Le polveri pericolose sono inevitabilmente presenti nell’industria farmaceutica. Le misure di contenimento vengono attuate per ridurre il rischio di contaminazione e garantire così una maggiore protezione dei dipendenti. L’obiettivo di queste misure è creare un’area protetta per i dipendenti e per l’ambiente. Tra le altre cose, vengono utilizzati sistemi di aspirazione delle polveri per estrarre, filtrare e separare in modo sicuro le polveri generate. Tuttavia, poiché la polvere estratta non viene trasportata via, ma solo dal punto di raccolta all’impianto, i sistemi di aspirazione devono essere dotati di misure di contenimento.
In questo articolo scoprirai quali misure tecniche puoi implementare nell’industria farmaceutica per ridurre il rischio di contaminazione e garantire così una maggiore protezione dei dipendenti.
Misure tecniche
I gestori di impianti di produzione hanno il dovere di proteggere i dipendenti dai pericoli che corrono durante il lavoro quotidiano. Questo dovere può essere assolto prendendo in considerazione soluzioni tecniche di contenimento durante la progettazione di un impianto.
Secondo la Direttiva 98/24/CE, nella scelta delle misure di contenimento in questione si deve tenere conto del cosiddetto principio “STOP”:
- Sostituzione dellasostanza a rischio – Verifica se esistono sostanze meno tossiche.
- Misure tecniche: aggiornamento dei sistemi con soluzioni di sicurezza adeguate.
- Misure organizzative: pianificazione per evitare che i dipendenti siano esposti a sostanze pericolose per troppo tempo.
- Dispositivi di protezione personale– Da utilizzare quando tutte le altre misure non sono applicabili.
Le misure utilizzate nell’industria farmaceutica si dividono in due gruppi:
Misure di contenimento primario e misure di contenimento secondario.
Mentre le misure di contenimento primarie assicurano direttamente che nessuna polvere pericolosa possa fuoriuscire dagli impianti di produzione, le misure secondarie servono a catturare le particelle che si formano negli impianti di produzione o a impedirne la diffusione. Tuttavia, ogni caso deve essere valutato singolarmente per determinare quali misure di contenimento siano appropriate. Il fattore decisivo è sempre l’esposizione o il pericolo rappresentato dalle polveri prodotte, oltre ai requisiti (legali) da rispettare (ad esempio GMP, HSE).
Una valutazione del rischio è obbligatoria per determinare il rischio e quindi la portata delle misure. In questa valutazione, il grado di pericolosità della sostanza in questione è legato all’esposizione (durata dell’esposizione).
L’obiettivo è quello di dare priorità alle misure tecniche che forniscono una protezione ottimale ai lavoratori. L’obiettivo dovrebbe essere quello di trovare soluzioni ragionevoli e adatte a ogni fase del ciclo di vita del prodotto. L’obiettivo non è quindi solo quello di rendere sicura la produzione del prodotto, ma anche di proteggere i dipendenti durante l’assemblaggio, lo smantellamento e lo smaltimento dell’impianto di produzione.
Contenimento primario – impedire la fuoriuscita delle particelle
La generazione di polveri pericolose durante la produzione di farmaci è inevitabile. È più sicuro per le persone e per l’ambiente se le polveri e le particelle staccate di sostanze pericolose non fuoriescono dal luogo in cui sono state create: l’impianto di produzione.
Per raggiungere questo obiettivo, esistono diverse opzioni tecniche, alcune delle quali sono elencate di seguito. Combinando le diverse opzioni tra loro, è possibile aumentare al massimo la protezione dei dipendenti e migliorare la facilità d’uso.
Cassetto portaoggetti, RABS e isolante
Per evitare la diffusione delle particelle, è possibile incapsulare e racchiudere l’area di esposizione. A seconda del potenziale di pericolo, questo può essere realizzato con le seguenti misure:
- Glove Box – Scatola con lastra di plexiglas e guanti incorporati
- Cabina RABS (Restricted Access Barrier System) – Cabina con condotti dell’aria integrati Misure
- Isolatore – dispositivo che consente di ottenere una pressione negativa definita e una tenuta estremamente elevata.
Sistemi di estrazione e filtraggio
I sistemi di aspirazione sono utilizzati per estrarre l’aria con le sostanze in essa contenute direttamente nel punto in cui si verifica il fenomeno e rimuoverla dall’area di lavoro del dipendente. L’aria aspirata viene poi filtrata per rimuovere le sostanze pericolose. I cosiddetti estrattori di polvere sono dotati di inserti filtranti che legano le particelle a se stesse e le eliminano dall’aria. Il risultato è un’aria pulita e non contaminata. Le sostanze presenti e la quantità di aria da filtrare determinano il numero di elementi filtranti e la loro classe di filtraggio (quali quantità di particelle di una certa dimensione vengono separate dall’aria).
Differenziazione in base alle dimensioni delle particelleContenimento secondario – prevenire la diffusione delle particelle
Durante i lavori di manutenzione e riparazione o in caso di interruzioni del processo produttivo, il contenimento può essere violato e le sostanze pericolose possono fuoriuscire. In questi casi, i locali di produzione sono progettati per ridurre al minimo il rischio di ulteriore diffusione e contaminazione dei dipendenti e dei locali di produzione adiacenti.
La selezione delle opzioni si basa su un’analisi dei luoghi di lavoro (ad esempio il flusso di materiali, i percorsi del personale, ecc.) e sulla valutazione del rischio delle sostanze coinvolte.
Per il contenimento secondario, ad esempio, sono disponibili le seguenti soluzioni:
Aree di lavoro con chiusure d’aria
L’accesso alle postazioni di lavoro può avvenire solo attraverso le porte d’aria per la decontaminazione. A seconda del progetto, è possibile utilizzare entrate e uscite separate o separare il flusso di materiale dai percorsi del personale. Nelle camere di compensazione, le persone e i materiali vengono ripuliti dai contaminanti che provengono dall’esterno e che rappresentano un rischio per il processo produttivo o per il prodotto. D’altra parte, l’uso delle camere stagne impedisce anche che le sostanze entrino dall’interno e contaminino le aree circostanti.
Aree di lavoro con cascate pressurizzate
Nelle singole aree prevalgono pressioni d’aria diverse, che controllano il movimento delle particelle sospese nell’aria.
- Pressione positiva: si utilizza quando non è consentito l’ingresso di sostanze nella stanza.
- Pressione negativa: si utilizza quando non è consentita la fuoriuscita di sostanze dalla stanza.
Soluzioni per camere bianche
Il concetto di camera bianca garantisce che la quantità di particelle contenute nell’aria rimanga limitata. A questo proposito entrano in gioco diverse normative, tutte finalizzate a ridurre la contaminazione o a facilitare la pulizia. Le norme si applicano, ad esempio, a
- la natura delle superfici: il più ampio possibile per ridurre al minimo il numero di giunzioni e semplificare la pulizia
- la scelta dei materiali – superfici lisce
- la costruzione dei soffitti – stretti, con illuminazione e ventilazione a incasso
- il flusso di materiale: nessun materiale contaminato può lasciare la stanza se non viene effettuata una decontaminazione adeguata o un imballaggio sicuro.
- pulizia dell’aria della stanza – in questo caso, la filtrazione avviene tramite filtri dell’aria di alimentazione e di scarico dotati di celle filtranti adeguate. Si applicano misure simili a quelle previste per il contenimento primario:
- La sostituzione del filtro deve essere effettuata con determinate misure di protezione.
- Le unità di trattamento dell’aria (UTA) devono essere controllate e manutenute regolarmente per quanto riguarda le loro prestazioni. Questo vale, ad esempio, per le prestazioni del filtro una volta installato.
- L’efficienza di filtrazione dei filtri viene verificata attraverso i cosiddetti test DEHS prima della messa in funzione.
Misure di contenimento sui sistemi di filtraggio
Nella progettazione dei processi e dei sistemi di produzione, vengono utilizzate diverse opzioni di protezione per i sistemi di depolverizzazione:
Cambiamento sicuro
Secondo questo principio, i dipendenti possono sostituire le celle filtranti contaminate di un sistema di filtraggio senza entrare in contatto con il materiale filtrante contaminato o con la polvere che potrebbe essere sollevata.
1. rimozione del materiale/della cella filtrante usata
In questo caso, il sistema di filtraggio è dotato di un telaio attorno all’apertura del filtro, sul quale è posizionato un sacchetto protettivo (sacchetto di plastica). Quando si cambia il filtro, un secondo sacchetto di plastica protettivo viene posizionato sul telaio e fissato ermeticamente con un anello di gomma.
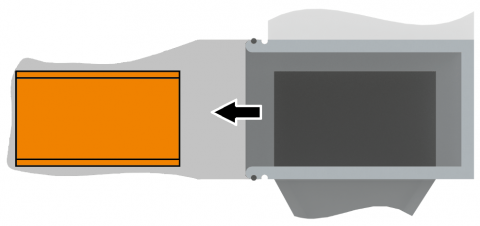
2. chiudere la borsa protettiva
L’elemento filtrante viene inserito nel nuovo sacco di plastica insieme al sacco protettivo esistente (Fig. 1). Questo viene poi chiuso saldamente in due punti tra il telaio e la cella filtrante e separato tra i punti di chiusura (Fig. 2). La parte separata del sacchetto protettivo con la cella filtrante all’interno può essere smaltita correttamente.
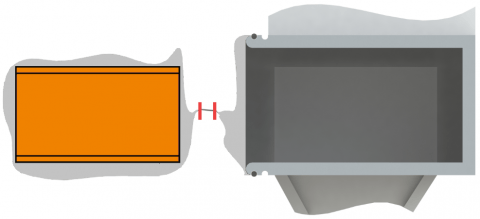
3. introduzione di un nuovo materiale/una nuova cella filtrante
Un nuovo elemento filtrante viene quindi inserito in un nuovo sacchetto protettivo, che viene poi riattaccato al telaio dell’apertura del filtro. Il resto del vecchio sacco protettivo viene rimosso dal telaio dal nuovo sacco protettivo e posizionato dietro la nuova cella in modo da poterla spingere nel sistema filtrante (Fig. 3). Il nuovo sacco protettivo viene arrotolato e riposto dietro il coperchio dell’apertura del filtro.
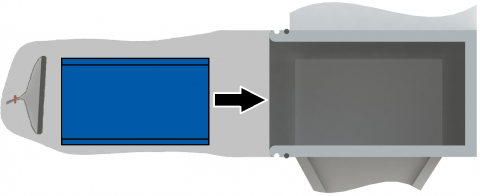
L’uso di sacchetti protettivi assicura che il sistema rimanga sigillato durante l’intero processo e che nessuna sostanza possa fuoriuscire. Per garantire una maggiore sicurezza, la cella filtrante carica può essere inumidita con acqua immediatamente prima della rimozione, in modo da legare la polvere e farla aderire alle celle filtranti. In questo modo si riduce notevolmente la possibile esposizione durante la sostituzione del filtro.
Sistemi di rivestimento infiniti
Il liner infinito è un metodo sicuro per cambiare lo scarico della polvere in un sistema di aspirazione. Consiste in una cartuccia di tubo flessibile in pellicola. La lunghezza del tubo flessibile in pellicola è dimensionata in modo tale che lo scarico possa essere svuotato più volte senza dover cambiare ogni volta il tubo flessibile in pellicola.
Il tubo di pellicola viene chiuso all’estremità inferiore in modo che il materiale possa cadere all’interno. Una volta raggiunto un certo livello di riempimento, il tubo di pellicola viene chiuso in modo sicuro sopra il materiale e tagliato. È importante che la chiusura avvenga in due punti e che il tubo di pellicola sia separato tra i punti di chiusura.
Sistemi di bloccaggio
La scelta dei sistemi di chiusura dipende dalle sostanze coinvolte. Esistono sistemi semplici, come le fascette, che sono sufficienti per le sostanze meno pericolose. Dato che nei punti di chiusura potrebbero rimanere dei residui delle sostanze, per le sostanze più pericolose si consiglia l’uso di sistemi di chiusura speciali. Questi consistono in fascette che chiudono ermeticamente il sacco protettivo e in strumenti speciali per separare le fascette in modo da evitare la fuoriuscita di polvere.
Pulizia del sistema di filtraggio dall’interno
Oltre alle misure già citate che vengono utilizzate durante il funzionamento, ci sono anche diverse opzioni che vengono utilizzate durante la manutenzione e la riparazione dei sistemi. Ad esempio, gli interni dei sistemi possono essere lavati con acqua prima dell’apertura, in modo da legare la polvere:
Wash-In-Place (WIP):
Prima di aprire il sistema, le superfici vengono inumidite con acqua per legare la polvere. Per ottenere un effetto di pulizia completo, è necessaria una successiva pulizia manuale.
In questo caso, l’interno del sistema viene completamente pulito prima di effettuare interventi di manutenzione o riparazione. La pulizia deve essere sempre qualificata e convalidata per i processi che entrano in contatto con il prodotto.
Conclusione
Nell’industria farmaceutica esistono diversi modi per proteggere i dipendenti e i processi dalle sostanze pericolose. Questi possono essere determinati utilizzando il principio STOP. Quando si scelgono le misure tecniche per i sistemi di aspirazione delle polveri, è fondamentale analizzare i processi stessi e le sostanze che si formano prima. Il pericolo risultante determina il grado di contenimento da utilizzare.
Nell’industria farmaceutica, le applicazioni possono essere suddivise in due gruppi: Misure di contenimento primarie, che assicurano l’assenza di fuoriuscite di polveri pericolose, e misure di contenimento secondarie, che catturano le particelle che si formano e ne impediscono la diffusione. Combinando diverse misure tecniche sui sistemi di aspirazione delle polveri, si aumenta al massimo la facilità d’uso per i dipendenti e la sicurezza sul lavoro e si previene la contaminazione.
I moderni sistemi di depolverizzazione svolgono un duplice ruolo in questo caso: da un lato, servono come misura di contenimento tecnica indipendente; dall’altro, devono essere adottate misure di contenimento per proteggere i dipendenti e l’ambiente durante l’utilizzo.