Contenimento tramite sistemi di filtraggio – protezione dei dipendenti nell’industria farmaceutica: In molti settori industriali, la polvere è un tipo di sostanza pericolosa a causa della sua composizione e rappresenta quindi un problema importante. Nell’industria farmaceutica, in particolare, la composizione della polvere e l’esposizione giornaliera dei dipendenti sono un problema importante, poiché le particelle generate durante la produzione sono presenti nell’aria del luogo di lavoro. Senza ulteriori misure di protezione, possono penetrare nelle vie respiratorie dei dipendenti e causare gravi problemi di salute. La protezione dei dipendenti è quindi particolarmente importante, ad esempio nel settore della produzione di compresse, in quanto, da un lato, il meccanismo di autopulizia delle vie respiratorie non è più in grado di gestire o rimuovere da solo una quantità eccessiva di polvere e, dall’altro, gli ingredienti attivi utilizzati possono diventare un pericolo se i dipendenti vi sono esposti per un periodo di tempo prolungato.
Scopri come proteggere i tuoi dipendenti dalle polveri pericolose nel nostro articolo sul blog.
Contenimento attraverso sistemi di filtraggio: un’efficace protezione dei dipendenti nell’industria farmaceutica
Nella produzione di farmaci, è importante rimuovere le particelle dall’aria in modo che non entrino in contatto con i dipendenti. Esistono diverse misure per proteggere i dipendenti durante la produzione di prodotti farmaceutici. Nell’ambiente farmaceutico, questa forma di protezione dei dipendenti è nota come contenimento.
Il processo di produzione gioca un ruolo importante nella scelta di una misura di contenimento adeguata:
- Esistono soluzioni per le camere bianche che mirano a evitare la fuoriuscita di polvere nell’aria ambiente.
- I separatori e le camere di compensazione installati all’interno delle linee di produzione assicurano che la polvere prodotta rimanga nel luogo in cui è stata generata e non si diffonda ulteriormente.
Per creare un ambiente sicuro, l’aria può anche essere purificata. I sistemi di filtraggio speciali o i sistemi di aspirazione della polvere sono una soluzione efficace in questo caso, poiché la loro speciale tecnologia di filtraggio rimuove anche le particelle più sottili dall’aria e crea così un’aria più pura.
Esiste un’ampia scelta di sistemi di filtraggio della polvere. Per i processi di produzione di compresse qui presentati, i sistemi di aspirazione della polvere con un sistema di raccolta della polvere adeguato assicurano che le particelle vengano raccolte subito dopo la rotazione grazie a un effetto di aspirazione e separate nel sistema di filtraggio attraverso un sistema di tubature. I depolveratori attivi per l’aria di scarico vengono utilizzati, ad esempio, per evitare che l’aria carica di polvere venga rilasciata nell’ambiente durante la produzione di granulati in polvere. Questi sistemi di depolverizzazione sono spesso installati alla fine del processo, assorbono il cosiddetto gas grezzo (=aria carica di polvere) e separano le particelle di polvere dal flusso d’aria.
Il sistema di aspirazione serve quindi principalmente a rimuovere in modo sicuro la polvere dall’area di produzione e quindi dalla zona di pericolo diretto per i dipendenti e la loro salute. Questo sottolinea l’importanza della protezione dei dipendenti nell’industria, dove la sicurezza sul posto di lavoro è una priorità assoluta. È quindi fondamentale definire con precisione i seguenti cinque criteri per la scelta di tali apparecchiature e selezionare le misure di protezione appropriate per il processo definito e con le sostanze descritte, al fine di garantire la protezione dei dipendenti.
1. classificazione dell’esposizione alla polvere sul luogo di lavoro (OEL)
Non tutta la polvere è uguale
La polvere dell’industria farmaceutica è costituita dai componenti delle compresse. Oltre all’ingrediente attivo vero e proprio, sono inclusi altri componenti che influenzano le proprietà delle compresse o dei farmaci. Il rischio per i dipendenti può variare a seconda del componente: Non solo il tipo di sostanza e i suoi componenti, ma anche la dose, ovvero il tempo in cui il dipendente è esposto a questa sostanza nel suo lavoro quotidiano, sono determinanti per il rischio per la salute dei dipendenti. A tal fine, per ogni sostanza viene definito un valore limite sul luogo di lavoro, il cosiddetto OEL (Occupational Exposure Limit), ovvero il limite di esposizione professionale. Questo valore indica la quantità di sostanza che può essere contenuta in un metro cubo di aria in modo che il dipendente non sia esposto ad alcun rischio per la salute.
La base del LEP è il “NOEL = No-Observable Effect Level”. Indica la dose giornaliera alla quale un effetto critico viene semplicemente evitato. Oltre a questa dose giornaliera, vengono presi in considerazione altri fattori, come ad esempio
- l’adattamento dei dati animali a quelli umani,
- sensibilità diverse delle persone,
- la durata degli studi,
- la gravità degli effetti o
- se si verificano effetti significativi nonostante la conformità.
Si ottiene così la “ADE = Acceptable Daily (Worker) Exposure”. Si tratta della dose giornaliera tollerabile che, in relazione all’aria respirata in un giorno, dà luogo al OEL.
Nell’industria farmaceutica, gli studi dei produttori di queste sostanze servono come fonte per la valutazione delle sostanze.
2. assegnazione dei sistemi ai livelli OEB (requisiti dell’industria farmaceutica)
Se per una sostanza non sono disponibili informazioni sufficienti per determinare il valore OEL e quindi valutare il pericolo, si ricorre a sistemi di classificazione. Questi sistemi vengono utilizzati per assegnare la sostanza a una categoria di pericolo (nota anche come classe o fascia). Un sistema comune è quello delle “Bande di esposizione professionale”, o OEB in breve. Il livello più basso si applica alle sostanze meno attive, cioè a quelle che non sono così pericolose da essere innocue. Il livello più alto, a sua volta, si applica alle sostanze più attive, cioè a quelle sostanze per le quali anche una piccola quantità di materiale è sufficiente a rappresentare un grave pericolo.
Questa categorizzazione viene confrontata con una classificazione dei sistemi di produzione da utilizzare: A seconda del progetto, durante il processo di produzione possono fuoriuscire diverse quantità di polvere. A seconda della classificazione della sostanza, è necessario selezionare le proprietà dell’attrezzatura. Ciò significa, ad esempio, che per le sostanze meno attive della categoria OEB1 è possibile scegliere attrezzature con misure di contenimento minime o nulle per proteggere i dipendenti, in quanto la sostanza non rappresenta un pericolo.
In linea di massima, è necessario assicurarsi che la quantità di sostanza che fuoriesce dal sistema selezionato sia sempre inferiore al valore limite della stessa sostanza per escludere qualsiasi rischio per i dipendenti.
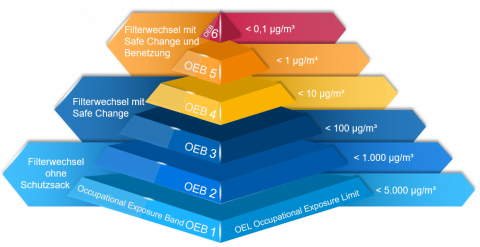
3. verifica i requisiti speciali dei sistemi di filtraggio per la produzione di compresse
La dotazione del sistema di filtraggio è determinata dal valore OEL delle sostanze utilizzate. È necessario prendere in considerazione il processo completo, ossia l’intero flusso di personale e di materiali: La sezione con i requisiti più elevati determina il livello OEB per tutti i componenti e quindi anche per il sistema di filtraggio. Per le sostanze meno critiche sono sufficienti misure più semplici rispetto a quelle che richiedono una classificazione più elevata a causa della loro tossicità.
4. il rispetto delle attrezzature e delle misure di manutenzione necessarie per i sistemi di filtraggio.
Per garantire l’affidabilità del processo durante la produzione di compresse, i sistemi filtranti rigenerabili sono largamente utilizzati per una depolverizzazione efficiente. Nei sistemi filtranti rigenerabili, gli elementi filtranti vengono puliti con aria compressa dopo tempi prestabiliti per evitare un intasamento prematuro. Questo aumenta notevolmente la durata del filtro. Non appena la durata del filtro viene raggiunta, cioè la polvere non può essere rimossa dal filtro nonostante la rigenerazione, il filtro deve essere sostituito. La sostituzione viene effettuata con misure di protezione adeguate per garantire che l’operatore e l’ambiente circostante non entrino in contatto con il materiale. Sono disponibili diverse misure tecniche di contenimento per la gestione sicura del sistema di aspirazione delle polveri.
La polvere che viene soffiata fuori dalle celle del filtro durante la pulizia viene raccolta insieme alle particelle di polvere più grandi in un contenitore di raccolta della polvere. Anche questo contenitore deve essere cambiato regolarmente. Come per la sostituzione delle celle filtranti, anche in questo caso è importante rispettare le misure di contenimento adeguate, a seconda della composizione della polvere, in modo da garantire la protezione dei dipendenti.
5. considerazione delle condizioni speciali dei sistemi di depolverizzazione nell’industria farmaceutica
Oltre al rischio per la salute rappresentato dagli ingredienti, c’è anche il rischio rappresentato dall’esistenza della polvere stessa: le aziende farmaceutiche lavorano principalmente sostanze organiche. Queste sono generalmente infiammabili e, in determinate condizioni, possono rappresentare un rischio di esplosione nel processo. Il sistema di filtraggio deve quindi essere dotato di misure adeguate alle esigenze dell’azienda. Un’alternativa sono i sistemi di depolverazione a prova di esplosione che soddisfano i requisiti della Direttiva ATEX 2014/34 applicabile a questi sistemi.
Conclusione
I moderni sistemi di depolverazione svolgono un ruolo fondamentale nella protezione della salute dei tuoi dipendenti, nella tutela dell’ambiente e nell’affidabilità dei processi nella produzione di prodotti farmaceutici. I seguenti criteri dovrebbero essere chiariti in anticipo per facilitare a tutti i soggetti coinvolti la scelta del sistema di depolverazione giusto per garantire la protezione dei dipendenti a lungo termine:
- Esposizione massima alla polvere sul posto di lavoro (OEL)
- Requisiti dell’industria farmaceutica
- Requisiti speciali per i sistemi di filtraggio per la produzione di compresse
- Attrezzature necessarie e misure di manutenzione per i sistemi di filtraggio
- Condizioni speciali per i sistemi di depolverizzazione nell’industria farmaceutica
Prendendo in considerazione questi cinque criteri, dovresti essere in grado di selezionare il sistema di filtraggio ottimale per le esigenze specifiche della tua azienda, garantendo un ambiente virtualmente privo di polvere e sicuro per i tuoi dipendenti e la produzione a lungo termine dei tuoi prodotti.