I depolveratori o sistemi di filtraggio sono utilizzati nell’industria farmaceutica e chimica per legare la polvere che si crea durante la produzione. Le celle filtranti installate in questi sistemi separano le particelle dall’aria, ottenendo aria pulita ed eliminando il rischio di polvere.
Il tipo di polvere o la composizione della miscela d’aria e i requisiti del processo determinano i criteri di selezione delle celle filtranti.
Le celle filtranti sono disponibili in vari tipi, design e materiali. Il seguente articolo fornisce una breve panoramica dei design e delle classificazioni dei filtri.
Per poter confrontare le diverse versioni delle singole celle filtranti tra loro o per confrontarle con i requisiti del processo, esiste un sistema di classificazione definito sulla base di standard.
La corretta selezione e manutenzione dei sistemi di filtrazione e dei loro componenti è fondamentale per assicurare la qualità dell’aria, garantire la sicurezza e l’efficienza del processo produttivo e assicurare la conformità alle normative ambientali e sanitarie. Il seguente articolo fornisce una panoramica dettagliata dei diversi design, gruppi di filtri e classificazioni di filtri per aiutare i professionisti del settore a scegliere la soluzione di filtrazione migliore per le loro esigenze specifiche.
Classificazione delle celle filtranti
Per poter classificare correttamente le varie classi di filtri o gruppi di filtri, occorre innanzitutto fornire una panoramica dei filtri dell’aria in esame per capire quale classificazione si applica.
Panoramica dei filtri dell’aria
I filtri dell’aria sono classificati in base alla loro capacità di separare particelle di diverse dimensioni.
Esistono “filtri antipolvere” che vengono utilizzati per carichi di polvere elevati e particelle più grossolane nell’aria. Questi sono ulteriormente suddivisi in “filtri per polveri grossolane” e “filtri per polveri fini”, a seconda della dimensione delle particelle. Questi filtri sono classificati secondo lo standard EN ISO 16890.
Se si vogliono filtrare particelle più sottili o molto fini, si utilizzano i “filtri HEPA”. In questo caso esiste un’ulteriore suddivisione in “filtri HEPA standard” e “filtri HEPA ad alte prestazioni”. Anche in questo caso, la classificazione si basa sulla dimensione effettiva delle particelle. La classificazione si basa sullo standard EN 1822-1.
Classificazione secondo la norma EN ISO 16890
La classificazione si basa sull’efficienza di filtrazione della cella filtrante. Questa indica quante particelle vengono trattenute dal mezzo filtrante o quante particelle si trovano ancora nell’aria di scarico dopo aver attraversato il filtro. Il valore importante è l’efficienza di separazione delle particelle di dimensioni comprese tra 0,3 µm e 10 µm.
Questo valore può essere utilizzato per assegnare il gruppo di filtri corrispondente in conformità allo standard EN ISO 16890.
Lo standard prevede 3 livelli di classificazione delle celle filtranti:
- PM1: efficienza di separazione per particelle fino a 1 µm (0,3-1 µm)
- PM2.5: efficienza di separazione per particelle fino a 2,5 µm (0,3-2,5 µm)
- PM10: efficienza di separazione per particelle fino a 10 µm (0,3-10 µm)
Se almeno il 50% delle particelle specificate viene separato, la cella filtrante ha raggiunto il gruppo corrispondente. In questo caso si parla di “efficienza minima”, che viene determinata su una nuova cella filtrante. Allo stesso tempo, viene misurata anche l'”efficienza media” sull’intera cella filtrante.
Nel processo di determinazione del gruppo di filtri, viene quindi prima determinata l’efficienza minima per le 3 dimensioni delle particelle e l’efficienza media. Per la fase in cui si ottiene almeno il 50% della separazione, si prende l’efficienza media e la si arrotonda per difetto al 5 più vicino.
Questi valori possono essere utilizzati per specificare la classificazione.
Esempio: ISO ePM2.5 80%
Se una cella filtrante soddisfa le condizioni per diverse fasi, spetta al produttore delle celle filtranti decidere quali informazioni includere nel prodotto.
Classificazione secondo la norma EN 1822-1
La norma DIN EN 1822-1 riguarda la categorizzazione dei filtri antiparticolato ad alte prestazioni e dei filtri HEPA ad alte prestazioni utilizzati nella tecnologia delle camere bianche o nell’industria farmaceutica. Oltre alla categorizzazione delle celle filtranti, la norma specifica anche la produzione e i test. Va notato che la Parte 1 della norma DIN EN 1822 si applica alla classificazione dei filtri; tuttavia, le specifiche per la produzione e il collaudo si trovano nelle Parti 2-5 della norma ISO 29463.
La norma DIN EN 1822-1 distingue tra gruppi di filtri e classi di filtri:
Filtergruppe | Filterklasse | Integralwert Abscheidegrad im MPPS | Integralwert Durchlassgrad im MPPS | Lokalwert Abscheidegrad im MPPS | Lokalwert Durchlassgrad im MPPS |
---|---|---|---|---|---|
EPA = Hochleistungs- Partikelfilter | E10 E11 E12 | ≥ 85 % ≥ 95 % ≥ 99,5 % | ≤ 15 % ≤5% ≤ 0,5 % | - - - | - - - |
HEPA = Schwebstofffilter | H13 H14 | ≥ 99,95 % ≥ 99,995 % | ≤ 0,05 % ≤ 0,005 % | ≥ 99,75 % ≥ 99,975 % | ≤ 0,25 % ≤ 0,025 % |
ULPA = Hochleistungs- Schwebstofffilter | U15 U16 U17 | ≥ 99,999 5 % ≥ 99,999 95 % ≥ 99,999 995 % | ≤ 0,000 5 % ≤ 0,000 05 % ≤ 0,000 005 % | ≥ 99,997 5 % ≥ 99,999 75 % ≥ 99,9999 9 % | ≤ 0,002 5 % ≤ 0,000 25 % ≤ 0,000 1 % |
La base della categorizzazione è l’efficienza minima di filtrazione della cella filtrante per particelle di dimensioni 0,1 – 0,3 µm, il “MPPS”, come spiegato nell’articolo Principio del fattore di influenza del filtro.
La classificazione avviene in tre fasi: in primo luogo, viene determinata la dimensione delle particelle al minimo di separazione sul mezzo filtrante dispiegato (MPPS). Nella seconda fase, si verifica l’assenza di perdite (= efficienza di separazione locale). Infine, l’efficienza di separazione integrale dell’elemento filtrante viene determinata utilizzando un aerosol di prova per la dimensione delle particelle al minimo di separazione.
In base ai valori ottenuti, l’elemento filtrante può essere assegnato alla classe di filtro corrispondente con l’aiuto della panoramica dello standard.
La seguente illustrazione mostra le aree in cui è possibile utilizzare le varie classi o gruppi di filtri.
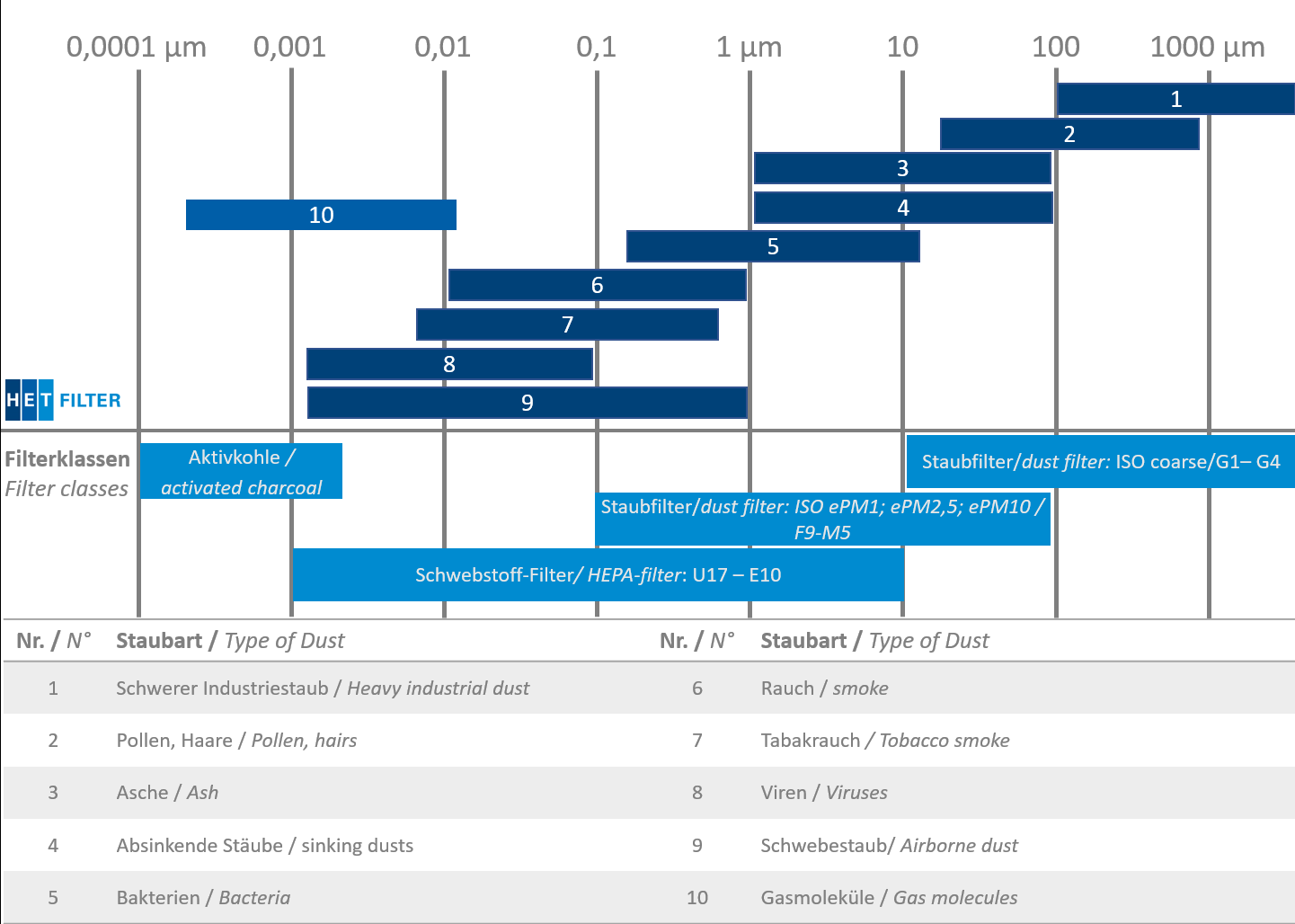
Progetti di celle filtranti
A seconda del produttore, dell’applicazione e dei requisiti, sono disponibili diversi design per gli elementi filtranti.
Diversi fattori giocano un ruolo nella scelta: dai requisiti di processo, alla situazione di installazione derivante dalla progettazione del sistema di filtraggio, fino alla questione dei costi, ci sono molti aspetti da considerare.
In questo articolo daremo un’occhiata ai modelli di “filtro a cartuccia”, “filtro a lamelle” e “filtro a cassetta”, ovvero i filtri utilizzati nei sistemi di HET Filter GmbH.
I tre modelli di filtro hanno proprietà diverse, descritte di seguito:
Filtro a cartuccia
Struttura:
Nei filtri a cartuccia, il materiale filtrante pieghettato (vello filtrante) si trova all’interno di un cestello cilindrico. Questo design consente una produzione economicamente vantaggiosa.
Applicazione: per aria con elevati carichi di polvere
Classificazione: Filtro grossolano e fine secondo la norma EN ISO 16890
Caratteristiche speciali: a causa del suo design, il filtro non può essere cambiato in condizioni di sicurezza, ovvero con questo filtro è possibile soddisfare solo requisiti di contenimento minori. Questi sono descritti negli articoli del blog dedicati al tema “Contenimento”.
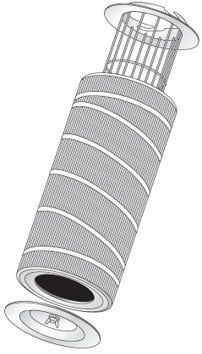
Filtro lamellare
Struttura: I filtri a lamelle sono costituiti da un tessuto plissettato che può essere installato sia in orizzontale che in verticale.
Il rispettivo stadio filtrante di un aspiratore è composto da diversi filtri a lamelle.
Grazie al loro design, i singoli filtri a lamelle possono essere puliti con aria compressa pulsata.
L’aria compressa fa vibrare gli elementi, in modo che le particelle si stacchino e cadano nello scarico della polvere.
Grazie al design semplice, questo tipo di filtro è relativamente vantaggioso.
Utilizzo: per aria con carichi di polvere elevati, per polveri difficili
Classificazione: Filtro grossolano e fine secondo la norma EN ISO 16890
Caratteristiche speciali: a causa del suo design, il filtro non può essere cambiato in condizioni di sicurezza, ovvero con questo filtro è possibile soddisfare solo requisiti di contenimento minori. Questi sono descritti negli articoli del blog dedicati al tema “Contenimento”.
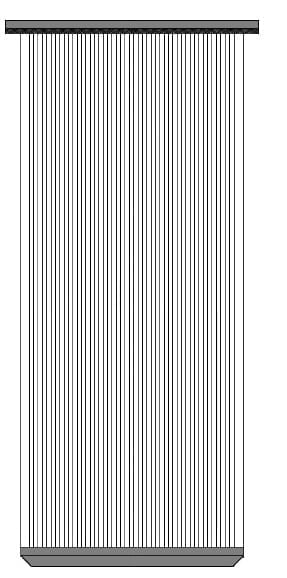
Filtro a cassetta
Costruzione:
Con il filtro a cassetta, il mezzo è contenuto in un robusto alloggiamento conduttivo realizzato in acciaio zincato o in acciaio inox.
Per l’utilizzo in aree non potenzialmente esplosive, il telaio può essere realizzato anche in legno (MDF). Il vello filtrante viene piegato a strati o a V e modellato sull’alloggiamento utilizzando un composto di fusione.
Tra i singoli strati sono presenti dei distanziatori che assicurano che gli strati rimangano aperti durante l’aspirazione dell’aria e che l’aria possa fluire senza ostacoli attraverso il filtro.
Sono inoltre conduttivi per evitare cariche elettrostatiche.
Applicazione: per le polveri più fini dell’industria farmaceutica, Carichi di polvere fino a 2.000 mg/m3 Flussi di volume fino a 2.000 m3/h Può essere utilizzato in diversi sistemi grazie alle dimensioni standardizzate.
Classificazione: filtro HEPA secondo EN 1822; filtro antipolvere secondo EN ISO 16890
Caratteristiche speciali: il filtro può essere sostituito in condizioni di sicurezza, ovvero può essere utilizzato per soddisfare i requisiti di contenimento fino a OEB6, tra gli altri. Le celle del filtro possono essere pulite, il che ne aumenta la durata.
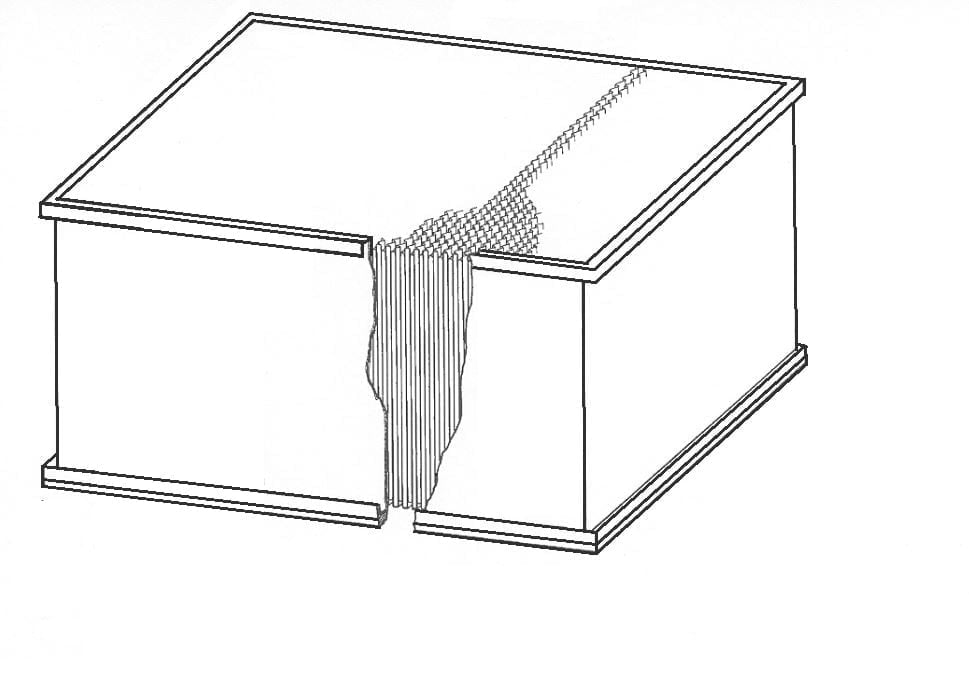
Conclusione
Le celle filtranti sono disponibili in un’ampia gamma di proprietà e opzioni di design. La scelta dipende dalle proprietà della polvere e dai requisiti del processo. Per la progettazione dei sistemi di filtraggio è quindi fondamentale conoscere con precisione le polveri e trasmettere i dati ai produttori dei gruppi filtranti. Solo in questo modo è possibile selezionare gli elementi filtranti giusti, in modo che il loro compito sia assolto: fornire aria pulita senza alcun pericolo per le persone o l’ambiente.