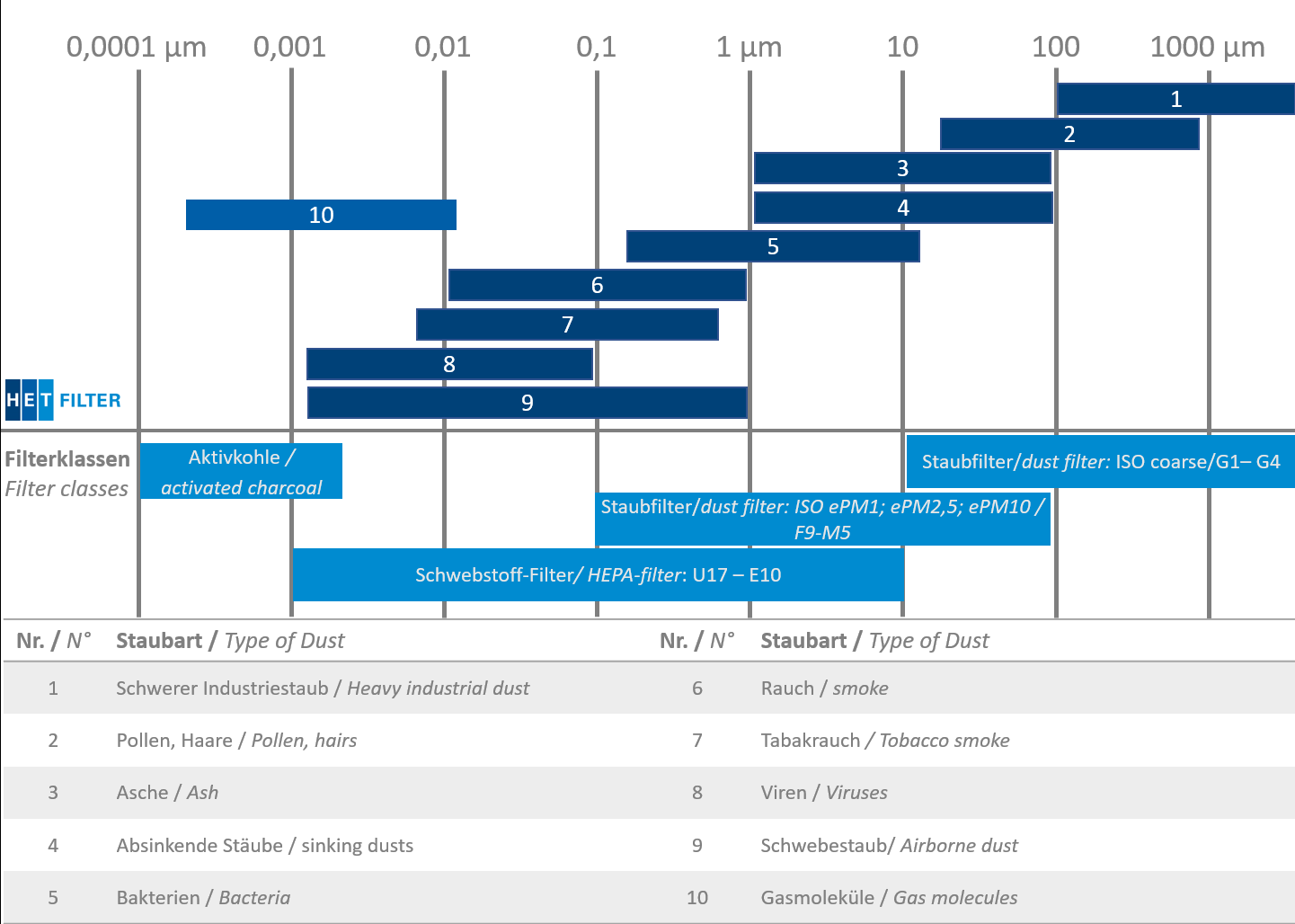
Bauweisen von Filterzellen
Für Filterelemente stehen je nach Hersteller, Anwendung und Anforderung verschiedene Bauweisen zur Verfügung.
Für die Auswahl spielen unterschiedliche Faktoren eine Rolle: von Anforderungen aus dem Prozess heraus über die Einbausituation, resultierend aus der Konstruktion der Filteranlage bis hin zur Kostenfrage gilt es vieles zu beachten.
In diesem Artikel sollen einmal die Bauweisen „Patronenfilter“, „Lamellenfilter“ sowie „Kassettenfilter“ betrachtet werden – also die Filter, die in den Anlagen der HET Filter GmbH zum Einsatz kommen.
Die drei Filterbauweisen verfügen über unterschiedliche Eigenschaften, die nachfolgend beschrieben werden:
Patronenfilter
Aufbau:
Beim Patronenfilter befindet sich das gefaltete Filtermedium (Filtervlies) innerhalb eines zylindrischen Trägerkorbs. Diese Gestaltung lässt eine kostengünstige Herstellung zu.
Einsatz:
bei Luft mit hoher Staubbeladungen
Klassifizierung:
Grob- , Feinfilter gemäß EN ISO 16890
Besonderheiten:
Aufgrund der Konstruktion ist der Wechsel des Filters nicht unter Safe-Change- Bedingungen möglich, d. h., dass mit diesem Filter nur geringe Containment- Anforderungen erfüllt werden können. Welche das sind, wird in den Blog-Artikeln zum Thema „Containment“ beschrieben.
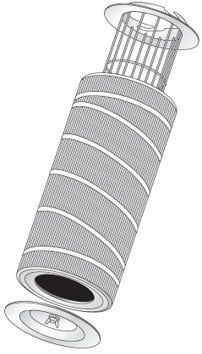
Lamellenfilter
Aufbau:
Lamellenfilter bestehen aus einem
gefalteten Vlies, das entweder waagerecht
oder senkrecht eingebaut werden kann. Die
jeweilige Filterstufe eines Entstaubers setzt
sich aus mehreren dieser Lamellenfilter
zusammen. Durch die Bauweise können die
einzelnen Lamellenfilter mittels gepulster
Druckluft abgereinigt werden. Die Druckluft
versetzt die Elemente in Schwingungen, so
dass sich die Partikel lösen und in den
Staubaustrag fallen. Aufgrund des einfachen
Aufbaus ist diese Filterart vergleichsweise
günstig.
Einsatz:
bei Luft mit hoher Staubbeladungen,
bei schwierigen Stäuben
Klassifizierung:
Grob- , Feinfilter gemäß EN ISO 16890
Besonderheiten:
Aufgrund der Konstruktion ist der Wechsel des Filters nicht unter Safe-Change- Bedingungen möglich, d. h., dass mit diesem Filter nur geringe Containment- Anforderungen erfüllt werden können. Welche das sind, wird in den Blog-Artikeln zum Thema „Containment“ beschrieben.
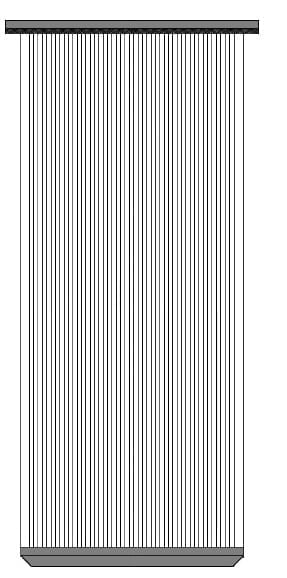
Kassettenfilter
Aufbau:
Beim Kassettenfilter befindet sich das
Medium in einem robusten, leitfähigen
Gehäuse aus verzinktem Stahl oder
Edelstahl. Beim Einsatz in nicht-
explosionsgefährdeten Bereichen kann der
Rahmen auch aus Holz (MDF) bestehen.
Das Filtervlies ist lagenförmig bzw. V-förmig
gefaltet und mittels Vergussmasse mit dem
Gehäuse vergossen. Zwischen den einzelnen
Lagen befinden sich Abstandshalter, die
dafür sorgen, dass die Lagen während des
Ansaugens der Luft geöffnet bleiben und die
Luft ungehindert durch den Filter strömen
kann. Außerdem sind sie ableitfähig, um
elektrostatische Aufladungen zu verhindern.
Einsatz:
für feinste Stäube der Pharma-Industrie,
Staubbeladungen bis 2.000 mg/m3
Volumenströme bis 2.000 m3/h
durch die standardisierten Abmessungen in
diversen Anlagen einsetzbar.
Klassifizierung:
HEPA-Filter gemäß EN 1822;
Staubfilter gemäß EN ISO 16890
Besonderheiten:
der Wechsel des Filters ist unter Safe-
Change-Bedingungen möglich, d. h., dass
mit diesem Filter u. a. Containment-
Anforderungen bis OEB6 erfüllt werden
können.
Die Filterzellen sind abreinigbar, wodurch
sich die Standzeiten erhöhen lassen.
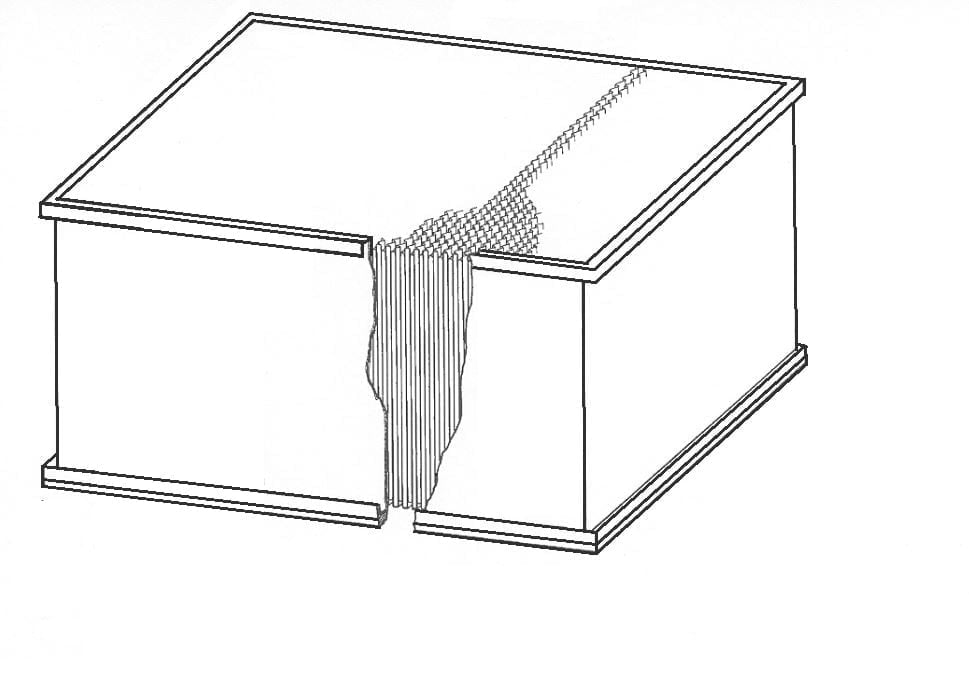
Fazit
Filterzellen sind in einer großen Bandbreite an Eigenschaften und Konstruktionsmöglichkeiten verfügbar. Die Auswahl richtet sich nach den Eigenschaften des Staubs sowie den Anforderungen des Prozesses. Deswegen ist es für die Auslegung der Filteranlagen unabdinbar, den Staub genau zu kennen und die Daten an die Hersteller der Filtergruppen zu übermitteln. Nur so können die richtigen Filterelemente ausgewählt werden, so dass am Ende deren Aufgabe erfüllt ist – das Bereitstellen sauberer Luft, ohne Gefahr für Mensch und Umwelt.