OEB und OEL – warum diese Begriffe in der Pharmaindustrie entscheidend sind Im Bereich der pharmazeutischen Produktion – insbesondere bei der...
Solida-1: Bayer setzt neue Maßstäbe in der Tablettenproduktion
Wie Digitalisierung, Automatisierung und nachhaltige Filtrationslösungen die Zukunft der Pharmaproduktion gestalten
Automatisierung und Effizienz in der Pharmaproduktion
Ein kalter Herbstmorgen im Chempark Leverkusen. Die ersten Sonnenstrahlen spiegeln sich auf der gläsernen Fassade von Solida-1, der neuesten und modernsten Tablettenfabrik von Bayer. Im Inneren der 15.000 Quadratmeter großen Anlage herrscht absolute Präzision. Hochmoderne Maschinen stehen in durchdachter Anordnung, vernetzt durch ein intelligentes Automatisierungssystem. Durch große Reinraumfenster sind die Produktionslinien zu erkennen, in denen sich Prozesse nahezu lautlos abspielen. Roboterarme bewegen sich synchron, während digitale Sensoren jede kleinste Abweichung registrieren und in Echtzeit korrigieren. Es ist ein Produktionssystem, das sich selbst überwacht und optimiert – eine Fabrik, die nicht nur produziert, sondern lernt.
Hinter der grauen Fassade verbirgt sich eine durchdachte Struktur: Das Werk ist nicht als statische Anlage konzipiert, sondern als modulares System, das flexibel erweitert werden kann. Ein zentraler Bestandteil dieses Konzepts ist der sogenannte Spine, das Rückgrat der Produktion. Dieser zentrale Medien- und Materialversorgungskanal durchzieht die gesamte Anlage und verbindet die verschiedenen Produktionsmodule miteinander. An diesen Spine können jederzeit weitere Module angeschlossen werden, ohne den laufenden Betrieb zu unterbrechen. Die Produktion bleibt so hochgradig anpassbar – eine entscheidende Voraussetzung, um neue Medikamente schneller in die Fertigung zu bringen.
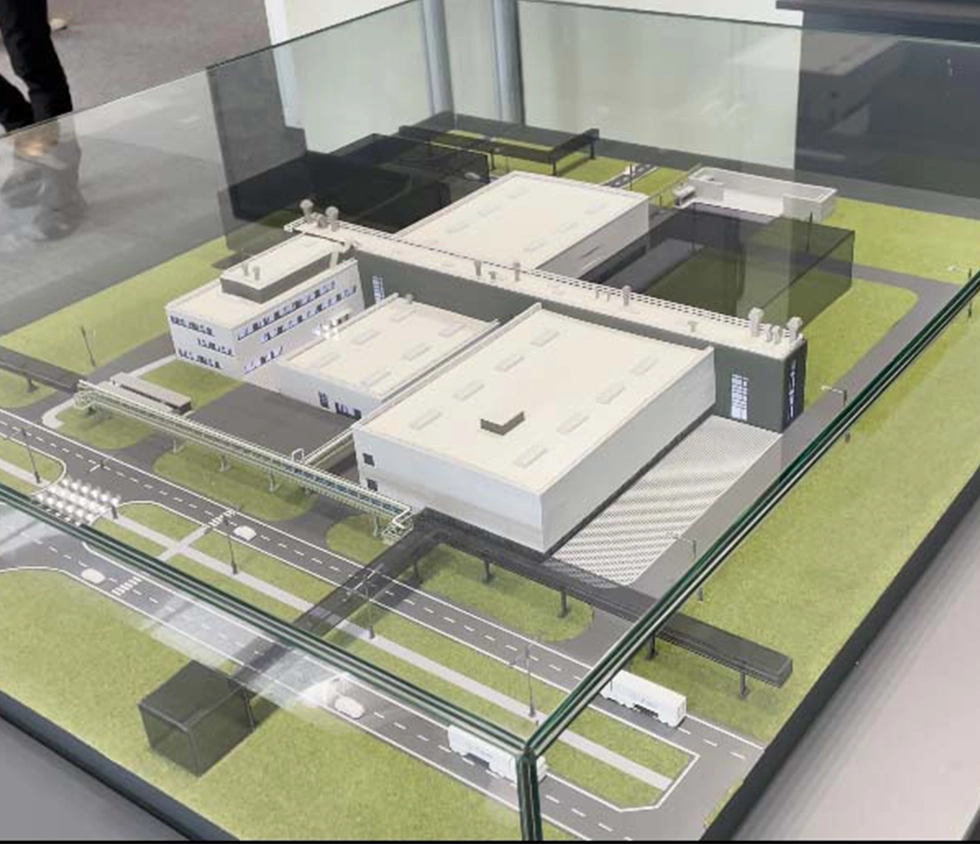
Von der Idee zur Realität: Die Entwicklung von Solida-1
Die Entscheidung für den Bau von Solida-1 fiel bereits 2018. Bayer hatte erkannt, dass herkömmliche Produktionsstrukturen an ihre Grenzen stießen. Lange Durchlaufzeiten, starre Produktionsabläufe und hohe Umrüstkosten machten es schwierig, neue Arzneimittel effizient herzustellen. Die Lösung war ein völlig neues Konzept: eine modulare, digital vernetzte Fabrik, die sich kontinuierlich selbst optimiert.
2021 begann der Bau, und von Anfang an galten strenge Anforderungen an die Reinraumqualität. Bereits während der Errichtung liefen erste Filtrationssysteme, um sicherzustellen, dass keinerlei Partikel oder Verunreinigungen in die sensible Produktionsumgebung gelangten.
Jede Maschinenkomponente wurde unter höchsten Sicherheitsvorkehrungen installiert, um die hohen GMP-Anforderungen zu erfüllen.
Von der Idee zur Realität: Die Entwicklung von Solida-1
Heute, kurz vor der Inbetriebnahme, zeigt sich das Potenzial dieser neuen Produktionsstrategie. Solida-1 ist eine der ersten Anlagen weltweit, die vollständig auf KI-gestützte Prozesssteuerung und automatisierte Materialflüsse setzt. Durch das Ballroom-Konzept, bei dem alle
Produktionsmaschinen in einem einzigen Reinraum untergebracht sind, werden Kreuzkontaminationen minimiert und die Produktionskapazität maximiert.
Luft- und Staubmanagement als Schlüssel zur Reinraumproduktion
Bei der Produktion fester Arzneiformen entstehen an mehreren Prozessstufen feine Stäube und Partikel – sei es während der Granulation, der Tablettierung oder der Beschichtung der Tabletten. In einem hochautomatisierten Werk wie Solida-1 darf dies jedoch nicht dem Zufall überlassen werden. Die kontrollierte Luftführung ist essenziell, um Kreuzkontaminationen zu vermeiden, die Qualität der Produkte zu sichern und die Mitarbeiter vor potenziell aktiven Wirkstoffen zu schützen.
Der gesamte Herstellungsprozess ist darauf ausgelegt, dass Partikel gar nicht erst in die Umgebung gelangen. Bei der Tablettenpressung entstehen durch die hohe mechanische Belastung feine Pulverrückstände, die sofort abgesaugt werden müssen, bevor sie sich im Reinraum verteilen. Ähnlich verhält es sich bei der Wirbelschichtgranulation, bei der Wirkstoffe in Pulverform mit Bindemitteln umhüllt werden, um eine gleichmäßige Granulatstruktur zu erzeugen. Dabei entstehen Aerosole, die gezielt abgeschieden werden müssen, um eine gleichbleibende Qualität zu gewährleisten.
Besonders anspruchsvoll ist die Luftführung im Coating-Prozess, bei dem Tabletten mit einem schützenden Film überzogen werden. Hier entstehen neben feinen Stäuben auch Lacknebel und Lösungsmittelreste, die zuverlässig erfasst und gefiltert werden müssen. Eine ineffiziente Absaugung würde nicht nur die Qualität der Beschichtung beeinträchtigen, sondern auch zu Ablagerungen in der Produktionsumgebung führen.
Damit in den Produktionsräumen selbst optimale Reinraumbedingungen herrschen, befinden sich die dafür notwendigen Filter- und Abluftanlagen in separaten Technikräumen. Hier werden die abgesaugten Luftströme zuverlässig gereinigt, bevor sie sicher abgeführt oder in den Luftkreislauf zurückgeführt werden.
Diese räumliche Trennung reduziert die Partikelbelastung im Produktionsbereich zusätzlich und sorgt für eine maximale Betriebssicherheit. Besonders wichtig ist hierbei das Safe Change-System, das einen kontaminationsfreien Filterwechsel ermöglicht, ohne die Reinraumumgebung zu beeinträchtigen.
Ein zentrales Element dieses Konzepts ist die doppelte HEPA-Filtration, die in kritischen Prozessen eine zusätzliche Schutzebene schafft. Die eingesetzten Anlagen von HET Filter kombinieren gleich drei Schlüsseltechnologien in einem System: Containment, Explosionsschutz und GMP-gerechte Konstruktion. Diese Kombination ermöglicht eine sichere Erfassung hochaktiver Stäube, schützt das System im Fall einer Staubexplosion und erfüllt gleichzeitig alle hygienischen Anforderungen an Materialien, Dichtungen und Reinigbarkeit. Durch diese Integration werden Schnittstellen minimiert, Risiken reduziert und Betriebsabläufe vereinfacht – ein entscheidender Beitrag zur Gesamtsicherheit und zur regulatorischen Konformität der Anlage.
Durch diese durchdachte Luftführung bleibt die Reinraumumgebung stabil, unabhängig davon, welche Wirkstoffe verarbeitet werden. Gleichzeitig wird das Personal entlastet, da manuelle Reinigungsprozesse auf ein Minimum reduziert werden können. Damit ist Solida-1 nicht nur ein Vorreiter in Sachen Effizienz, sondern setzt auch neue Maßstäbe für Sicherheit und Qualität in der pharmazeutischen Produktion.
Sie möchten wissen, wie unsere Filteranlagen auch Ihre Prozesse sicherer und effizienter machen können?
Kontaktieren Sie uns
Nachhaltigkeit als zentrales Element
Die technologische Basis von Solida-1 bildet eine durchgängige digitale Vernetzung aller Produktionsschritte. Sensoren überwachen in Echtzeit sämtliche Prozessparameter – von der Temperatur über die Luftfeuchtigkeit bis hin zur exakten Dosierung der Wirkstoffe. Abweichungen werden automatisch erkannt und durch das Prozessleitsystem SIPAT von Siemens sofort korrigiert.
Fahrerlose Transportsysteme bewegen Rohstoffe autonom von einer Station zur nächsten, sodass der gesamte Produktionsfluss ohne manuelle Eingriffe abläuft. Dies reduziert nicht nur das Risiko menschlicher Fehler, sondern auch den Personalaufwand erheblich. Trotz der hohen Produktionskapazität wird Solida-1 mit einer vergleichsweise kleinen Belegschaft betrieben – die intelligente Automation übernimmt die Routineaufgaben, während sich die Mitarbeitenden auf Prozesskontrolle und Qualitätsmanagement konzentrieren.
Neben Effizienz und Automatisierung spielt auch Nachhaltigkeit eine entscheidende Rolle im Gesamtkonzept von Solida-1. Ein innovatives Geothermie-System versorgt die Anlage mit erneuerbarer Energie und reduziert den CO₂-Ausstoß um 70 % im Vergleich zu herkömmlichen Pharmawerken. Die gesamte Gebäudetechnik ist darauf ausgelegt, Wärme und Kühlung präzise zu steuern und so den Energieverbrauch weiter zu minimieren.
Durch den Einsatz moderner Filtrationslösungen wird zudem sichergestellt, dass Materialverluste reduziert und Filterwechsel sicher durchgeführt werden können. HET Filter trägt mit energieeffizienten Staubabscheidesystemen und langlebigen Filtermedien dazu bei, den ökologischen Fußabdruck der Produktion weiter zu verringern.
Solida-1 ist mehr als eine Fabrik – es ist ein skalierbares Produktionsmodell, das als Vorbild für zukünftige Pharmastandorte dienen könnte. Dank der modularen Architektur und des Spine-Konzepts kann die Anlage jederzeit an neue Anforderungen angepasst werden.
Während die letzten Vorbereitungen für den Produktionsstart laufen, ist bereits klar, dass Solida-1 eine neue Benchmark für die globale Pharmabranche setzt. Die Kombination aus intelligenter Automatisierung, nachhaltiger Energieversorgung und präzisem Staubmanagement macht die Anlage zu einem Vorreiter für die Fabriken von morgen.
Ein Modell für die Zukunft der Pharmaproduktion
Wenn die ersten Tabletten 2026 offiziell vom Band rollen, wird sich zeigen, ob dieses ambitionierte Konzept aufgeht – doch schon jetzt gilt Solida-1 als eines der innovativsten Projekte in der pharmazeutischen Fertigung. Die Zukunft der Arzneimittelproduktion beginnt hier.
Ähnliche Beiträge
Retrofit-Containmentlösungen für bestehende Anlagen: Sicherheit und Compliance wirtschaftlich optimieren
Pharmazeutische und feinchemische Betriebe müssen ihre Produktionsumgebungen regelmäßig an neue Vorschriften anpassen.Strengere GMP-Vorgaben, der...
Digitalisierung in der Filtrationstechnik
Die Digitalisierung ist längst in den produktionsnahen Bereichen der pharmazeutischen Industrie angekommen – mit einem klaren Ziel: mehr Effizienz,...